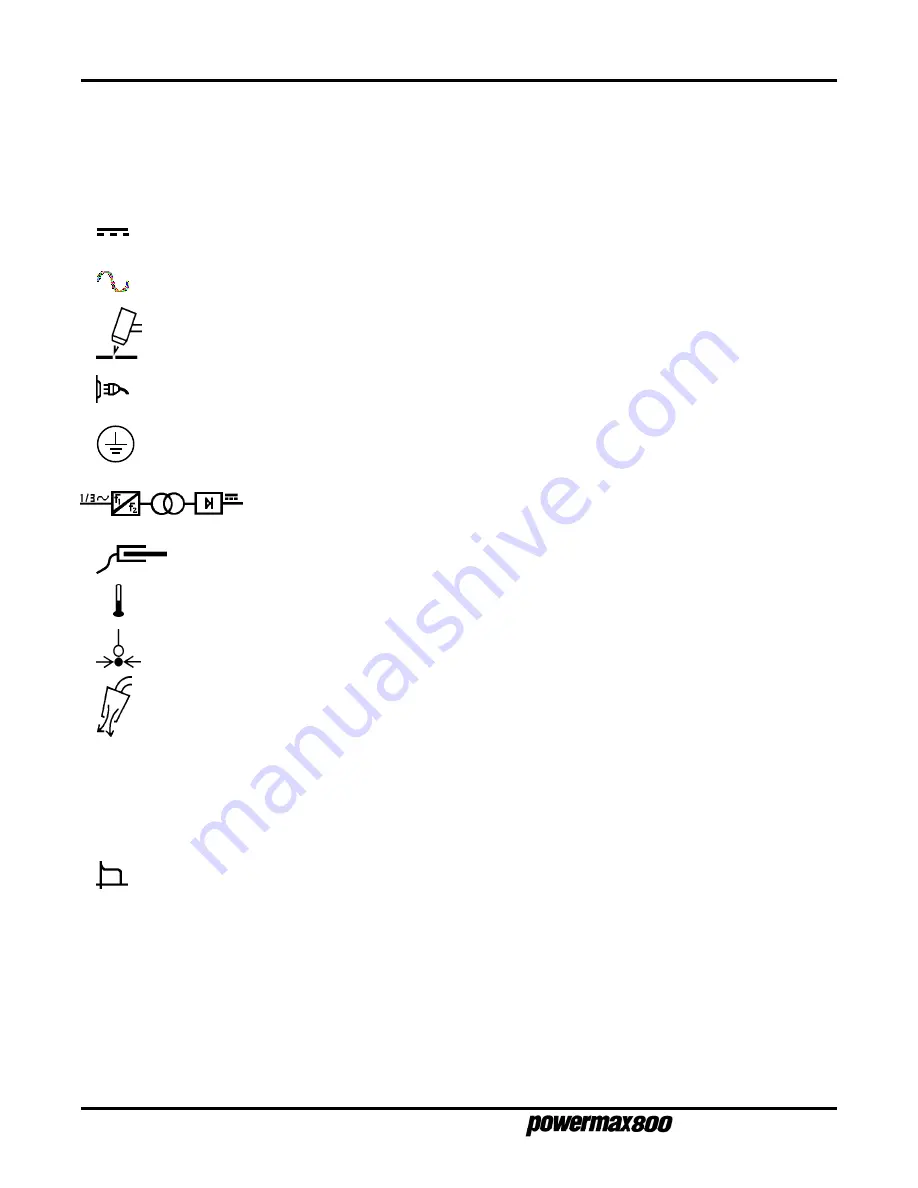
2-6
D
ESCRIPTION
& S
PECIFICATIONS
Operator Manual
O
I
Direct Current (DC)
Alternating current (AC)
Plasma cutting torch
AC input power connection
The terminal for the external protective (earth) conductor
An inverter-based power source
Anode (+) work clamp
Temperature switch
Pressure switch
Plasma torch in the TEST position (cooling and cutting gas exiting nozzle)
Power is on
Power is off
Volt/amp curve, "drooping" characteristic
IEC SYMBOLS USED
9-96