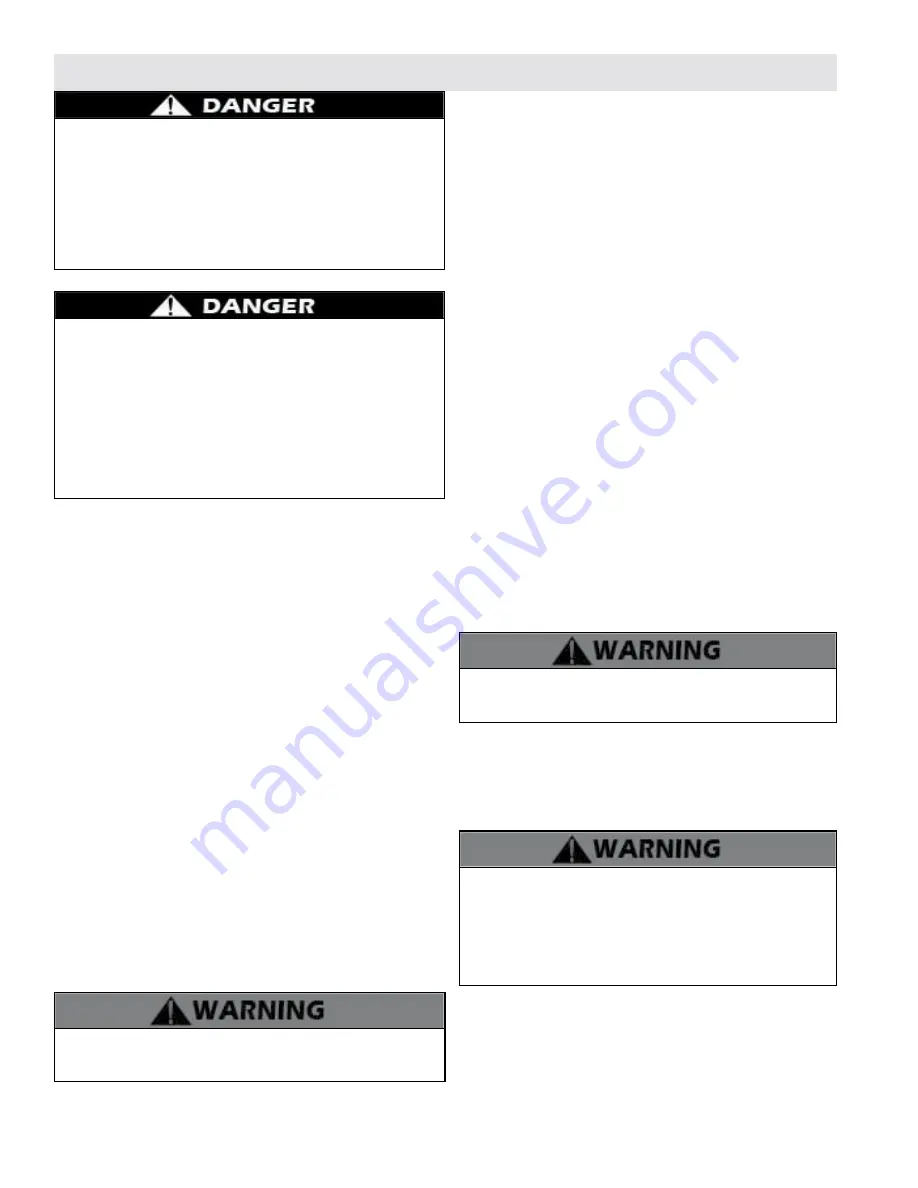
lp-672 Rev. 000 Rel. 002 Date 10.3.18
56
Part 12 - Maintenance
The water heater must be inspected and serviced annually,
preferably at the start of the heating season, by a qualified service
technician. In addition, the maintenance and care of the water heater
as outlined in this manual must be performed by the user/owner to
assure maximum efficiency and reliability. Follow the maintenance
procedures given throughout this manual. Failure to perform the
service and maintenance or follow the directions in this manual
could damage the water heater or system components, resulting in
substantial property damage, severe personal injury, or death.
Check the Surrounding Area
To prevent the potential of substantial property damage, severe
personal injury, or death, eliminate all the materials listed in Table
8. from the area surrounding the water heater and the vicinity of the
combustion air intake. If contaminates are found:
•
Remove products immediately from area.
