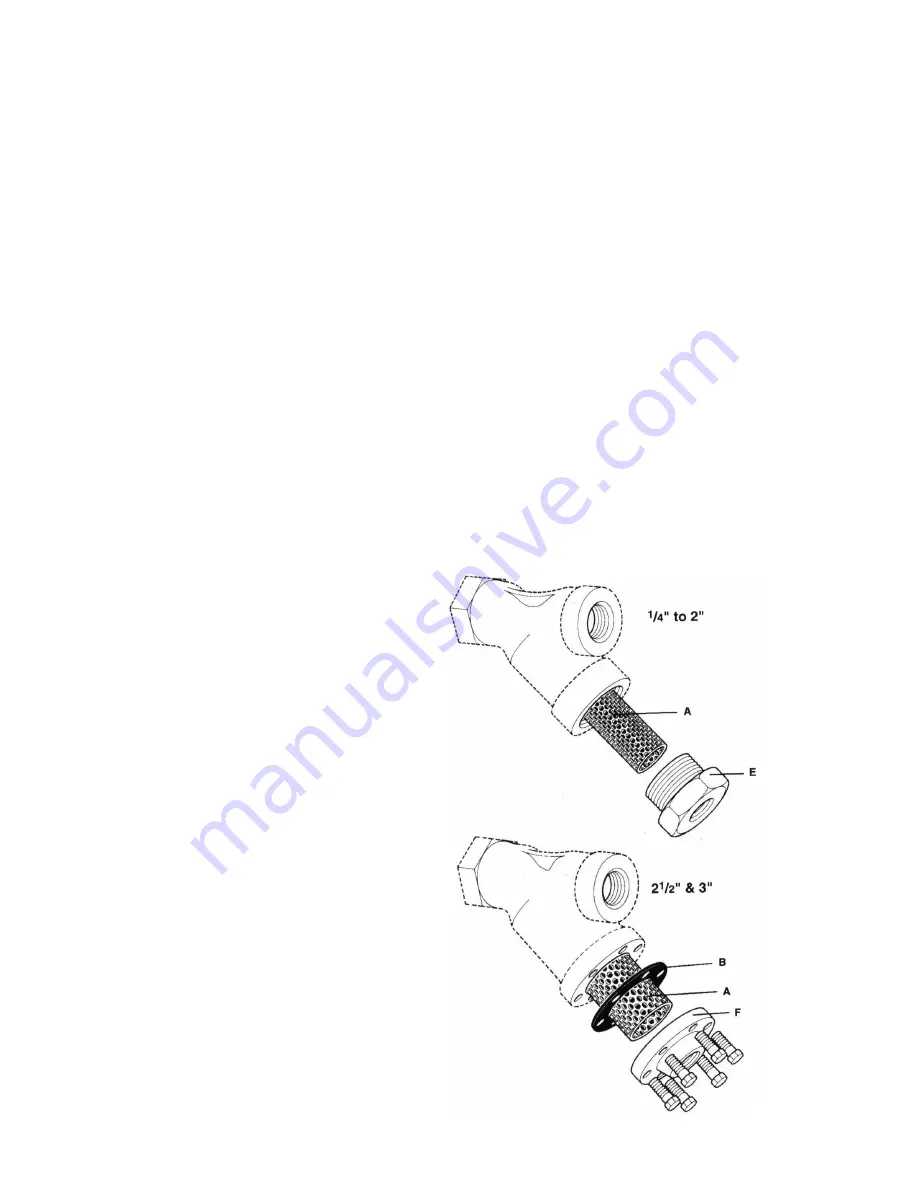
cement lining includes an inspection to ensure that the lining is applied to the
correct thickness, covers all appropriate surfaces, and is free from defects or
cracks greater than 3 mm (1/8”) in width. Any deficiencies are repaired at the
factory prior to shipment. However, it is characteristic to find hairline cracks
in the cement lining prior to initial installation. After the vessel is first filled, the
water will work its way into these cracks and begin the corrosion process. At
the same time the cement lining undergoes a “wet curing” process whereby the
cement absorbs water and expands. The water that is absorbed into the lining
becomes trapped between the cement lining and the steel tank and once the
cement is fully absorbed with water, the water in contact with the steel tank
becomes deoxygenated which serves to protect the steel vessel. In addition, the
cement leaches minerals and various impurities from the water which fills and
“heals” the cracks. This “healing” together with the “wet curing” and expansion
of the cement prevents any ongoing corrosion. In the unlikely event a crack
greater than 3 mm (1/8”) develops, the cement lining can be easily repaired in
the field. For repair procedures please contact Hubbell
a.
Shut down unit as described in Section II.
b.
Close valve on hot water outlet piping.
c.
Open valve on drain piping.
d.
Cold water inlet line pressure will be strong enough to flush sediment from
the bottom of the tank out through the drain. Let water run for 3-4 minutes.
e.
Clean strainer filter, see below.
f.
Close drain valve.
g.
Open hot water valve.
h.
Re-start unit as described in Section II.
17.
Clean strainer filter. Perform
annually or more often , if
required.
a.
Remove blowoff bushing
(E) or cap (F), as required.
b.
Remove gasket (B), if
required.
c.
Remove, clean, and re-
install screen (A).
d.
Replace gasket (B).
e.
Re-install blowoff bushing
(E) or cap (F), as required.
15
Summary of Contents for ST
Page 4: ...4 ...
Page 5: ...NOMENCLATURE FOR PARTS 5 ...
Page 6: ...NOMENCLATURE FOR ACCESSORY PARTS 6 ...
Page 16: ...16 ...
Page 17: ...SINGLE SAFETY SOLENOID SYSTEM if installed 17 ...
Page 23: ...NOTES 23 ...