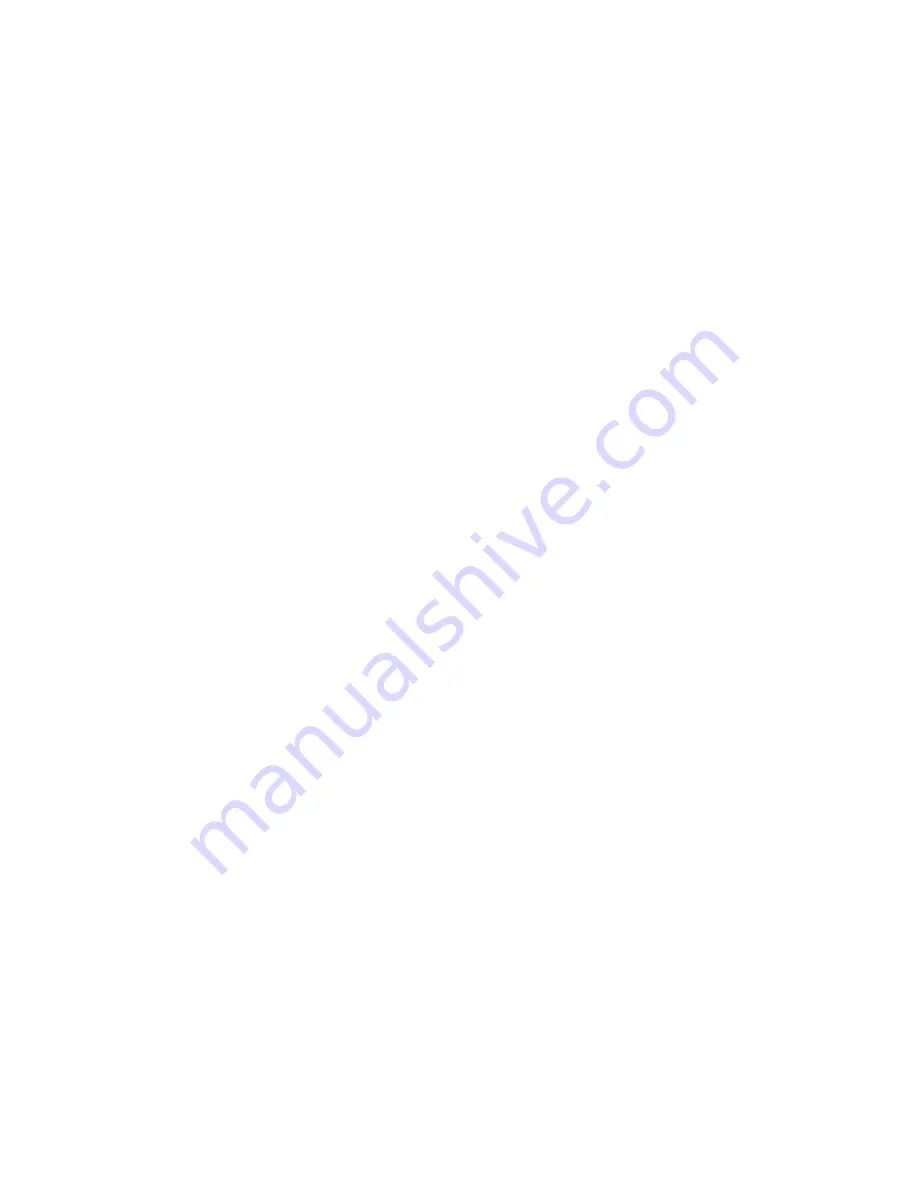
----------------------------------------------------------------------------
1. CHEMICAL PRODUCT/COMPANY IDENTIFICATION
----------------------------------------------------------------------------
HYDROCLEAR(R) DEXRON(R) III/MERCON(R) Automatic Transmission Fluid
MSDS Code: ATFC0089 Revised: 14-Mar-2000
"HYDROCLEAR" is a registered trademark of Conoco.
"DEXRON" is a registered trademark of General Motors Corp.
"MERCON" is a registered trademark of Ford Motor Company.
Product Use: Automatic Transmission Fluid
Conoco Blend Code: 46682
MANUFACTURER/DISTRIBUTOR
Conoco Inc.
P.O. Box 2197
Houston, TX 77252
PHONE NUMBERS
Product Information: 1-281-293-5550
Transport Emergency: CHEMTREC 1-800-424-9300 (U.S. & Canada)
703-527-3887 (elsewhere; call collect)
Medical Emergency: 1-800-441-3637
-------------------------------------------------------------------------
2. COMPOSITION/INFORMATION ON INGREDIENTS
-------------------------------------------------------------------------
COMPONENTS %
Base oils >85
Proprietary additives <15
If oil mist is generated, exposure limits apply (see Section 8).
