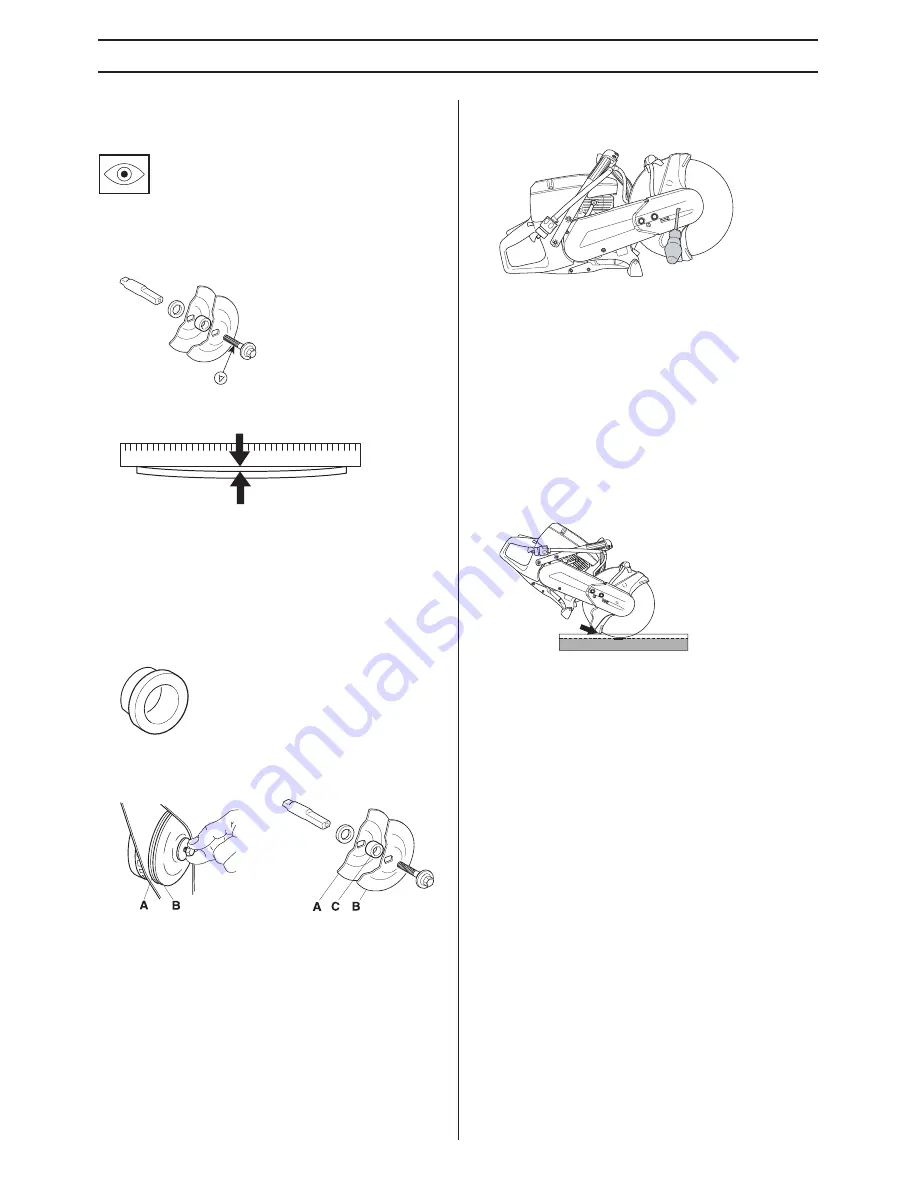
English
– 13
ASSEMBLY
Checking the drive axle and flange
washers
Check that the threads on the drive shaft are undamaged.
Check that the contact surfaces on the blade and the flange
washers are undamaged, of the correct dimension, clean,
and that they run properly on the drive axle.
Do not use warped, notched, indented or dirty flange
washers. Do not use different dimensions of flange washers.
Fitting the cutting blade
Husqvarna’s blades are approved for hand-held power
cutters. Blades are manufactured with three different
diameters of centre holes: 20 mm (0.787"), 22.2 mm (7/8")
and 25.4 mm (1"). Bushings can be fitted on the machine axle
to adjust the machine to the centre hole of the blade. Use a
bushing with the correct diameter! The blades are marked
with the diameter of the centre hole.
The blade is placed on the bushing (C) between the inner
flange washer (A) and the flange washer (B). The flange
washer is turned so that it fits on the axle.
Tightening torque for the bolt holding the blade is: 15-25 Nm
(130-215 in.lb).
The shaft can be locked using a screwdriver, steel pin or the
like. This is slid in as far as possible. The blade is tightened
clockwise.
When a diamond blade is mounted on the power cutter make
sure that the diamond blade will rotate in the direction
indicated by the arrow on the blade.
When the blade is replaced with a new one, check the flange
washers and the drive axle. See instructions under the
heading Checking the drive axle and flange washers.
Guard for the blade
The guard must always be fitted on the machine. The guard
for the cutting equipment should be adjusted so that the rear
section is flush with the work piece. Spatter and sparks from
the material being cut are then collected up by the guard and
led away from the user.
Summary of Contents for K 750 SpeedMill
Page 23: ......