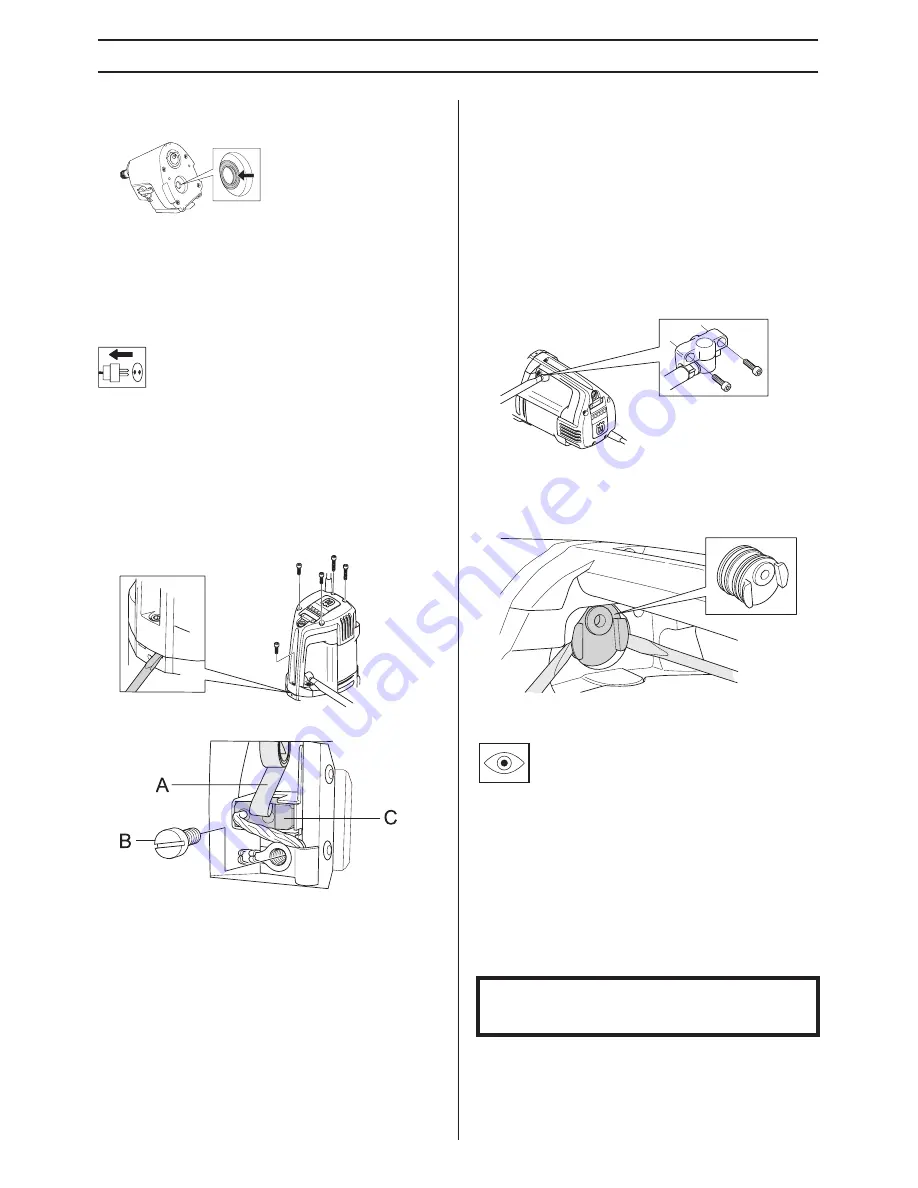
12 –
English
MAINTENANCE
6
If necessary contact your dealer to clean the gearbox.
7
Pour the new oil into the gearbox, about 0.5 litres.
8
Check that the sealing lip on the radial seal is intact.
9
Reassemble the machine and screw in the four screws.
Be careful when assembling so as not to damage the
radial seal.
Replacing the carbon brushes
The carbon brushes must be removed and checked regularly.
Weekly if the machine is used daily or at longer intervals if the
machine is used more seldom. The area of wear should be
even and undamaged.
Both carbon brushes must always be replaced as a pair, but
one at a time. Do as follows:
1
Remove the 5 screws from the inspection cover. Use a
chisel in the break tracks to easier remove the inspection
cover.
2
Lift the carbon brush holder spring to one side (A).
3
Loosen the screw (B).
4
Pull out the carbon brush connector.
5
Pull the carbon brush out from the holder (C).
6
Clean the brush holder with compressed air or a brush.
Replace the brush if worn.
7
Fit the new carbon brush. Make sure that the side with the
copper wire is facing the gear box and that the carbon
brush slides easily in the brush retainer. If the carbon
brush is fitted in the wrong direction it can get jammed.
8
Put the brush holder spring back into place.
9
Insert the carbon brush connection under the screw.
10 Repeat the procedure with the other carbon brush.
11 Guide the inspection cover into the handle's tracks. Begin
with the screw at the very bottom of the handle and
unscrew the inspection cover's five screws.
12 Let the machine idle for 10 minutes to run in the new
carbon brushes.
Replacing the seal retainer
If there is oil or water coming out of the leakage hole the seal
retainer must be replaced.
1
Loosen the two screws for the water module.
2
Use two flathead screwdrivers to carefully prize open the
seal retainer.
3
Carefully push in the new seal retainer and screw the
water module back on.
Daily maintenance
1
Check that nuts and screws are tight.
2
Check that the power switch unit works smoothly.
3
Clean the outside of the machine.
4
Check and clean the cooling air openings.
5
Check that the cord and extension cord are intact and in
good condition.
Repairs
Important All types of repairs may only be carried out by
authorised repairmen. This is so that the operators are not
exposed to great risks.
Summary of Contents for 1152417-30
Page 15: ...English 15 WIRING DIAGRAM ...