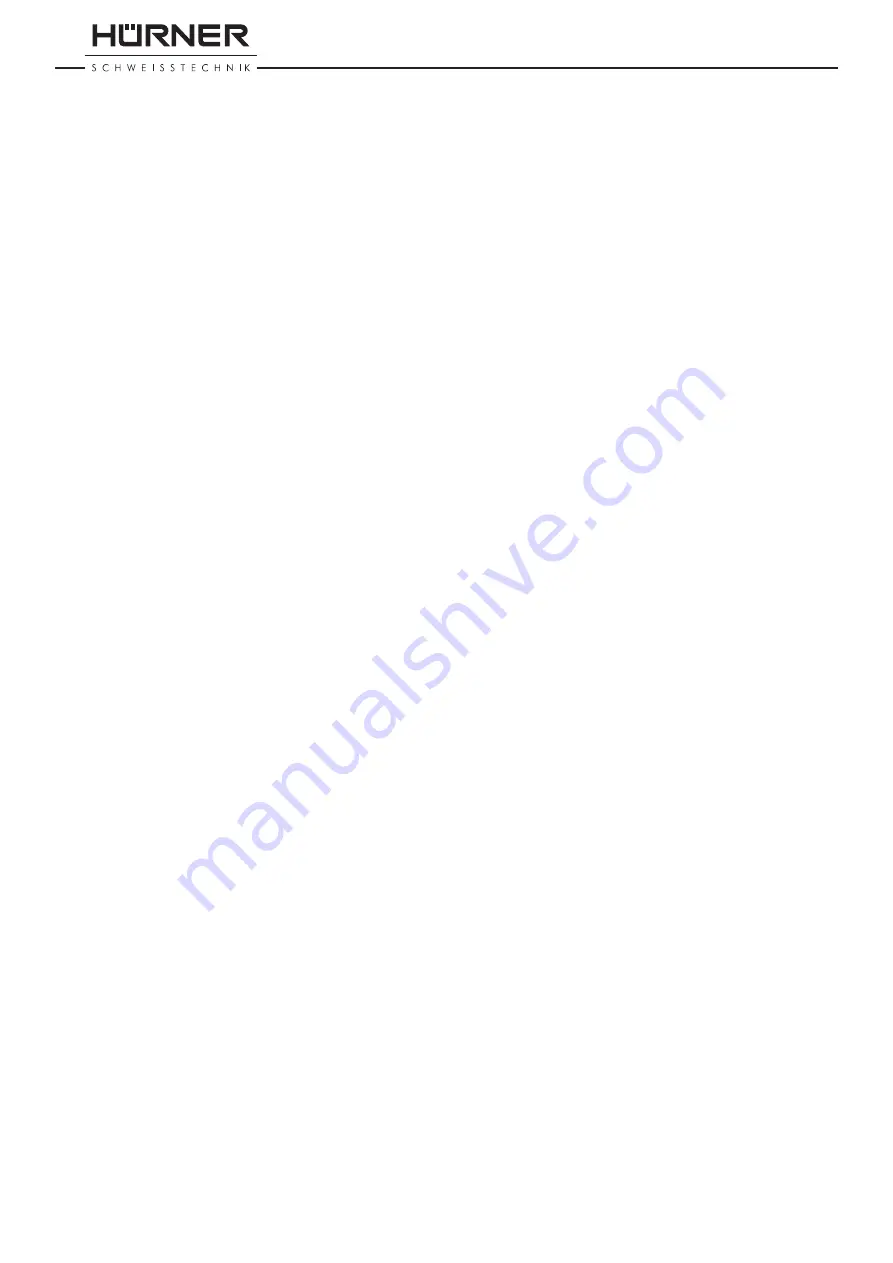
Version April 2016
8
EN
HÜRNER HST 300 2.0 User’s Manual
H Ü R N E R S c h w e i s s t e c h n i k G m b H
Nieder-Ohmener Str. 26
35325 Mücke, Germany
3
Service and Repair
3.1 General
As the product is used in applications that are sensitive to
safety considerations, it may be serviced and repaired only
by the manufacturer or its duly authorized and trained
partners. Thus, constantly high standards of operation
quality and safety are maintained.
Failure to comply with this provision will dispense the
manufacturer from any warranty and liability claims for
the product, including any consequential damage.
When serviced, the unit is upgraded automatically to the
technical specifications of the product at the moment it is
serviced, and we grant a three-month functional warranty
on the serviced unit.
We recommend having the product serviced at least every
twelve months.
Any provisions in the law pertaining to an electrical safety
inspection have to be complied with.
3.2 Transport, Storage, Shipment
The product ships in a transport box. The product should
be stored in this box, protects the product from humidity
and environmental agents.
When sending the product, it should be placed into the
transport box at all times.
Any provisions in the law pertaining to an electrical safety
inspection have to be complied with.
4
Principles of Operation
The HST 300 2.0 and the HST 300 Junior 2.0 allow
welding electrofusion fittings that feature a bar code.
Every fitting is provided with a tag with one or two bar
codes on it. The structure of this code is internationally
standardized. The first code, encoding the data on proper
welding, complies with ISO TR 13950 and can be processed
with the welding unit.
The model version HST 300 2.0 allows addition-
ally the manual input of the welding parameters. The
microprocessor-controlled welding unit:-
• controls and monitors the welding process in a fully
automated fashion,
Summary of Contents for HST 300 Junior + 2.0
Page 2: ......