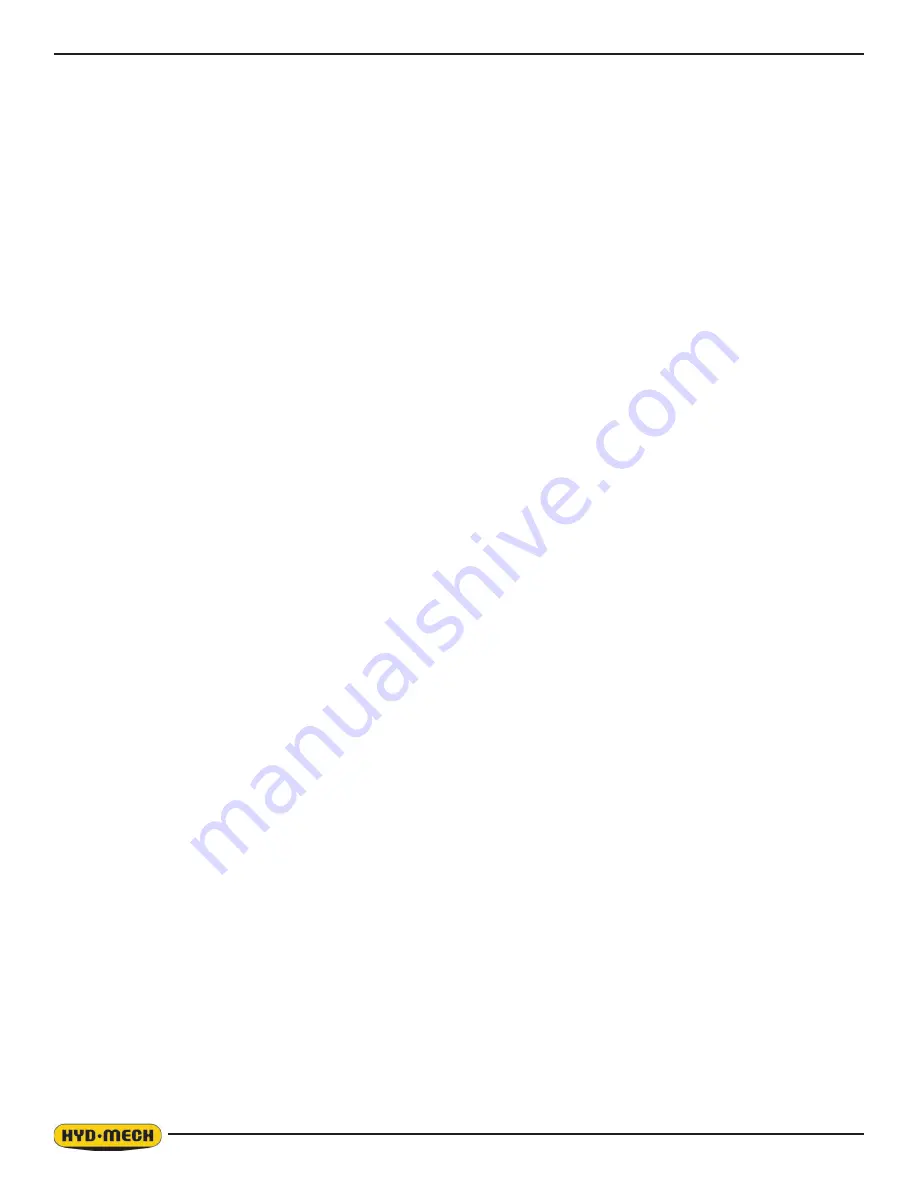
3.12
3.13
•
load machine with a piece of stock for test cutting
•
program the PLC to cut two pieces each of 1”, 12” and a length equal to a shuttle and a half of the machine being
checked.
