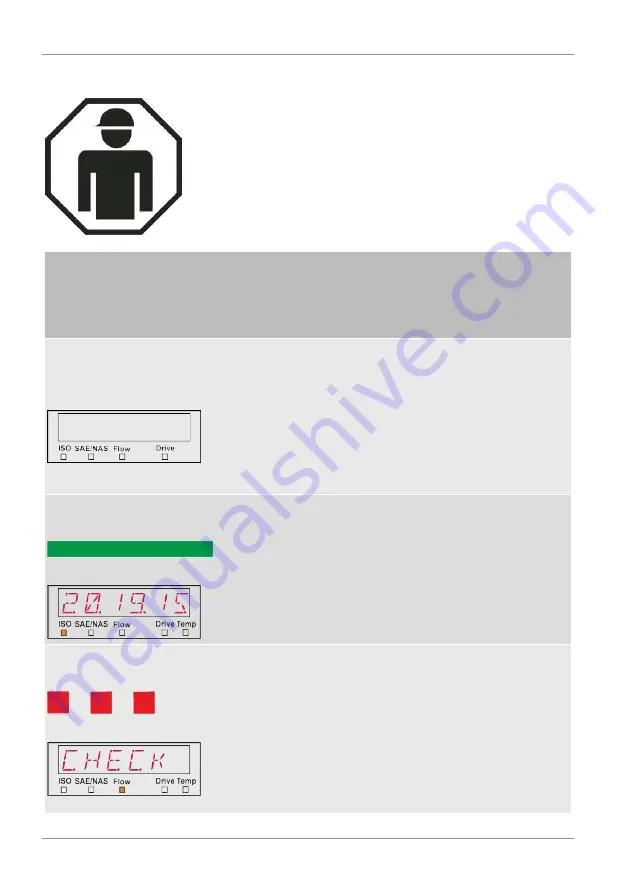
10 | Finding / rectifying errors
HYDAC FILTER SYSTEMS GMBH
76 / 92
BeWa FCU1210 3545830b en-us lq
10 Finding / rectifying errors
The following malfunctions / errors can occur during operation.
Disruption / error
LED
Status-LED
Display
Status /
Possible causes
Solution
LED: Off
Status LED:
Display:
Error code: -
No display
No function
Check the power supply to the
FCU.
Contact the HYDAC Service
Department.
LED: Green
Status LED
Display: (Example)
The FCU is ready for oper-
ation.
You can take measurements.
LED: Red
Status LED:
Display:
The flow rate is too low.
Check that the flow is between
30 … 500 ml/min, as permit-
ted.
Check whether the pump is
running and whether the IN-
LET connection is attached
Check/lean the suction
strainer.