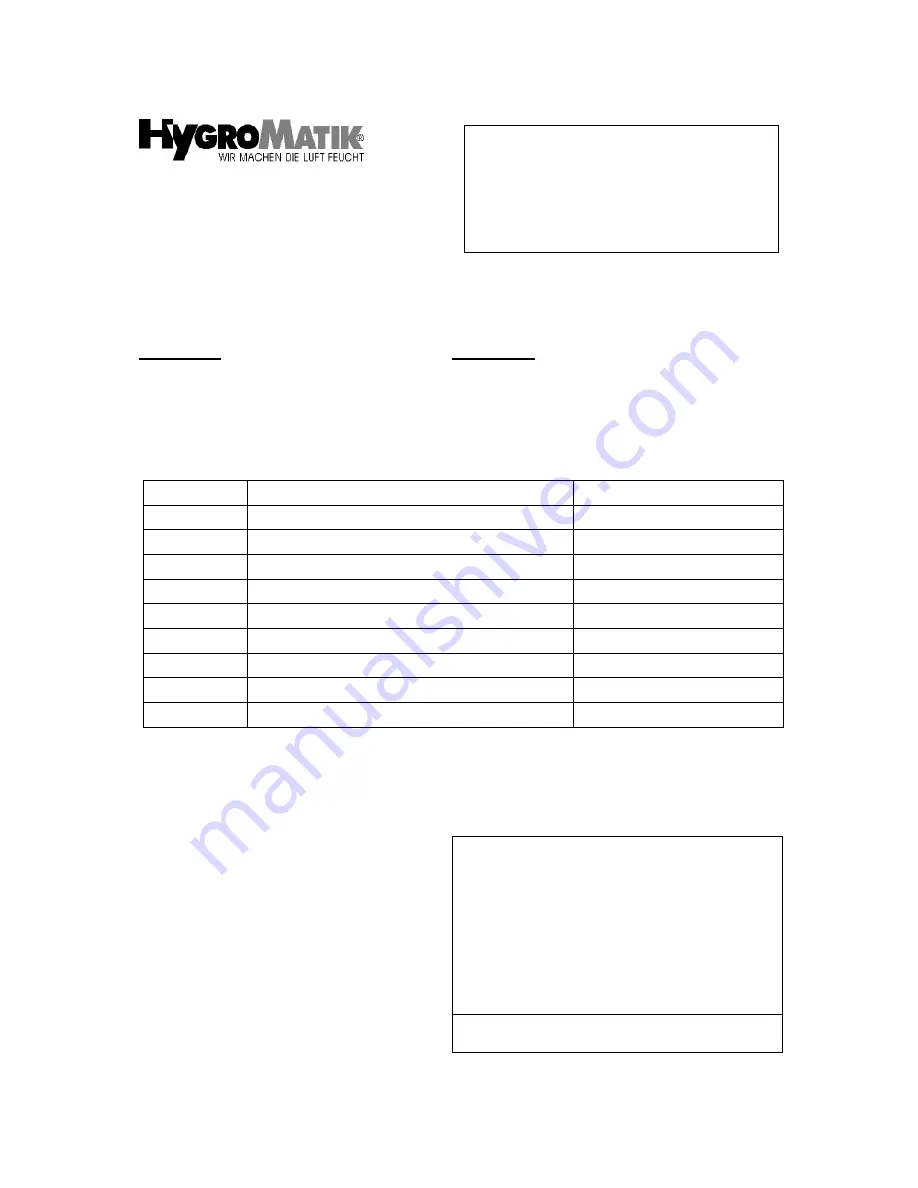
company stamp (invoice address)
Lise-Meitner-Str. 3
24558 Henstedt-Ulzburg
Tel. 04193/895-0
Order for spare parts
unit type
٭
_________________
serial
no
.
٭
___________________
commission: ________________ order no: ______________________
date of delivery ____________forwarder _____________ shipment by ___________
delivery address (if different from
invoice address)
__________________________
__________________________
__________________________
__________________________
__________________________
__________________________
٭
Order can only be processed if unit type and unit serial number are filled in.
quantity
article
article no
Fax Form
Please copy, fill in and fax to
Fax.No
.
+49
(
0)4193/895-33
date/signature
Summary of Contents for DBV-U126P
Page 1: ......
Page 42: ...DBV U P 2 9 2 9 Drill Pattern 2 9 1 Drill Pattern DN 25...
Page 43: ...2 10 DBV U P 2 9 2 Drill Pattern DN40...
Page 54: ......
Page 55: ......
Page 56: ......
Page 57: ......
Page 58: ......
Page 59: ......
Page 60: ......