•
make the cuts and measure as a accurately as possible (vernier caliper)
•
using the formula provided below, calculate the new parameter “LTH CONST”
Formula for determining new parameter “LTH CONST”
Measured length divided by Programmed length X Existing constant = New “LTH CONST”
i.e. Programmed length
= 1.00” Measured length
= .999”
-0.001” short
= 12.00”
= 11.988”
-0.012” short
= 60.00”
= 59.940”
-0.060” short
Existing parameter “LTH CONST”
= 0.001256
11.988 divided by 12.00 x 0.001256
= 0.001255
The new parameter “LTH CONST” would be 0.001255. This value should be entered as the new “LTH CONST” parameter
and test cuts repeated. Adjust the parameter again if necessary.
GENERAL RULE:
Lowering the parameter value = longer shuttle travel = longer parts
Increasing the value = shorter shuttle travel = shorter parts
PROBLEM # 3, (for P models, disregard all references to a shuttle).
AUTO cycle not being completed
In the AUTO mode, the PLC controls saw functions through output relays. For a certain function to be actuated, the PLC
must first see specific input(s). Like the output relays, the input relays are located on the PLC unit. Directly beside input
and output terminals are red LED lights, which light up when the corresponding input is being received or output is being
actuated. Observation of these input/output LED’s can help to diagnose AUTO cycle problems. When a problem occurs in
the AUTO mode, the lights should be checked to see if they are coming on at the proper time or at all.
INPUT LED’s
•
If a specific input light does not come on when expected;
•
Check for a faulty/misadjusted limit switch, push button, encoder or by faulty wiring and connections.
•
Wiring for each limit switch should be connected from the VDC terminal connection to particular limit switch and
from the limit switch to the input connector of the PLC.
NOTE:
All inputs are denoted by “X”
All outputs are denoted by “Y”
Following is information on output diagnosis and the sequence of inputs and outputs during AUTO cycle.
AUTO CYCLE SEQUENCE:
After the mode push button is in the AUTO position and the job has been
Programmed into the PLC, and the Cycle Start push button pressed:
1. Hydraulics running, the head should move to its up limit, if it is not already there. Shuttle vise should open and come
forward to the home position. HUP input light must come on for cycle to continue.
HUP input on - cycle should continue, if not check outputs per step 2.
HUP input not on - check that head up limit switch is being actuated, check limit switch / limit switch wiring.
2. Front vise should be closed, the shuttle vise should stay open and move back to the programmed length;
FVC output should be on, SVO output will light momentarily, REV output and FST output should be on when the
Summary of Contents for H14A
Page 2: ......
Page 16: ......
Page 32: ......
Page 50: ......
Page 55: ...4 5 ...
Page 56: ...4 6 ELECTRICAL SCHEMATICS 208 240 VOLT ...
Page 57: ...4 7 ...
Page 58: ...4 8 ...
Page 59: ...4 9 ...
Page 60: ...4 10 ...
Page 61: ...4 11 ...
Page 62: ...4 12 ...
Page 63: ...4 13 ...
Page 64: ...4 14 ...
Page 65: ...4 15 ...
Page 66: ...4 16 ...
Page 67: ...4 17 ...
Page 68: ...4 18 ELECTRICAL SCHEMATICS 480 575 VOLT ...
Page 69: ...4 19 ...
Page 70: ...4 20 ...
Page 71: ...4 21 ...
Page 72: ...4 22 ...
Page 73: ...4 23 ...
Page 74: ...4 24 ...
Page 75: ...4 25 ...
Page 76: ...4 26 ...
Page 77: ...4 27 ...
Page 78: ...4 28 ...
Page 79: ...4 29 ...
Page 80: ...4 30 ...
Page 82: ...5 2 GLAND ASSEMBLIES PISTON ASSEMBLIES ...
Page 83: ...5 3 HYDRAULIC SCHEMATIC ...
Page 84: ...5 4 HYDRAULIC PLUMBING DIAGRAM ...
Page 85: ...5 5 ...
Page 86: ...5 6 ...
Page 87: ...5 7 ...
Page 88: ......
Page 96: ...6 8 FRONT VISE ASSEMBLY ...
Page 101: ...6 13 ...
Page 102: ...6 14 BONFIGLIOLI A412 GEARBOX ASSEMBLY ...
Page 103: ...6 15 ...
Page 105: ......
Page 106: ......
Page 107: ......
Page 108: ......
Page 112: ......
Page 114: ...8 2 H 14A LAYOUT DRAWING ...