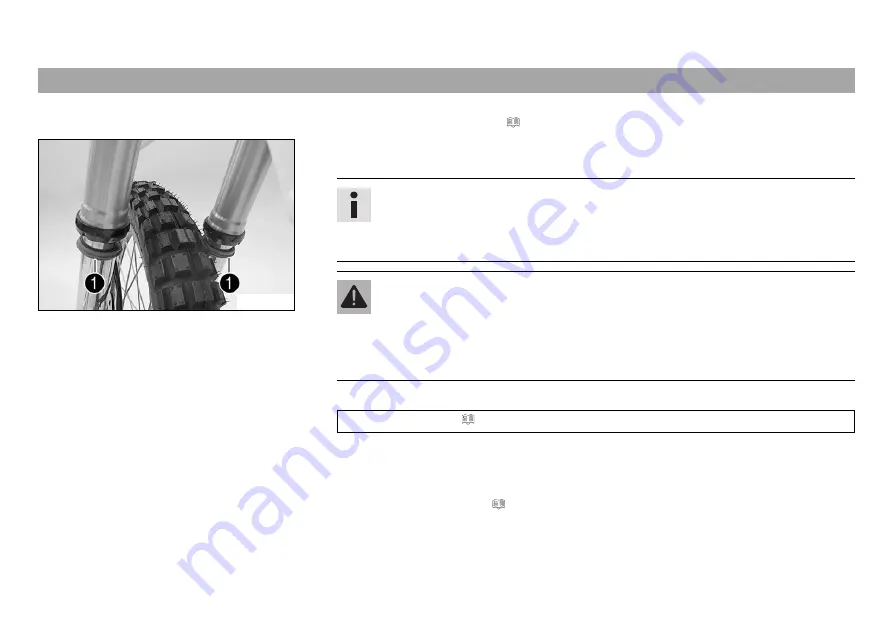
12 SERVICE WORK ON THE CHASSIS
79
12.4
Cleaning the dust boots of the fork legs
Preparatory work
–
Remove the fork protector. (
E00069-10
Main work
–
Push dust boots
of both fork legs downward.
Info
The dust boots remove dust and coarse dirt particles from the inside fork
tubes. Over time, dirt can accumulate behind the dust boots. If this dirt is not
removed, the oil seals behind can start to leak.
Warning
Danger of accidents
Oil or grease on the brake discs reduces the braking
effect.
–
Always keep the brake discs free of oil and grease.
–
Clean the brake discs with brake cleaner when necessary.
–
Clean and oil the dust boots and inner fork tubes of both fork legs.
Universal oil spray (
–
Press the dust boots back into their installation position.
–
Remove excess oil.
Finishing work
–
Install the fork protector. (