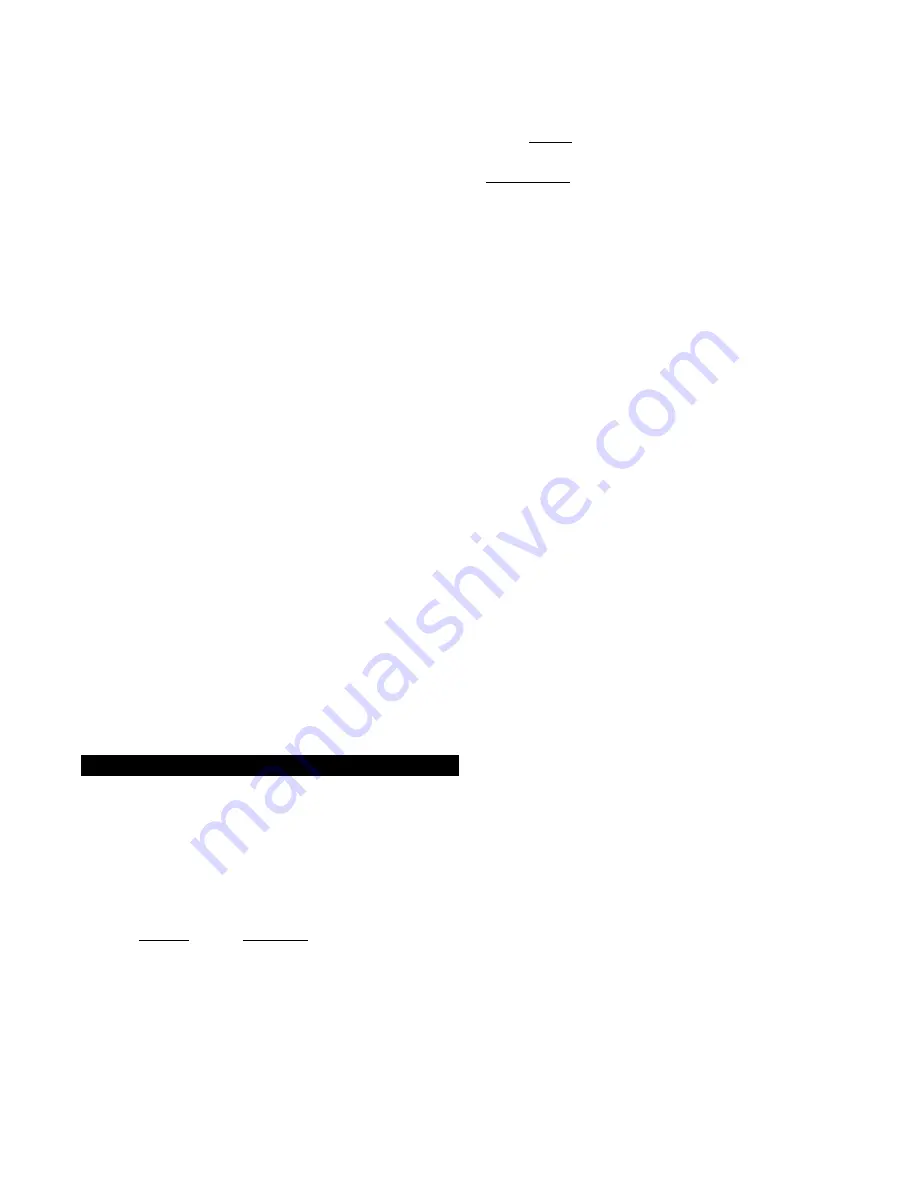
Rev.0109
5
condensate drains to insure a proper installation:
1. Never use pipe for condensate drains smaller than
the nominal diameter of the pipe or P-trap supplied
with the case.
2. When connecting condensate drains, the P-trap
must be used as part of the condensate drain to
prevent air leakage or insect entrance. Store plumb-
ing system floor drains should be at least 14" off the
center of the case to allow use of the P-trap pipe
section. Never use two water seals in series in any
one line. Double P-traps in series will cause a lock
and prevent draining.
