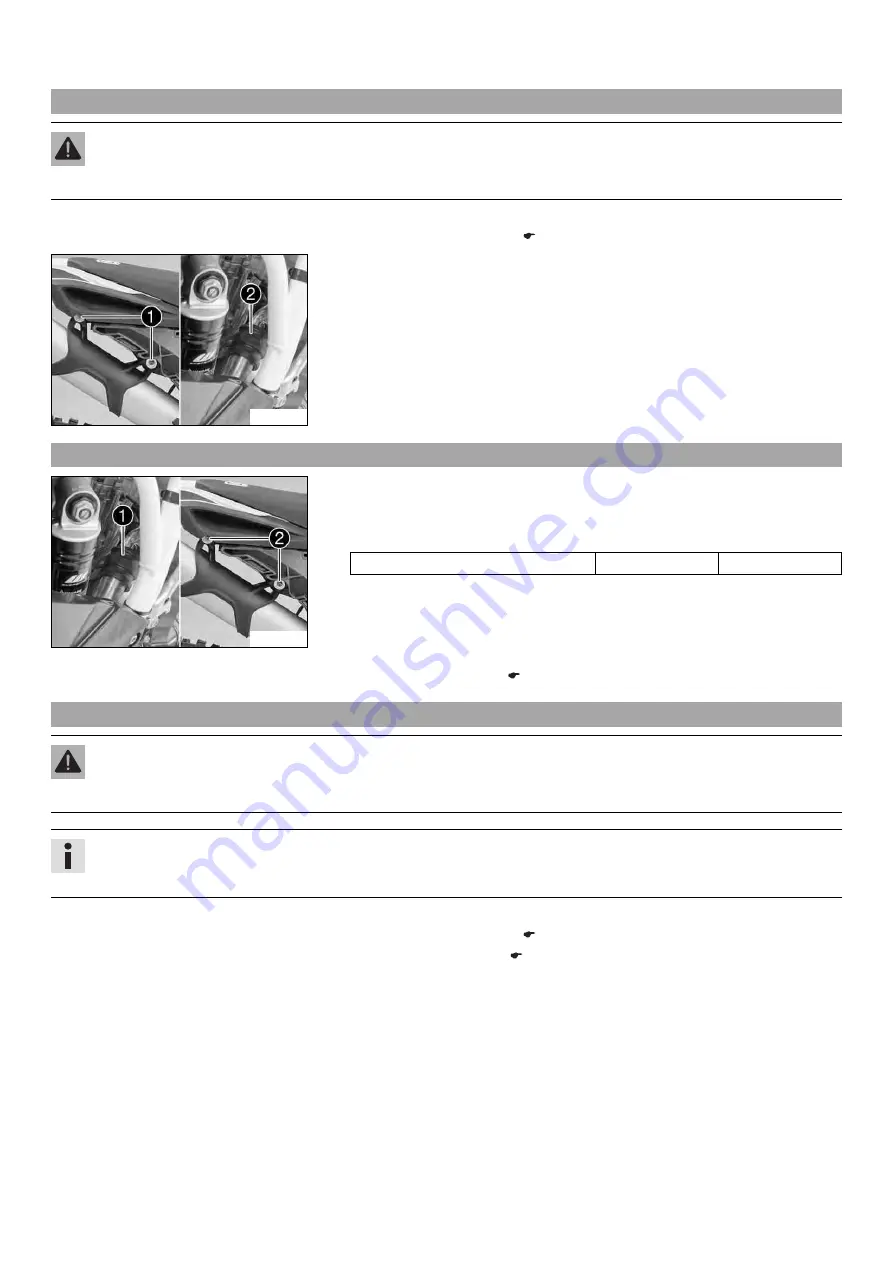
12 SERVICE WORK ON THE CHASSIS
54
12.28
Removing the main silencer
Warning
Danger of burns
The exhaust system gets very hot when the vehicle is driven.
–
Allow the exhaust system to cool down. Do not touch hot components.
Preparatory work
–
Remove the right side cover. (
L01633-10
Main work
–
Remove screws
1
.
–
Pull the main silencer off of the manifold at rubber sleeve
2
.
12.29
Installing the main silencer
L01634-10
Main work
–
Mount the main silencer with rubber sleeve
1
.
–
Mount and tighten screws
2
.
Guideline
Remaining screws, chassis
M6
10 Nm (7.4 lbf ft)
Finishing work
–
Install the right side cover. (
12.30
Changing the glass fiber yarn filling of the main silencer
x
Warning
Danger of burns
The exhaust system gets very hot when the vehicle is driven.
–
Allow the exhaust system to cool down. Do not touch hot components.
Info
Over time, the fibers of the glass fiber yarn filling escape and the damper "burns" out.
Not only is the noise level higher, the performance characteristic changes.
Preparatory work
–
Remove the right side cover. (
–
Remove the main silencer. (
Summary of Contents for 2014 TE 125 EU
Page 2: ......