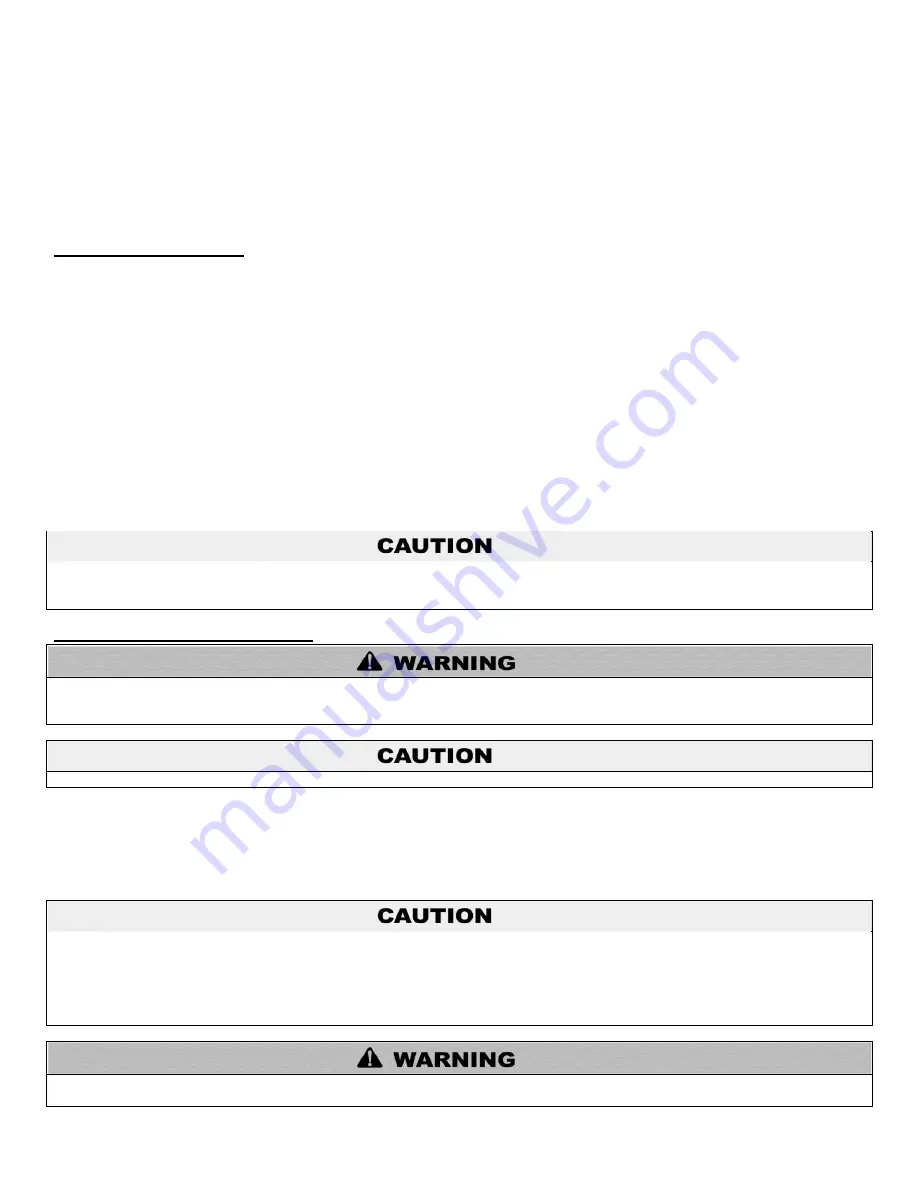
10
LP- 446 REV. 9.3.14
Flow Protection
– The supplied flow switch is designed to protect the boiler in the event of low flow conditions. The boiler control will
also monitor flow through the heat exchanger by monitoring the return and supply sensor and will shut down the burner before
overheating occurs.
System Pipe Sensor
– This sensor is designed to be used in a cascade system. When placed on the supply line feeding the storage
tank, the system pipe sensor measures the temperature of return water and communicates with the control system to modulate the
firing rate of the connected boilers.
Indirect Tank Sensor
(optional)
– Monitors storage tank temperature.
C. OPTIONAL EQUIPMENT
Below is a list of optional equipment available from HTP:
Indirect Tank Sensor (Part # 7250P-325)
4” Stainless Steel Outside Termination Vent Kit (V2000)
6” Stainless Steel Outside Termination Vent Kit (V3000)
High and Low Gas Pressure Switch Kit with Manual Reset (Part # 7350P-600)
U.L. 353 Compliant Low Water Cut-Off Interface Kit with Manual Reset (Part # 7350P-601)
Alarm System (Part # 7350P-602) (to monitor any failure)
PC Connection Kit (Part # 7250P-320)
Condensate Neutralizer (Part # 7350P-611)
Caster Kit (Part # 7350P-604)
These additional options may be purchased through your HTP distributor.
PART 3 – PREPARE BOILER LOCATION
Carefully consider installation when determining boiler location. Please read the entire manual before attempting installation. Failure to
properly take factors such as boiler venting, piping, condensate removal, and wiring into account before installation could result in
wasted time, money, and possible property damage and personal injury.
A. BEFORE LOCATING THE BOILER
Incorrect ambient conditions can lead to damage to the heating system and put safe operation at risk. Ensure that the boiler installation
location adheres to the information included in this manual. Failure to do so could result in property damage, serious personal injury, or
death.
Failure of boiler or components due to incorrect operating conditions IS NOT covered by product warranty.
1. Installation Area (Mechanical Room) Operating Conditions
Ensure ambient temperatures are higher than 32
o
F/0
o
C and lower than 104
o
F/40
o
C.
Prevent the air from becoming contaminated by the products, places, and conditions listed in this manual, Part 3, Section F.
Avoid continuously high levels of humidity
Never close existing ventilation openings
The service life of the boiler’s exposed metallic surfaces, such as the casing, as well as internal surfaces, such as the heat exchanger,
are directly influenced by proximity to damp and salty marine environments. In such areas, higher concentration levels of chlorides from
sea spray coupled with relative humidity can lead to degradation of the heat exchanger and other boiler components. In these
environments, boilers must not be installed using direct vent systems which draw outdoor air for combustion. Such boilers must be
installed using room air for combustion. Indoor air will have a much lower relative humidity and, hence, potential corrosion will be
minimized.
This boiler is certified for indoor installations only. Do not install the boiler outdoors. Failure to install this boiler indoors could result in
substantial property damage, severe personal injury, or death.
Summary of Contents for 500 HL
Page 12: ...12 LP 446 REV 9 3 14 Figure 2 Dimensions and Specifications ...
Page 21: ...21 LP 446 REV 9 3 14 H PIPING DIAGRAMS Figure 6 ...
Page 44: ...44 LP 446 REV 9 3 14 E GAS VALVE Figure 26 Mod Con 500 Gas Valve ...
Page 52: ...52 LP 446 REV 9 3 14 Figure 33 Mod Con Internal Connection Diagram LP 428 K ...
Page 71: ...71 LP 446 REV 9 3 14 Figure 36 ...
Page 72: ...72 LP 446 REV 9 3 14 Figure 37 ...
Page 73: ...73 LP 446 REV 9 3 14 Figure 38 ...
Page 74: ...74 LP 446 REV 9 3 14 Figure 39 ...
Page 77: ...77 LP 446 REV 9 3 14 ...
Page 78: ...78 LP 446 REV 9 3 14 ...