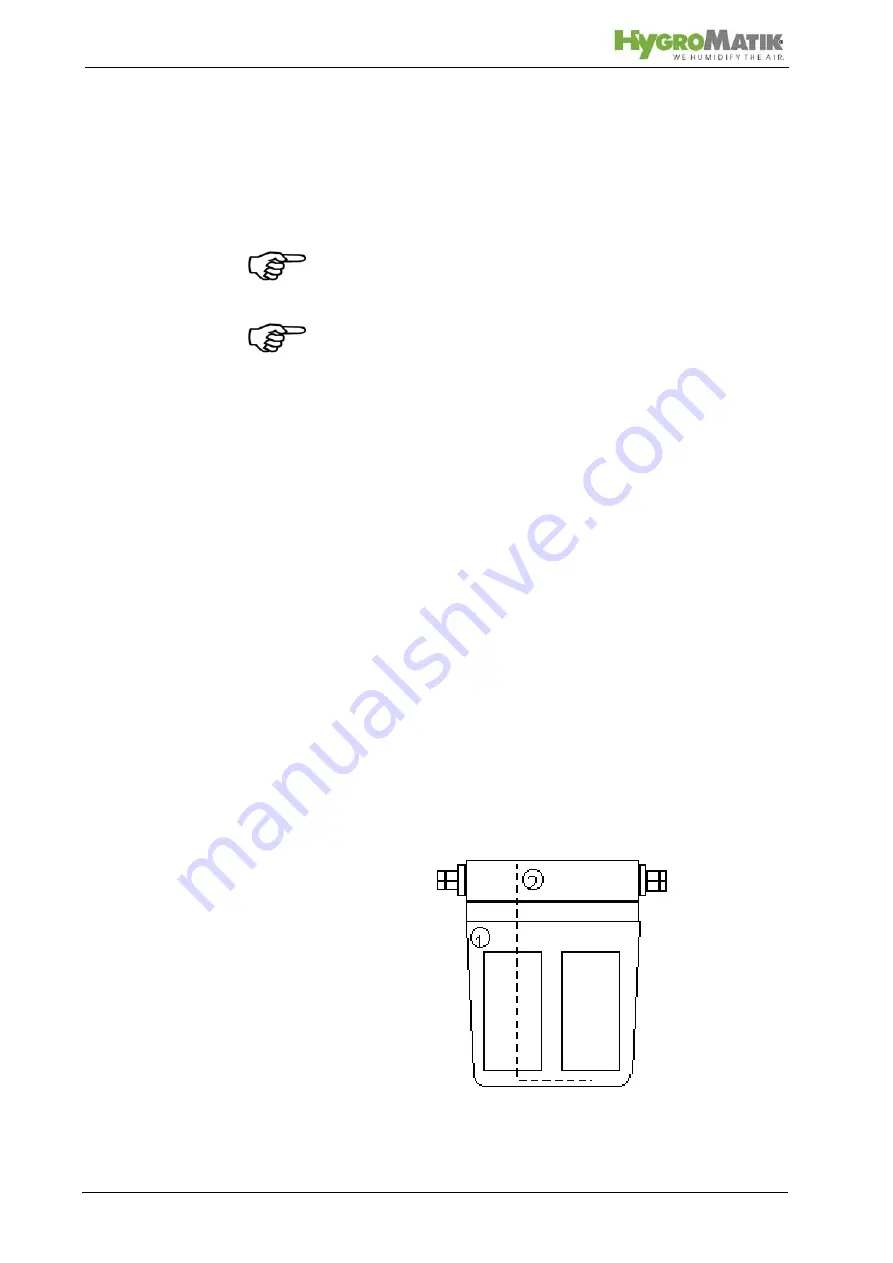
Page 46
9.6
Cleaning the Water Filter
Replace the water filter cartridge in the water filter at least twice
a year Replace the water filter cartridge sooner if there is a high
level of impurities.
Note:
A fouled water filter leads to inceased pressure loss. This
can cause a fall in the nozzles' atomisation output.
Note:
The pressure loss can be determined by placing a mano-
meter in front of and behind the water filter. If pressure loss is
increasing, clean the water filter and replace the filter cartridge.
»
Shut off the nozzle system as specified in Section 5.3.
»
Unscrew the lower part (1) of the water filter. Turn coun-
terclockwise.
»
Remove water filter cartridge (2).
»
Clean the inner surface of the water filter housing with a
clean cloth.
»
Thoroughly rinse out the lower part (1) of the filter with
drinking water.
»
Insert new water filter cartridge.
»
Screw the lower part of the filter back on.
»
Start up nozzle system as specified in Section 5.2.
water filter
Summary of Contents for CU-1
Page 1: ...Atomising Vacuum Nozzle System Manual...
Page 37: ...Page 37 5 4 Example of Installation Fig Example of installation a VN Unit with 4 nozzles...
Page 38: ...Page 38 Fig Example of installation a VN Unit with 8 VN nozzles and 2 vacuum valves...
Page 48: ...Page 48 10 EC Declaration of Conformity...
Page 54: ...Page 54 General 39 Water Installation 39 Wiring Diagram 42...