•
If contaminates have been there for an extended period, call
a qualified service technician to inspect the water heater for
possible damage from acid corrosion.
If products cannot be removed, immediately call a qualified service
technician to re-pipe the combustion air intake piping away from
the contaminated areas.
Combustible/Flammable Materials
Do not store combustible materials, gasoline, or other flammable
vapors or liquids near the water heater. If found, remove these
materials immediately.
Air Contaminates
If allowed to contaminate combustion air, products containing chlorine
or fluorine will produce acidic condensate that will cause significant
damage to the water heater. Read the list of potential contaminates
and areas likely to have these contaminates in Table 8. If any of these
contaminates are in the room where the water heater is located, or
combustion air is taken from one of the areas listed, the contaminants
must be removed immediately or the intake pipe must be relocated to
another area.
Ensure the Water Heater Cabinet is Closed
Ensure the water heater cabinet is closed. Tighten the two upper and
lower screws to secure it. The cabinet must be closed while the water
heater is running.
Check the Power Source
Make sure the power cord is properly connected. The main power line
is connected to the manual switch box inside the water heater.
Check the Status of the Control Panel
Observe the Control Panel to ensure the water heater is powered on,
and to check for any error codes. Clear any debris from the panel.
Check Exhaust Vent and Intake
Verify that the water heater exhaust vent and intake clean and free of
obstructions, leakage, or deterioration. Remove any debris from the
exhaust vent or intake openings.
Notify a qualified service technician immediately if any problems are
found or if removing the debris does not allow the water heater to
operate correctly.
Failure to inspect the water heater exhaust vent and intake system
and have it repaired by a qualified service technician can result in
vent system failure, causing severe personal injury or death.
Visually inspect the intake piping for any signs of blockage. Inspect
the entire length of the intake pipe to ensure piping is intact and all
joints are properly sealed. Inspect the intake pipe bracing. Ensure
bracing is undamaged and in good condition. Notify a qualified
service technician if any problems are found.
Check Pressure Relief Valve
•
Visually inspect the primary pressure relief valve and
discharge pipe for signs of weeping or leakage.
•
If the pressure relief valve often weeps, the expansion tank
may not be operating properly. Immediately contact a
qualified service technician to inspect the water heater and
system.
Check the Condensate Drain System
•
While the water heater is running, check the discharge end
of the condensate drain tubing. Ensure no flue gas is leaking
from the condensate drain tubing by holding your fingers
near the opening.
•
If you notice flue gas leaking from the opening, this indicates
a dry condensate drain trap. If problem persists, contact a
qualified service technician to inspect the water heater and
condensate line and refill the condensate trap.
•
If applicable, check the condensate neutralizer and ensure it
is full of condensate neutralizing marble chips.
Check Primary and Gas Piping
•
Remove the water heater cover and perform a gas leak
inspection following Operating Instructions, page 2, this
manual. If gas odor or leak is detected, follow procedures on
page 2. Call a qualified service technician.
•
Visually inspect for leaks around the internal water heater
water connections and around the heat exchanger. Visually
inspect the external system piping, circulators, and system
components and fittings. Immediately call a qualified service
technician to repair any leaks
Have leaks fixed at once by a qualified service technician. Failure
to comply could result in substantial property damage, severe
personal injury, or death.
Operate Pressure Relief Valve
•
Before proceeding, verify that the relief valve outlet has been
piped to a safe place of discharge, avoiding any possibility of
scalding from hot water.
•
Shut power off to the water heater. To avoid scalding, wait
for water heater to cool before operating the relief valve.
To avoid water damage or scalding due to relief valve operation, a
discharge line must be connected to the valve outlet and directed
to a safe place of disposal. This discharge line must be installed
by a qualified service technician or heating/plumbing installer
in accordance with the water heater installation manual. The
discharge line must be terminated so as to eliminate possibility
of severe burns or property damage should the valve discharge.
•
Lift the relief valve lever. If water flows freely, release the
lever and allow the valve to seat. Watch the end of the relief
valve discharge pipe to ensure that the valve does not weep
after the line has had time to drain. If the valve weeps, lift
the lever again to attempt to clean the valve seat. If the valve
does not properly seat and continues to weep, contact a
qualified service technician to inspect the valve and system.
•
If water does not flow from the valve when you completely
lift the lever, the valve or discharge line may be blocked.