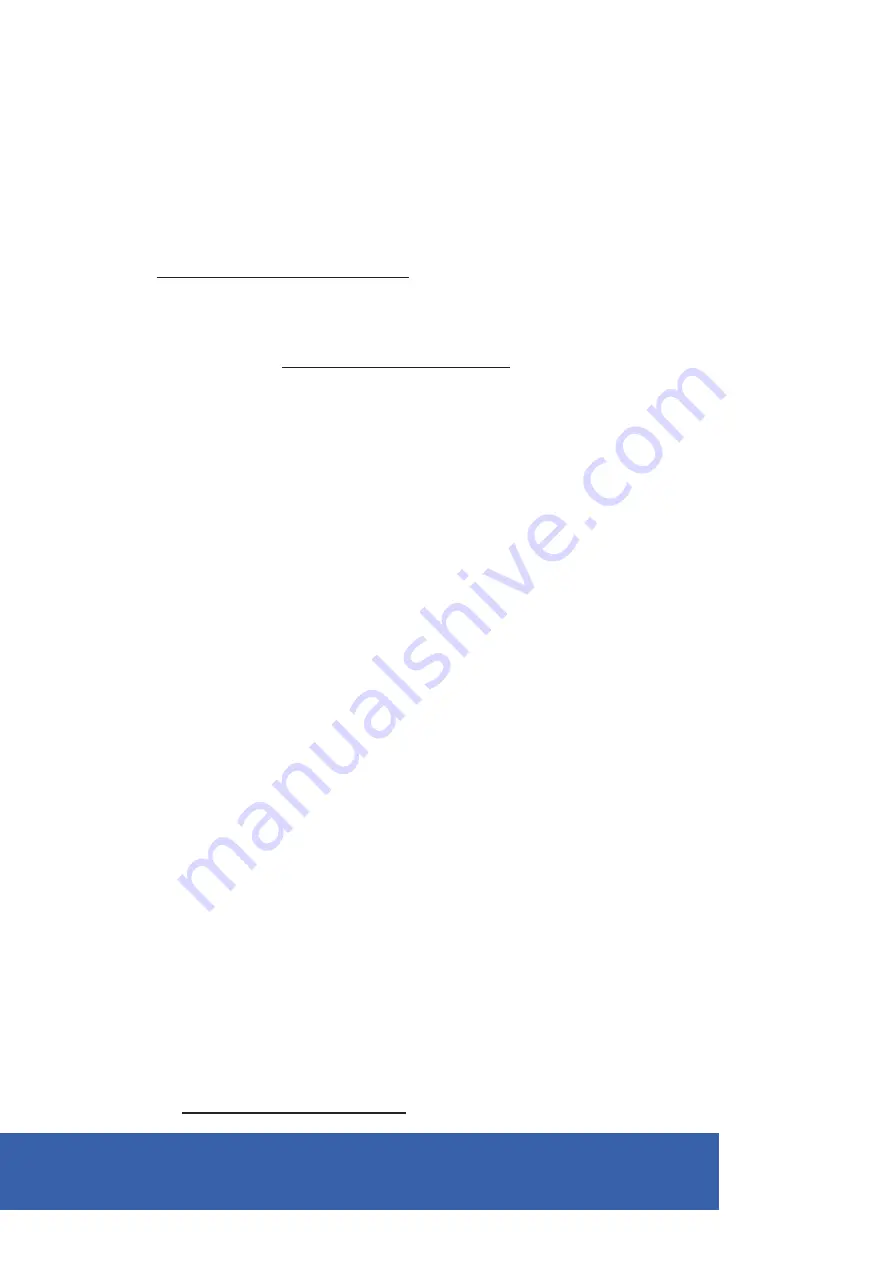
Maintenance
Regular servicing and maintenance of emergency safety shower and eye/face wash equipment is essential to ensure
correct functionality. All services and weekly activations must be recorded to ensure a full history is maintained as per
European and International standard requirements.
Weekly activation
All equipment should be visually inspected and activated at least once a week to ensure it is operating properly, to clear
the line of any sediment build up and check that the water runs clear.
Where fitted, the external test handle can be used for ease.
Please visit www.hughes-safety.com/weekly-activation to download the checklist and video detailing what to look out for to
remain compliant.
Servicing and cleaning
Hughes recommend equipment be serviced and cleaned regularly, and at least every 6 months. To purchase spare parts call
us on (1) 866-312-1652 or email
Periodic analysis of the water quality is recommended to ensure there is no build-up of harmful bacteria.
Regular cleaning of the outside of the emergency equipment is recommended. Abrasives or solvents must not be used to
clean the unit as this can damage the surface or affect the instruction stickers.
Safety showers:
•
Remove the shower head/nozzle periodically to clean, disinfect and ensure any build-up of debris or bacteria is
removed.
•
Remove the shower rose and replace after flushing.
Eye and eye/face washes:
•
The fine mesh strainers should be cleaned regularly, particularly in the first 6 months of service as there may be
contamination of the water from dirt, jointing compounds, etc. which may have remained in the pipework following
installation, despite the recommended flushing procedure.
•
Nozzles should be cleaned regularly; the frequency will depend on the ambient conditions of the installation.
•
Diffusers can be unscrewed for cleaning.
•
To clean the ‘Y’ strainer filter basket remove the strainer housing using a 22mm socket. The filter basket can be
found inside the housing and can easily be removed for cleaning. To ensure hygienic operation, the diffusers and
filter baskets should be replaced if they become excessively dirty or damaged.
•
After any cleaning or maintenance work has been carried out on the equipment it is imperative that the eye and
eye/face washes are given a full operational test and any flow regulator or volume control screws are re-adjusted
to ensure optimum performance. It is recommended that eye wash diffusers are replaced every six months.
Electrical equipment:
•
Thorough visual inspections should be carried out to check for external damage to the electrical units, their cables
or the junction boxes. Should any part be found to be damaged, this must be reported and repaired or replaced
as soon as possible. A further test should be carried out to establish that it functions as intended. Any additional
electrical tests should be carried out at the discretion of a qualified electrician.
Out of Service Procedure
In the event of an emergency safety shower, eye bath or eye/face wash unit being temporarily out of service, a standard
procedure should be followed.
•
Place a sign on the unit indicating it is ‘Out of Service’.
•
Notify the relevant manager/supervisor of the area that the unit is out of service
•
Prohibit or suspend any work where there is a significant hazard requiring use of the unit
•
If work cannot be prohibited or suspended, a portable unit must be provided to supply the initial wash only, after
which it will be necessary to move the person to a plumbed emergency safety shower, eyebath or eye/face wash
unit to complete the procedure.
Note: Portable units are not acceptable as a long-term substitute for permanent locations.
A selection of our emergency safety showers are available to hire. Ensure your workforce are protected around
the clock, visit www.hughes-safety.com/us/rentals for more information.
If you require further assistance please contact us:
T: (1) 866-312-1652