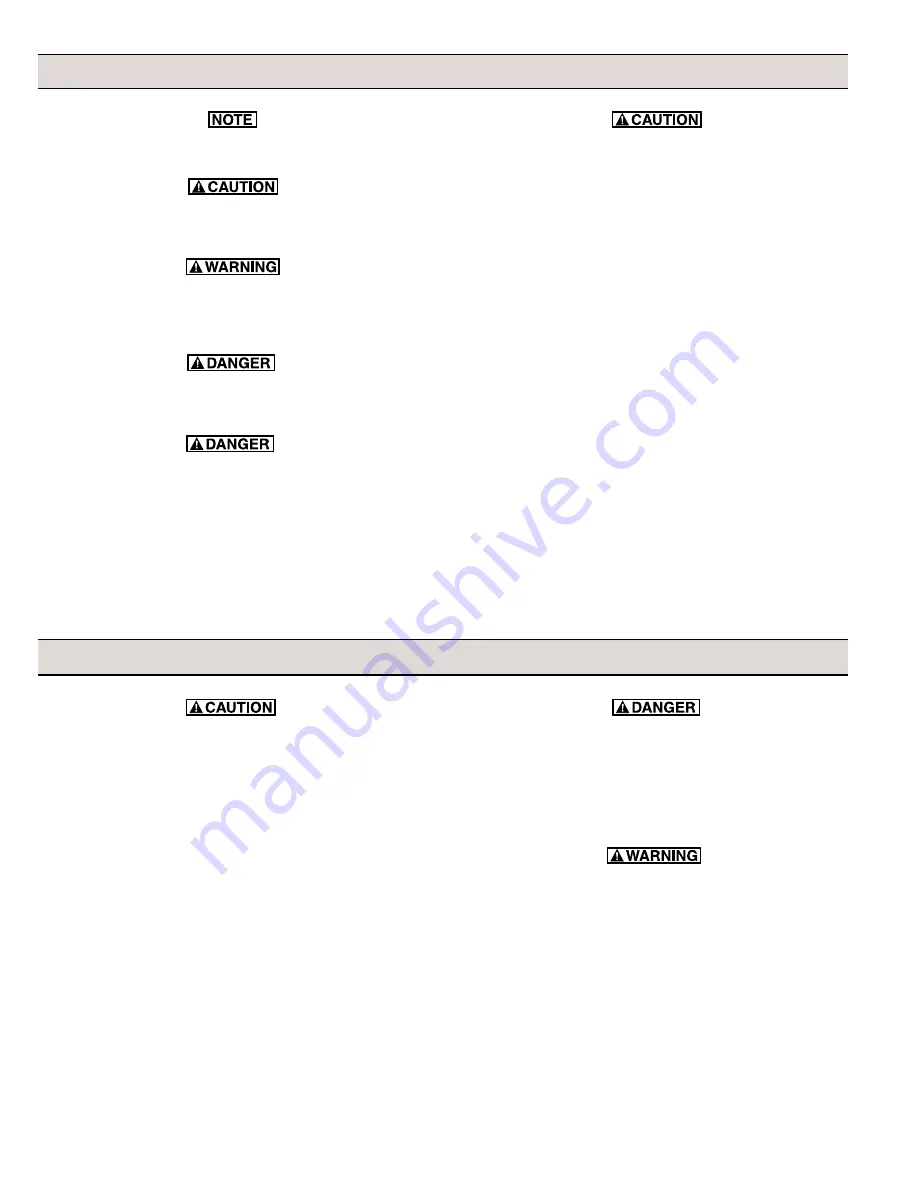
-2-
General Safety Information
Notes are used to notify of installation, operation, or maintenance
information that is important but not safety related.
Caution is used to indicate the presence of a hazard, which will
or can cause minor injury or property damage if the notice is
ignored
Warning denotes that a potential hazard exists and indicates
procedures that must be followed exactly to either eliminate or
reduce the hazard, and to avoid serious personal injury, or
prevent future safety problems with the product.
Danger is used to indicate the presence of a hazard
that will result in severe personal injury, death, or property
damage if the notice is ignored.
Do not pump flammable or explosive fluids such as gasoline,
fuel oil, kerosene, etc. Do not use in explosive atmospheres.
The Pump should be used only with liquids compatible with the
Pump component materials. Failure to follow this notice can
result in severe personal injury and/or property damage and will
void the product warranty.
1.
Do not pump at pressures higher than the maximum
recommended pressure.
2.
Maximum liquid temperatures is 140
o
F for Series 9300
centrifugal pumps.
3.
Disconnect power before servicing.
4.
Release all pressure within the system before servicing any
component.
5.
Drain all liquids from the system before servicing any
component. Flush with water.
6.
Secure the outlet lines before starting the pump. An unsecured
line may whip, causing personal injury and/or property
damage.
7.
Check hose for weak or worn condition before each use.
Make certain that all connections are tightly secured.
8.
Periodically inspect the pump and the system components.
Perform routine maintenance as required (See Repair
Instructions).
9.
Use only pipe, hose and fittings rated for the maximum psi
rating of the pump.
10. Do not use these pumps for pumping water or other liquids
for human or animal consumption.
1.
Always drain and flush pump before servicing or
disassembling for any reason.
2.
Always drain and flush pumps prior to returning unit
for repair.
3.
Never store pumps containing hazardous chemicals.
4.
Before returning pump for service/repair, drain out
all liquids and flush unit with neutralizing liquid.
Then, drain the pump. Attach tag or include written
notice certifying that this has been done. It is illegal
to ship or transport any hazardous chemicals without
United States Environmental Protection Agency
Licensing.
Hazardous Substance Alert
Never use your hand to check the condition of hydraulic
lines or hoses. If hydraulic fluid penetrates the skin, get
medical help immediately. Failure to get proper medical
help may result in loss of limb or life. The safest way to
check hydraulic lines or hoses is by holding a piece of
cardboard next to the hydraulic line or hose.
The sound pressure level of the Pump is 80dBA.
Observe all safety precautions when operating the Pump
within close proximity for extended periods of time by
wearing hearing protectors. Extended exposure to
elevated sound levels will result in permanent loss of
hearing acuteness, tinnitus, tiredness, stress, and other
effects such as loss of balance and awareness.