3. Always provide as much down hill slope (“fall”) as
possible; 1/8" per foot is the preferred minimum.
PVC pipe, when used, must be supported to main-
tain the 1/8" pitch and to prevent warping.
4. Avoid long runs of condensate drains. Long runs
make it impossible to provide the “fall” necessary for
good drainage.
5. Provide a suitable air break between the flood rim of
the floor drain and outlet of condensate drain. 1" is
ideal.
6. Prevent condensate drains from freezing:
a. Do not install condensate drains in contact with
non-insulated suction lines. Suction lines should be
insulated with a nonabsorbent insulation material
such as Armstrong’s Armaflex.
b. Where condensate drains are located in dead air
spaces (between refrigerators or between a
refrigerator and a wall), provide means to prevent
freezing. The water seal should be insulated to
prevent condensation.
Refrigeration
REFRIGERANT TYPE
The standard refrigerant will be R-22 unless otherwise
specified on the customer order. Check the serial plate
on the case for information. Minimum opening for self
contained condensor units - 150 sq. in. up to 1 1/2 hp, 200
for over 1 1/2 hp.
REFRIGERATION LINES
LIQUID
SUCTION
3/8" O.D.
5/8" O.D.
NOTE: The standard coil is piped at 5/8" (suction); however,
the store tie-in may vary depending on the number of
coils and the draw the case has. Depending on the case
setup, the connecting point in the store may be
5
/
8
",
7
/
8
", or 1
1
/
8
". Refer to the particular case you are
hooking up.
Refrigerant lines should be sized as shown on the refrig-
eration legend furnished by the store.
Install
P-traps
(oil traps) at the base of all suction line ver-
tical risers.
Pressure drop
can rob the system of capacity. To keep the
pressure drop to a minimum, keep refrigerant line run as
short as possible, using the minimum number of elbows.
Where elbows are required, use long radius elbows only.
CONTROL SETTINGS
See the “Case Specs” section of this guidebook for the
appropriate settings for your merchandiser. Maintain these
parameters to achieve near constant product tempera-
tures. Product temperature should be measured first thing
in the morning, after having been refrigerated overnight.
For all multiplexing, defrost should be time terminated.
Defrost times should be as seen in Case Specifications.
The number of defrosts per day should never change. The
duration of the defrost cycle may be adjusted to meet
conditions present at your location.
ACCESS TO TX VALVES & DRAIN LINES
Remove product from either side of the case.
The drain is behind the panel labeled “Drain Access”
TX Valves:
MECHANICAL
-Lift bottom deck pans to access the fan ple-
nums and TX valve.
ELECTRONIC
- The Electronic Expansion Valve is located
in the same place as the mechanical TXV. The control
module is located near the electrical stub-up area.
ELECTRONIC EXPANSION VALVE
(OPTIONAL)
A wide variety of electronic expansion valves and case
controllers can be utilized. Please refer to EEV and con-
troller manufacturers information sheet. Sensors for elec-
tronic expansion valves will be installed on the coil inlet,
coil outlet, and in the discharge air. (Some supermarkets
require a 4th sensor in the return air). Case controllers
will be located in the electrical raceway or under the case
THERMOSTATIC EXPANSION VALVE LOCATION
This device is located on the same side as the refrigera-
tion stub. An Alco balanced port expansion valve model is
furnished as standard equipment, unless otherwise speci-
fied by customer.
EXPANSION VALVE ADJUSTMENT
Expansion valves must be adjusted to fully feed the evapo-
rator. Before attempting any adjustments, make sure the
evaporator is either clear or very lightly covered with frost,
and that the fixture is within 10
°
F of its expected operat-
ing temperature.
MEASURING THE OPERATING SUPERHEAT
1. Determine the suction pressure with an accurate
pressure gauge at the evaporator outlet.
Summary of Contents for RMID
Page 36: ...IGIC RMID 0109 36 ...