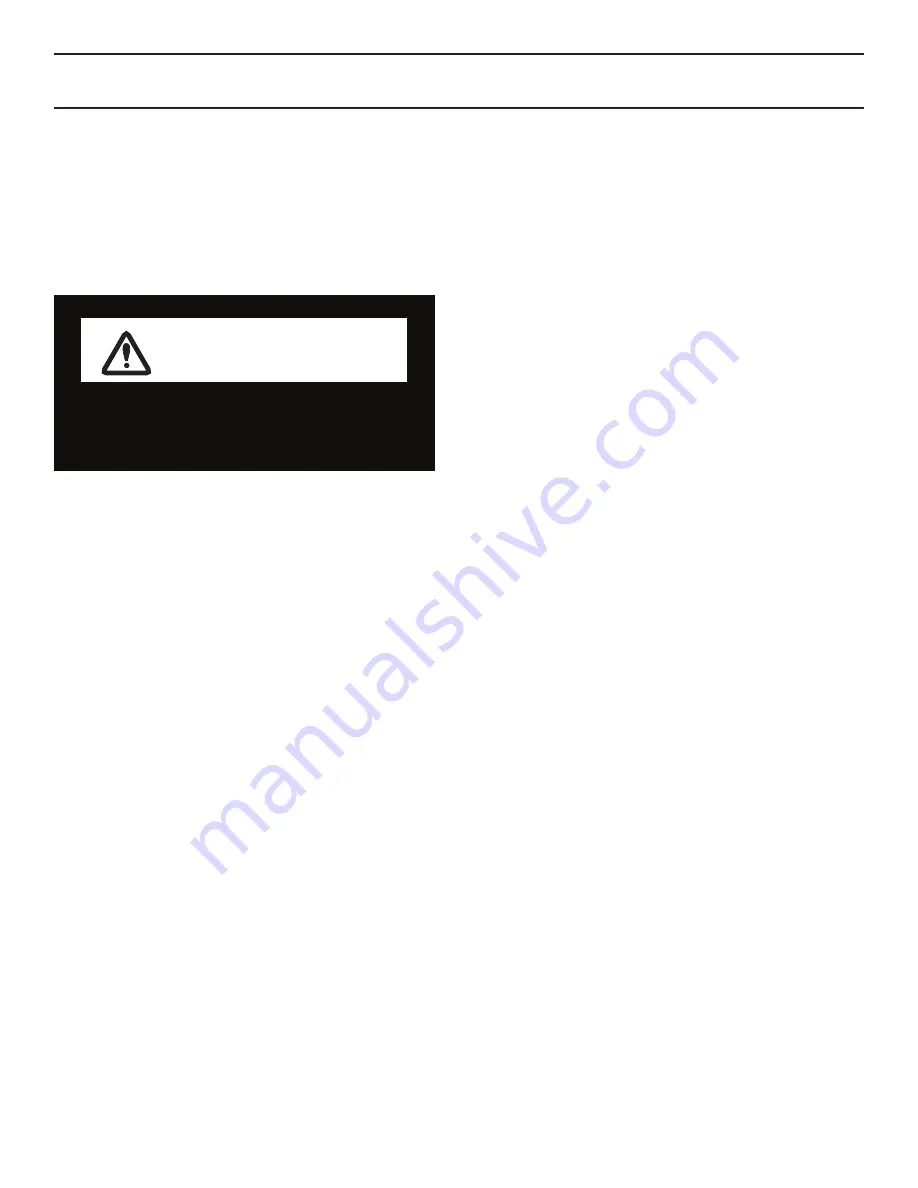
34
Case Cleaning
Long life and satisfactory performance of any
equipment are dependent upon the care it re-
ceives. To insure long life, proper sanitation and
minimum maintenance costs, the merchandiser
should be thoroughly cleaned, all debris re-
moved and interiors washed down, weekly.
WARNING
TO PREVENT INJURY ALWAYS SHUT OFF
POWER DURING CLEANING PROCESS.
Exterior Surfaces
The exterior surfaces must be cleaned with a
mild detergent and warm water to protect and
maintain their attractive finish. NEVER USE
ABRASIVE CLEANSERS OR SCOURING
PADS
.
Cleaning Bumpers
Clean Bumpers with household spray cleaners.
Cleaning Under Merchandiser
Remove lower body panels. Use a vacuum with
a long wand attachment to remove accumulated
dust and debris from under the merchandiser.
Cleaning Stainless Steel Surfaces
Use non abrasive cleaning materials, and always
polish with grain of steel. Use warm water or add
a mild detergent to the water and apply with a
cloth. Always wipe dry after wetting.
Use alkaline chlorinated or non-chlorine contain-
ing cleaners such as window cleaners and mild
detergents. Do not use cleaners containing salts
as this may cause pitting and rusting of the stain-
less steel finish. Do not use bleach.
Clean frequently to avoid build-up of hard, stub-
born stains. A stainless steel cleaning solution
may be used periodically to minimize scratching
and remove stains.
Rinse and wipe dry immediately after cleaning.
Never use hydrochloric acid (muriatic acid) on
stainless steel.
Interior Surfaces
The interior surfaces may be cleaned with most
domestic detergents, ammonia based clean-
ers and sanitizing solutions with no harm to the
surface.
Cleaning Coils
NEVER USE SHARP OBJECTS AROUND
COILS.
Use a soft brush or vacuum brush to
clean debris from coils. Do not puncture Coils!
Do not bend fins. Contact an authorized service
technician if a coil is punctured, cracked, or oth-
erwise damaged.
ICE in or on the coil indicates the refrigera-
tion and defrost cycle is not operating properly.
Contact an authorized Service Technician to
determine the cause of icing and to make proper
adjustments as necessary. To maintain product
integrity, if not done so already, move all product
to a cooler until the merchandiser has returned
to normal operating temperatures.
Do Not Use:
• Abrasive cleaners and scouring pads, as
these will mar the finish.
• A hose on lighted shelves or submerge
shelves in water.
• Solvent, oil or acidic based cleaners on any
interior surfaces.
• A hose on LED Lights or any other electrical
component.
User Information Cont’d