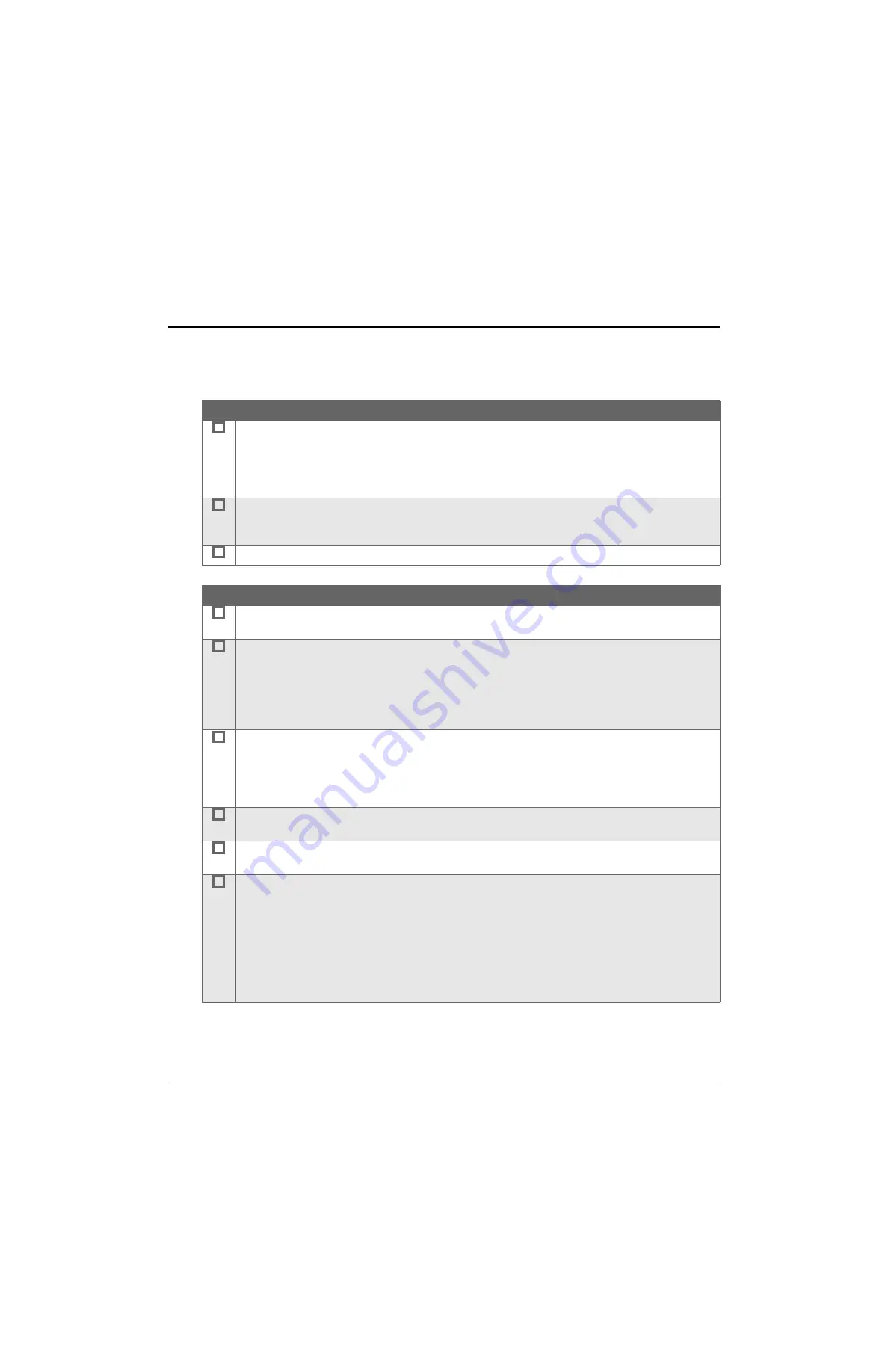
Prepare to Troubleshoot Internal Components
2
Powermax65/85/105 SYNC
Troubleshooting Guide
810430
17
Troubleshooting checklist
Make sure that operators go through the following checklist before you remove the cover from the
plasma power supply and examine internal components.
Examine the power source
Can the power source supply sufficient power to the plasma power supply for the applications that
you are doing?
If you are using a generator, make sure that it has sufficient power to let you do a full plasma arc
stretch. Refer to
on page 62. For power requirements for generators, refer
to the
Powermax65/85/105 SYNC Operator Manual
(810470).
Are the circuit breakers or fuses sufficient for your plasma power supply and for the applications that
you are doing? The recommended fuse / breaker sizes let the input current increase quickly when you
stretch the plasma arc.
Did the circuit breaker open (trip)?
Make sure that the mechanized cutting system is grounded and set up correctly (if applicable)
Is the mechanized cutting system correctly grounded or bonded? For information on grounding best
practices, refer to the
Powermax65/85/105 SYNC Mechanized Cutting Guide
(810480).
Does the routing of all cables keep electromagnetic interference (EMI), also called noise, to a
minimum? For information on best practices to decrease noise, refer to the
Powermax65/85/105 SYNC Mechanized Cutting Guide
(810480).
For example, keep the torch lead and work lead together by using cable ties or intertwining them like
a twisted pair. Also keep the routing of the torch lead and work lead separate from the shielded
cables and from all other components of the mechanized cutting system.
Does other industrial equipment share the same ground as the plasma power supply? This can cause
noise problems.
For example, do you have an inverter-type welder with a work lead that is connected to the same
cutting table (or workpiece) as the plasma power supply? Disconnect the welder from power, and
remove its work lead from the cutting table.
Is excess cable wound into coils? This can cause noise problems. Instead, put the excess cable
down flat or in a figure-8 shape.
If you are using torch height control (THC), is an ohmic contact ring (428895) installed on the
Hypertherm cartridge? Is the ohmic contact ring connected correctly to the THC?
If you are using torch height control (THC) and are connecting to raw arc voltage directly, is the
wiring correct?
• Is the correct wire gauge used?
• Are the wires connected to the correct locations on the power PCB?
• Are the wires fully tightened?
Incorrect wiring can cause noise problems and in some cases can cause severe damage to the
plasma power supply. For instructions on how to correctly connect to raw arc voltage, refer to the
Powermax65/85/105 SYNC Raw Arc Voltage Field Service Bulletin
(810320).
Summary of Contents for Powermax105
Page 1: ...Powermax65 85 105 SYNC Troubleshooting Guide 810430 REVISION 0 ENGLISH ...
Page 12: ...Before You Begin 1 12 810430 Troubleshooting Guide Powermax65 85 105 SYNC ...
Page 174: ...System Diagrams 8 174 810430 Troubleshooting Guide Powermax65 85 105 SYNC ...
Page 180: ...System Diagrams 8 180 810430 Troubleshooting Guide Powermax65 85 105 SYNC ...