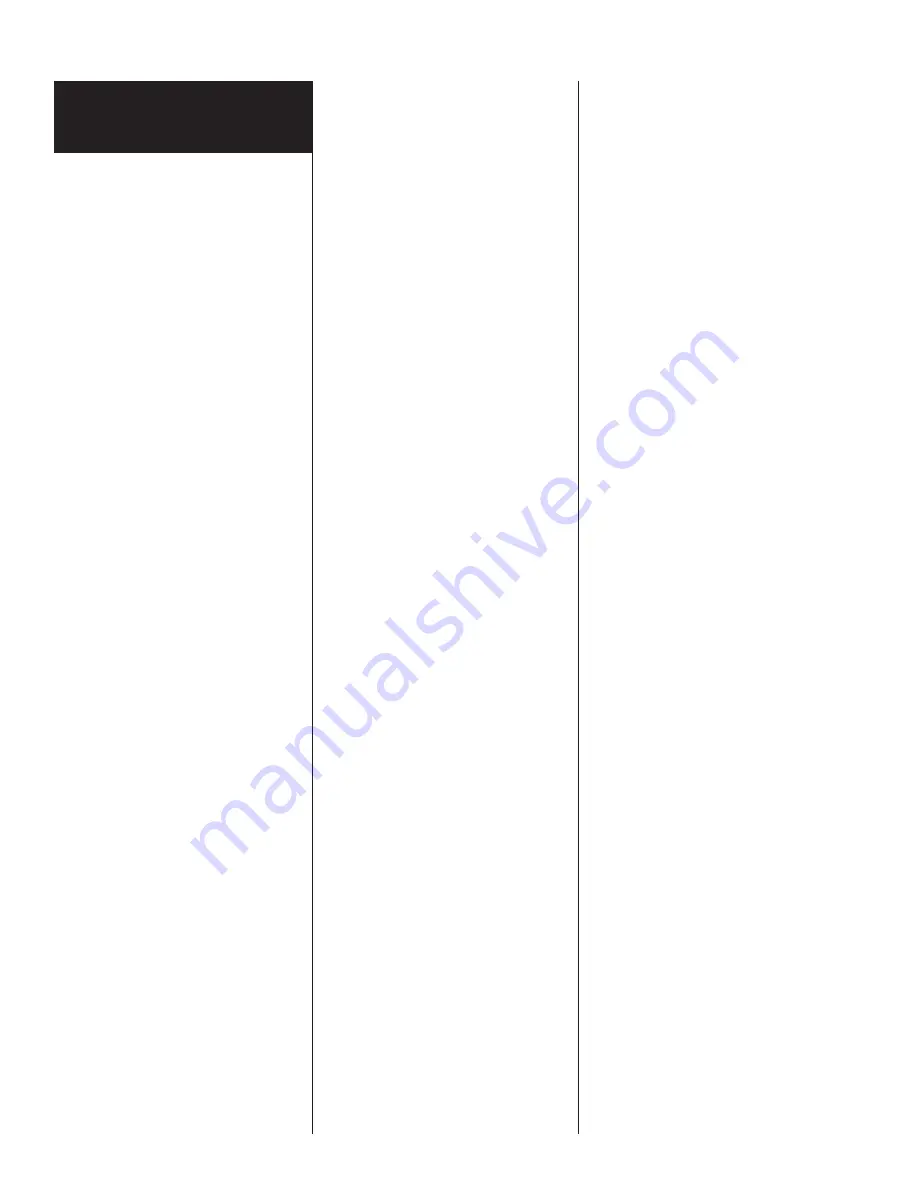
4
Pump
Servicing
Read the following instructions
carefully before replacing any
parts. Reasonable care and safe
methods should be practiced.
Check local codes and
requirements before installation.
Only competent electrician
should make the installations.
Before removing the pump from
its installation for repairs, check
first to see if the trouble is
caused by:
1. Miswiring of the pump into the
terminal block.
2. Miswiring of the flat level
controls into the panel.
3. Miswiring inside the control
panel.
4.
Tripped circuit breaker.
If the
breaker is manually reset and
then trips off again, the
problem could be:
a. short circuit in motor or
control panel
b. water in the motor housing
c. insufficient amp capacity of
wiring or breakers, or low
voltage supply
d. improper panel wiring
5.
Tripped overload.
If overload
is manually reset and then
trips off again, the problem
could be:
a. pump or piping clogged
b. pump motor or bearings may
be defective
c. start capacitor in motor may
have failed
d. pump may be miswired to
terminal block
e. head lower than rating,
pumping too much liquid
6.
Air locked pump.
Disconnect
piping at union and run until
all air bubbles are expelled.
Hydromatic pumps have a
small air vent hole in the
impeller cavity to let out
trapped air. If this hole
becomes plugged, pump may
air lock. To break the air
lock, use a small screwdriver
to clear hole in the
impeller cavity.
As a secondary precaution in
installations of this type, 1 ⁄ 16"
hole should be drilled in the
discharge pipe below the check
valve. The check valve should
be 12 to 18 inches above pump
discharge. Do not put check
valve directly into pump
discharge opening.
NOTE: In sumps where the
pump is operating daily, air
locking rarely occurs.
7.
Wrong impeller rotation.
The rotation should be
counterclockwise when you’re
looking at the impeller.
Correct improper rotation
on three phase pumps by
reversing any two line leads.
No rotation check is necesary
on single phase pumps.
8. Closed discharge gate valve.
9. Plugged impeller or pipeline.
10.Discharge head may be too
high. Check elevation against
design point of pump.
11.Floats not hanging free in
the sump.
12.Malfunctioning floats.
WARNING: Be certain power
to pump is off! Disconnect
the pump power cord from
terminals and remove pump
from sump.
1. Clean any dirt or trash from
the outside of the pump
before dismantling.
2. Check for an obstruction in the
impeller by looking through
the suction hole of the pump.
The shaft should turn freely if
unobstructed. Keep fingers,
clothing or any material from
suction inlet. Serious injury
may occur if pump is
connected to power source.
3. Obtain an ohmmeter to test for
burned or broken wires or for
defective stator winding. Set
ohmmeter scale pointer to
R X 1 scale and check the
meter by putting both meter
leads together and adjusting
the needle knob until the meter
reads zero. If the meter cannot
be adjusted to zero, the
batteries need to be replaced.
For three phase pumps, attach
one meter lead to the white
cord wire of the power cord
and the outer meter lead to the
black cord wire. This reading
should equal the resistance
of one phase (see Winding
Resistance Chart). Repeat the
above procedure for white and
red wires as well as red and
black wires. Each of the three
separate readings should read
approximately the same. If no
resistance is obtainable for any
of the three phases, either a
wire is broken, there is a bad
connection or the winding is
defective. Skip Steps 5 and 8
if resistance is OK.
For single phase pumps, remove
the hex head cap screws (11)
from adaptor ring casing (10)
and remove assembly from
volute (14). Disassemble wire
connections from motor (7)
and remove power cord (27)
from pump. Using the wire
leads (26) from the motor (7)
check the winding resistance
with an ohmmeter.