-------------------------------------------------------------------------
3. HAZARDS IDENTIFICATION
-------------------------------------------------------------------------
--- EMERGENCY OVERVIEW ---
APPEARANCE / ODOR
Red liquid / mild petroleum hydrocarbon odor.
OSHA REGULATORY STATUS
This material is classified as nonhazardous under OSHA Regulations.
HMIS RATING
Health: 1; Flammability: 1; Reactivity: 0
___________________________________
Potential Health Effects
Primary Route of Entry: Skin
The product, as with many petroleum products, may cause minor skin, eye, and
lung irritation, but good hygienic practices can minimize these effects.
Normal use of this product does not result in generation of an oil mist. However if
an oil mist is generated, overexposure can cause minor and reversible irritation to
the eyes, skin, and especially the lungs. Proper personal protective equipment
and sufficient ventilation can provide adequate protection.
Carcinogenicity Information
None of the components present in this material at concentrations equal to or
greater than 0.1% are listed by IARC, NTP, OSHA or ACGIH as a carcinogen.
------------------------------------------------------------------------
4. FIRST AID MEASURES
------------------------------------------------------------------------
INHALATION
If inhaled, remove to fresh air. If not breathing, give artificial respiration. If
breathing is difficult, give oxygen. Call a physician.
SKIN CONTACT
Wash skin thoroughly with soap and water. If irritation develops and persists,
consult a physician.
EYE CONTACT
In case of contact, immediately flush eyes with plenty of water for at least 15
minutes. Call a physician.
INGESTION
Material poses an aspiration hazard. If swallowed, do not induce vomiting.
Immediately give 2 glasses of water. Never give anything by mouth to an
unconscious person. Call a physician.
If vomiting occurs naturally, have victim lean forward to reduce the risk of
aspiration.
Notes to Physicians
Activated charcoal mixture may be administered. To prepare activated charcoal
mixture, suspend 50 grams activated charcoal in 400 mL water and mix
thoroughly. Administer 5 mL/kg, or 350 mL for an average adult.
---------------------------------------------------------------------------
5. FIRE FIGHTING MEASURES
---------------------------------------------------------------------------
Flammable Properties
Flash Point (typical): 370 F (188 C)
Flash Point (minimum): 351 F (177 C)
Method: COC
NFPA Classification: Class IIIB Combustible Liquid.
NFPA Rating: Health 0; Flammability 1; Reactivity 0
Extinguishing Media
Water Spray, Foam, Dry Chemical, CO2.
Fire Fighting Instructions
Water or foam may cause frothing. Use water to keep fire-exposed containers
cool. Water may be used to flush spills away from exposures.
Products of combustion may contain carbon monoxide, carbon dioxide, and other
toxic materials. Do not enter enclosed or confined space without proper protective
equipment including respiratory protection.
---------------------------------------------------------------------------
6. ACCIDENTAL RELEASE MEASURES
---------------------------------------------------------------------------
Safeguards (Personnel)
NOTE: Review FIRE FIGHTING MEASURES and HANDLING (PERSONNEL)
sections
before proceeding with clean-up. Use appropriate PERSONAL PROTECTIVE
EQUIPMENT during clean-up.
Remove source of heat, sparks, and flame.
Initial Containment
Dike spill. Prevent material from entering sewers, waterways, or low areas.
Spill Clean Up
Recover free liquid for reuse or reclamation. Soak up with sawdust, sand, oil dry
or other absorbent material.
---------------------------------------------------------------------------
7. HANDLING AND STORAGE
---------------------------------------------------------------------------
Handling (Personnel)
Avoid breathing vapors or mist. Avoid contact with eyes. Avoid prolonged or
repeated contact with skin. Wash thoroughly after handling. Wash contaminated
clothing prior to reuse.
Handling (Physical Aspects)
Close container after each use. Do not pressurize, cut, weld, braze, solder, grind,
or drill on or near full or empty container. Empty container retains residue (liquid
and/or vapor) and may
explode in heat of a fire.
Storage
Store in accordance with National Fire Protection Association recommendations.
Store in a cool, dry place. Store away from heat, sparks and flames, oxidizers.
Close container after each use.
---------------------------------------------------------------------------
8. EXPOSURE CONTROLS/PERSONAL PROTECTION
---------------------------------------------------------------------------
Engineering Controls
VENTILATION
Normal shop ventilation.
Personal Protective Equipment
RESPIRATORY PROTECTION
None normally required except in emergencies or when conditions cause
excessive airborne levels of mists or vapors. Select appropriate NIOSH-approved
respiratory protective equipment when exposed to sprays or mists. Proper
respirator selection should be determined by adequately trained personnel and
based on the contaminant(s), the degree of potential exposure, and published
respirator protection factors.
PROTECTIVE GLOVES
Should be worn when the potential exists for prolonged or repeated skin contact.
NBR or neoprene recommended.
EYE PROTECTION
Safety glasses with side shields.
OTHER PROTECTIVE EQUIPMENT
Coveralls with long sleeves if splashing is probable.