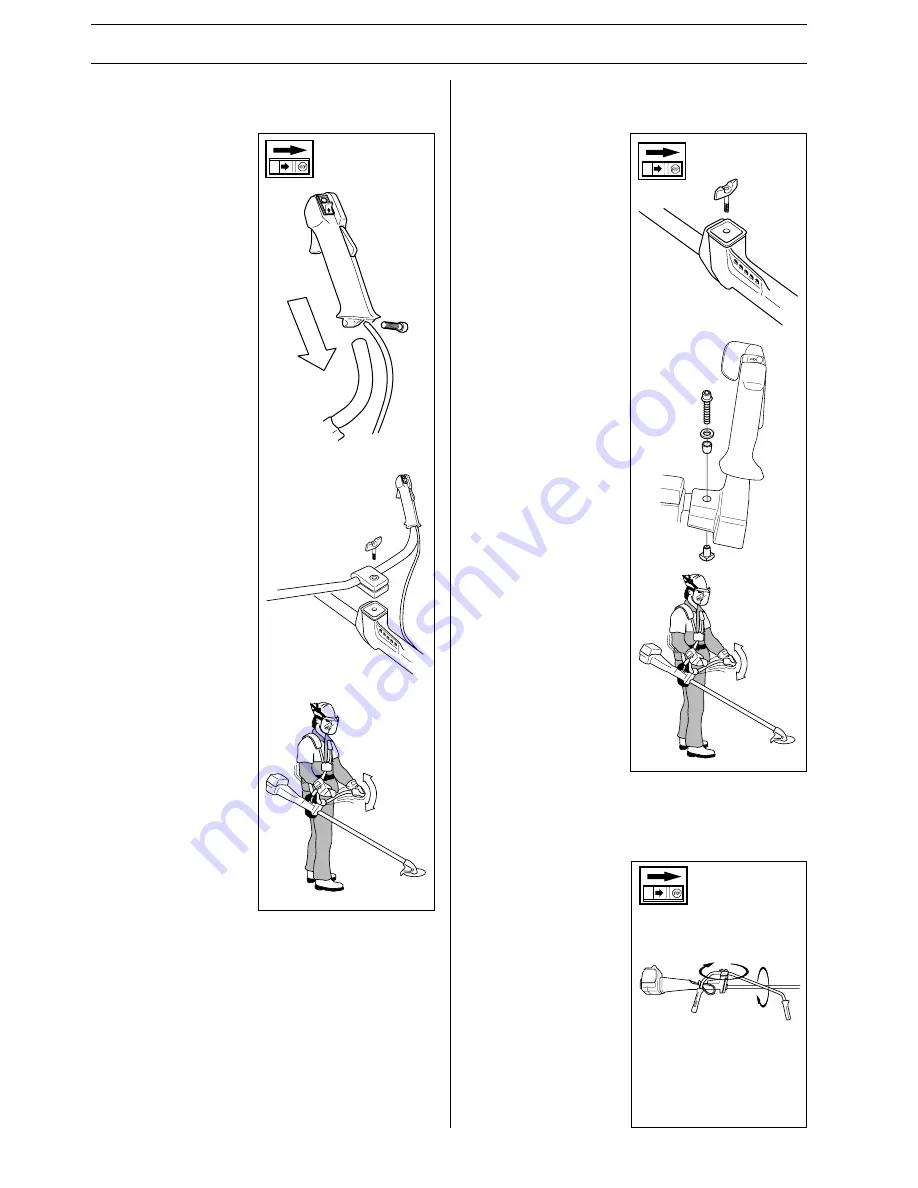
22
– English
Assembling the handlebars (240R,
245R, 250R)
ASSEMBLY
• The handlebars can easily
be turned to fit along the
shaft for easy
transportation and storage.
• Loosen the knob. Turn the
handles clockwise so that
the throttle comes against
the engine.
• Thereafter fold the
handlebars around the
shaft. Tighten the handle.
• Attach the transport guard.
• Unscrew the handle from
the handlebar bracket.
• Position the handlebars as
shown. Fit the bracket
components and tighten
the handle lightly.
• Fit the right hand grip to
the handlebar using the
bolt, washer, sleeve and
nut as shown. Tighten the
bolt.
• Put on the harness and
hang the machine in the
suspension hook. Now
finely adjust so that the
machine gives a
comfortable working
position when it‘s attached
to the harness. Tighten the
handle.
• Remove the screw at the
rear of the throttle handle.
• Slide on the throttle
handle on the right-hand
side of the handlebars, (see
the diagram).
• Align the hole in the
throttle handle for the
fixing screw with the hole
on the handlebars.
• Refit the screw in the rear
of the throttle handle.
• Fit the screw through the
throttle handle and the
handlebars and tighten.
• Unscrew the handle from
the handlebar bracket.
• Position the handlebars as
shown. Fit the bracket
components and tighten
the handle lightly.
• Put on the harness and
hang the machine in the
suspension hook. Now
finely adjust so that the
machine gives a
comfortable working
position when it‘s attached
to the harness. Tighten the
handle.
Assembling the handlebars (245RX,
252RX)
Transport position, handlebars
(240R, 245R/RX, 250R, 252RX)
Summary of Contents for 240R
Page 40: ...40 English 1 Tri Cut 2 3 4 5 6 7 8 20mm 20mm B A 6 Nm X 10 ...
Page 48: ...48 English ...
Page 49: ...English 49 ...
Page 50: ...50 English H o 5 ...
Page 51: ...English 51 ...
Page 52: ...2001W34 H o 5 114 00 27 95 ...