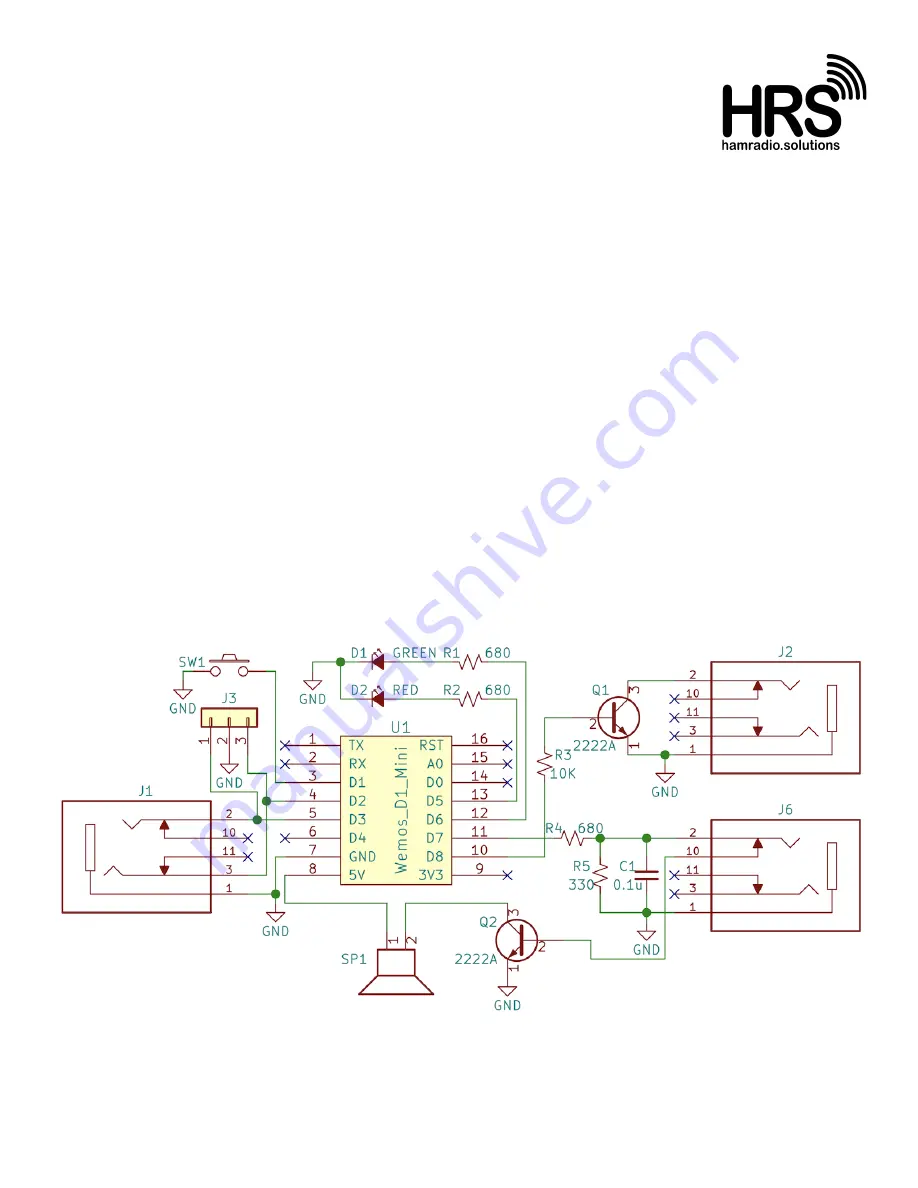
Ham Radio Solutions
CW Hotline
Assembly Manual
Version 0.5 1-20-2022
The Ham Radio Solutions CW Hotline is a fairly simple construction project that can usually be built in
about two hours. You will need a low wattage pencil-type soldering iron with a small tip, some thin
solder, a pair of diagonal cutters and a Phillips head screwdriver. Desoldering braid may be required
to correct soldering mistakes. Be sure to wear eye protection when soldering and cutting leads.
Most parts, except for a few at the end, should be inserted into the side of the PCB with the jack
silkscreens J1, J2, J6. Unless otherwise indicated, parts should be flush with the PCB. After
inserting, turn the board over and solder the leads to the pads on the other side. It is often helpful to
just solder one lead, then ensure the component is correctly positioned before soldering the
remaining leads. Be sure to only solder the correct pads, and do not let any solder touch any other
pad or trace. Trim any excess leads with diagonal cutters after soldering each batch of components.
The checklist will be useful to ensure all components are properly assembled.
Build slowly and follow the instructions. Use the images to confirm component placement. CW
Hotline may be built with a straight key, Iambic paddles, or neither. It is recommended to drill the
case first, then use the case to aid in placing some components on the PCB.
Schematic