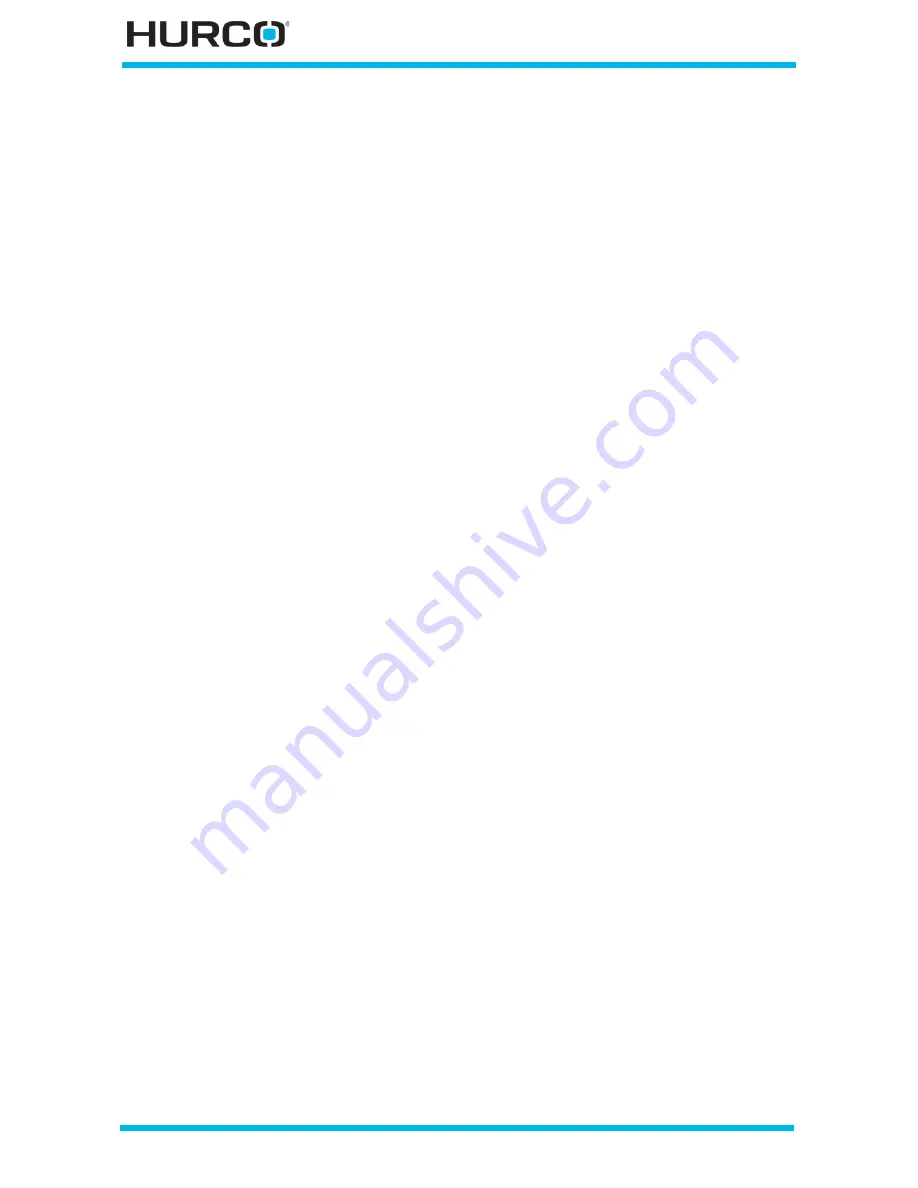
4 - 54 ISNC G Codes
704-0115-307
WinMax Lathe NC Programming
G73 - Pattern Repeating
G73 cuts identical profiles in each pass, shifting by the current relief amount as each pass
gets closer to the final profile.
Modal—No
F, S, and T functions specified in Profile blocks using G71 - Stock Removal in Turning, G72
- Stock Removal in Facing, and G73 - Pattern Repeating are ignored until a G70 is active.
G73 allows Linear and Circular interpolation.
Format
G73 U ____ W ____ R ____
G73 P ____ Q ____ U ____ W ____ F ____ S ____ T ____
Parameters
•
U—depth of cut in X axis
•
W—first line with W is depth of cut in Z axis
•
R—number of repetitions for roughing passes
•
P—first sequence number of Profile
•
Q—last sequence number of Profile
•
U—second line with U is finish allowance in X/2
•
W—second line with W is finish allowance in Z
•
F—cutting feedrate for roughing
•
S—spindle speed
•
T—tool with offset xxxx
Summary of Contents for winmax
Page 14: ...xiv List of Tables 704 0115 307 WinMax Lathe NC Programming...
Page 20: ...xx Programming and Operation Information 704 0115 307 WinMax Lathe NC Programming...
Page 98: ...2 50 Basic NC G Codes 704 0115 307 WinMax Lathe NC Programming...
Page 208: ...4 94 ISNC G Codes 704 0115 307 WinMax Lathe NC Programming...
Page 236: ...5 28 ISNC M Codes 704 0115 307 WinMax Lathe NC Programming...
Page 238: ...6 2 E Codes 704 0115 307 WinMax Lathe NC Programming...
Page 254: ...12 Index 704 0115 307 WinMax Lathe NC Programming...