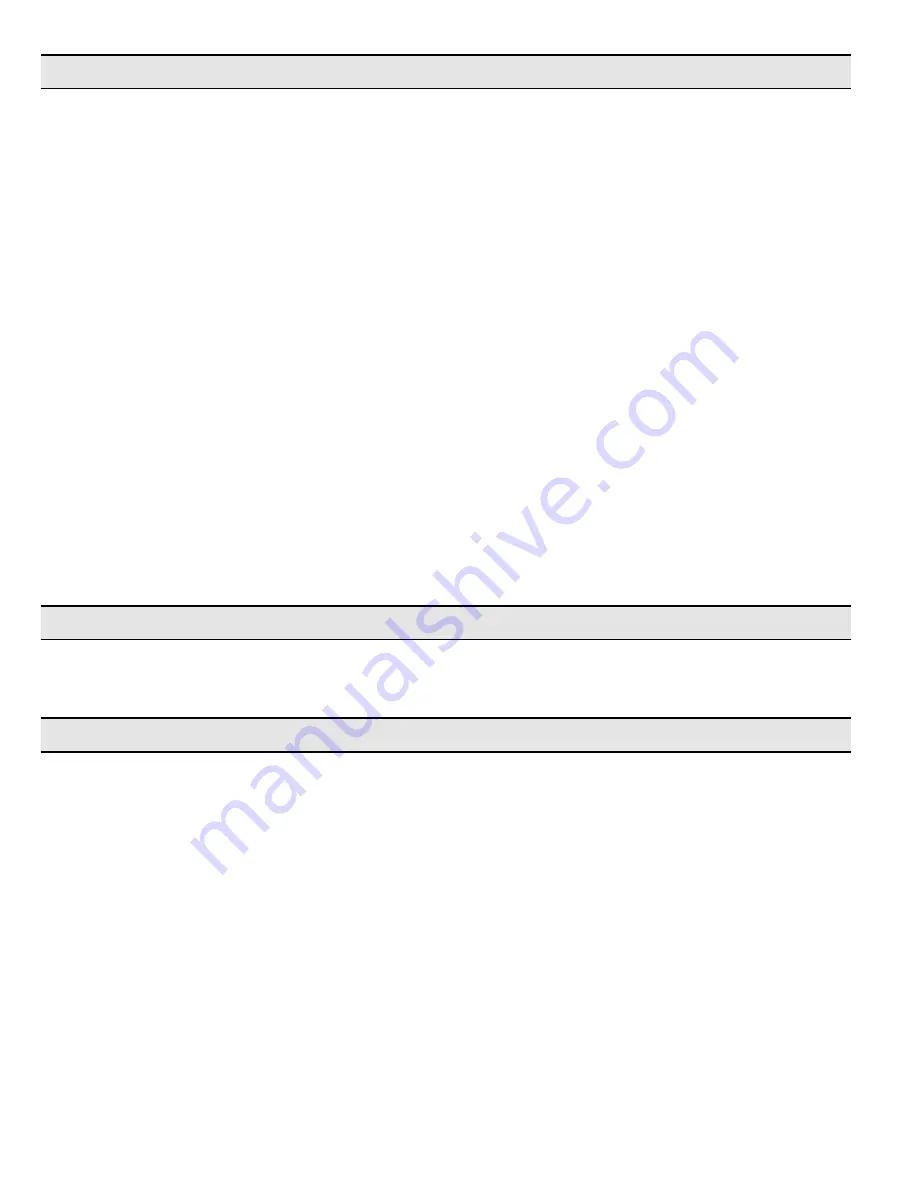
Pump/Motor Base Assembly
The pump/motor base assembly must be mounted in the
horizontal position. The system can be run at 15 degrees
on any plane to the horizontal and may be run intermittent-
ly at 30 degrees to the horizontal plane. The base of the
system must be anchored to a surface or structure that is
ridged and of adequate strength to withstand the vibration
and stresses of apparatus operation. The drawings on
page 10 provide the mounting dimensions for the Hypro
High Pressure pump/motor base assembly. Flexible hose
is required to make the hose connections to the Hypro
High Pressure System. DO NOT hard pipe the system.
Protect the hoses and wiring to prevent chafing and abra-
sion during operation of the foam system. Protect the foam
pump base unit from excessive spray and debris. See
engine manual for allowed engine operating conditions.
Line Strainers
There are two line strainers provided with theTurbo Stream
unit. The pump inlet line strainer has 3/4-inch NPT female
threaded ports and is to be installed on the water inlet of
the foam pump. The water supply hose should have ade-
quate wall stiffness to withstand the vacuum of the pump
while it is in operation (23 in. [584 mm] Hg and 50 psi [3
BAR]).
NOTE
: If a pressurized water flush from one of the dis-
charges is incorporated, the plumbing and line strainer
exposed to this pressure must be rated at or above the
operating pressure of all other discharge components
(1800 psi [124.1 BAR] minimum).
Check Valves
A 3/4-inch check valve is included at pump inlet. A foam
injection check valve is included.
Flushing System
Depending on the corrosiveness of the foam concentrates
to be used, a flushing system may be required in the foam
concentrate injection system. Most Class A foam concen-
trates (per NFPA 1150) are less corrosive and therefore
may not require flushing. It is important to flush and drain
the entire system before long periods of storage to prevent
component malfunction.
Thermal Relief Valve
A thermal relief valve is included with the system to pre-
vent pump overheating during unloading.
-6-
Plumbing Component Installation -
continued
Electrical Equipment Installation
Making Sure Everything is Working Right
Electrical Connections
See engine manual for detailed electrical connections only if engine is equipped with electric start.
System Check
Check fuel level and oil level per engine manual prior to running system. Check pump and gear case oil level prior to running
system. Pump and gear case should be filled with oil per manual instructions.
Check the function of all components before using the system. Also check that all plumbing and components are tight and
functional.
Check to see that water supply lines, strainers and foam tank lines are free of debris and plumbed correctly. Any leaks in the
system will cause poor system performance and operation.
L-1530 (5/11 Rev. B)
Summary of Contents for Turbo Stream 1508B-130EFS
Page 11: ...11 Notes L 1530 5 11 Rev B...