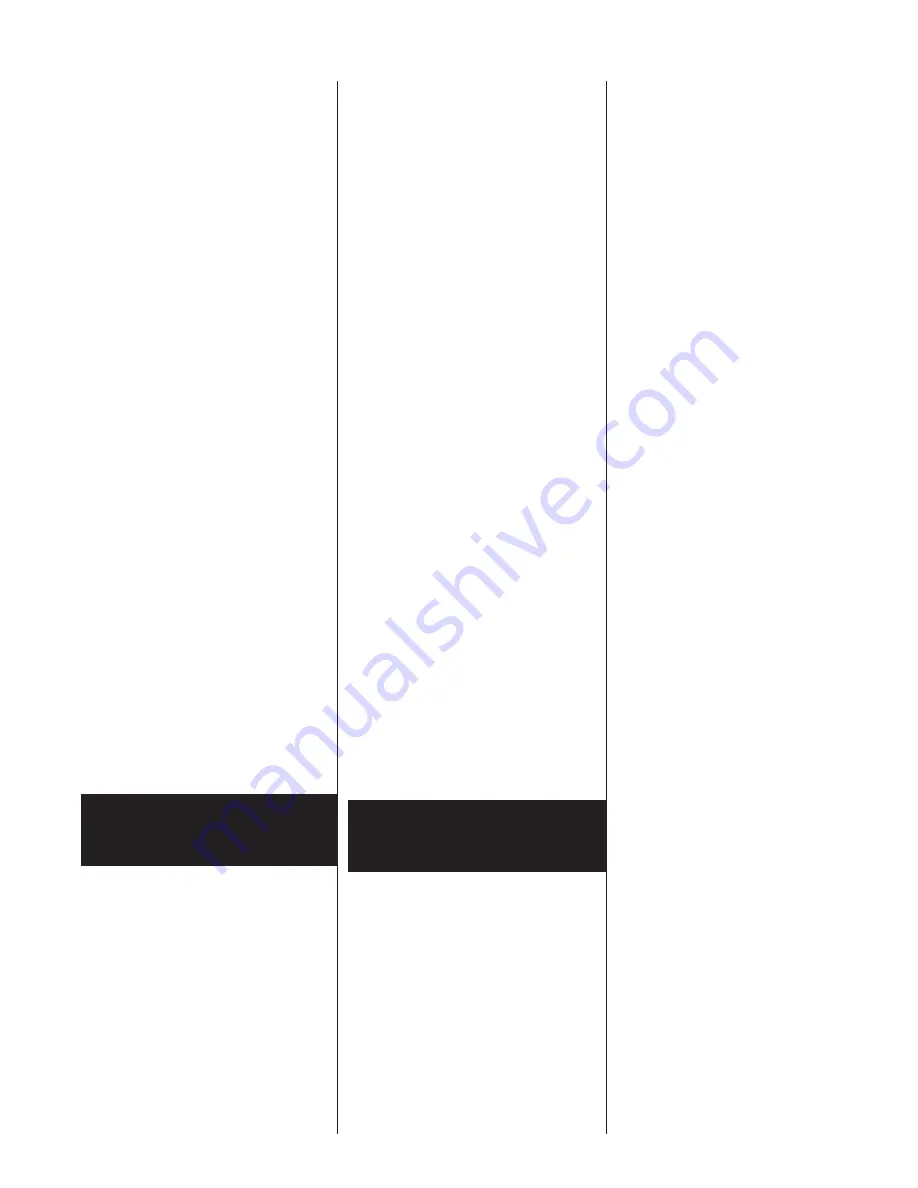
3
A check valve must be installed
on each pump.
Location:
If pumps are installed in an
existing basin or concrete sump,
the piping can either be connected
permanently or rails and brackets
can be furnished for mounting to
walls of basin. In either case, be
sure that the Hydromatic nonclog
check valve is used and that the
pumps are submerged in a
vertical position. The complete
factory-built packaged system is
recommended for the most
satisfactory installation and
generally for the lowest cost
where expensive installation labor
is involved.
Making Electrical Connections:
All electrical wiring must be in
accordance with local code, and
only qualified electricians should
make the installations. Complete
wiring diagrams are included for
use in making the installation. All
wires should be checked for shorts
to ground with an ohmmeter or
Megger after the connections are
made. This is important, as one
grounded wire can cause
considerable trouble.
1. Grinder pump is single phase;
no rotation check is necessary.
2. Run water into sump until
motor is covered.
3. Open gate valve in discharge
line.
4. Turn pump on. If pump runs
and sump liquid does not pump
down, stop pump and close
discharge gate valve. Then lift
pump until sealing flange is open
to vent off trapped air. Lower
pump, open discharge valve,
and start the pump again.
5. Level control should be set so
that pump turns off when level
is about 2 inches above inlet
of pump suction and turns on
when level is about 2 inches
above motor.
6. If problems occur check power
source. Make sure a separate
supply line is available. Verify
voltage supply.
7. Check resistance of windings.
(See Chart, page 5.) If not
within guidelines, return pump
to authorized Hydromatic
service or repair center.
As the motors are oil filled, no
lubrication or other maintenance
is required. Pump should be
checked every quarter for
corrosion and wear.
Starting the Pump:
WARNING: Severe injury may
result from accidental contact
with moving cutters. Keep
clothing, hands and feet away
from cutters any time power is
connected to the pump.
To start the pump, perform the
following steps in order:
Pump
Servicing
connected and that the unit
is properly grounded in
accordance with local codes.
CAUTION: Severe injury may
result from accidental contact
with moving cutters. Keep
clothing, hands and feet away
from cutters any time power is
connected to the pump.
Replacing Grinder Parts:
If necessary to replace grinder
parts because of wear or to inspect
for clogging:
1. Close gate valve at pump
discharge.
2. Turn off circuit breaker.
CAUTION: Never work on
pump with power on. Be sure
ground wire from pump is
connected to a good ground
such as a water pipe.
3. Remove pump from sump.
4. Unscrew screws (17) and
remove cutter ring retainer
(16). Stationary cutter (15)
cannot be removed from volute
(20).
5. Unscrew hex head cap screws
(12) and remove volute
case (20).
6. Radial cutter (13) and axial
cutter (14) are now exposed. If
checking for clogging, these
parts can now be cleaned
without removing them from
the shaft.
7. If necessary to replace
cutters, remove screw (19),
washer (18), and radial cutter
(13) from shaft. Radial cutter
(13) and impeller (9) are
screwed onto shaft. The thread
is right-hand. Tap radial cutter
(13) with plastic hammer if
necessary to loosen. Axial
Pump
Operation
Read the following instructions
carefully before replacing any
parts. Reasonable care and safe
methods should be practiced.
Check local codes and
requirements before installation.
Only a competent electrician
should make the installations.
CAUTION: Never work on
pump with power on. Make sure
that the ground wire is securely