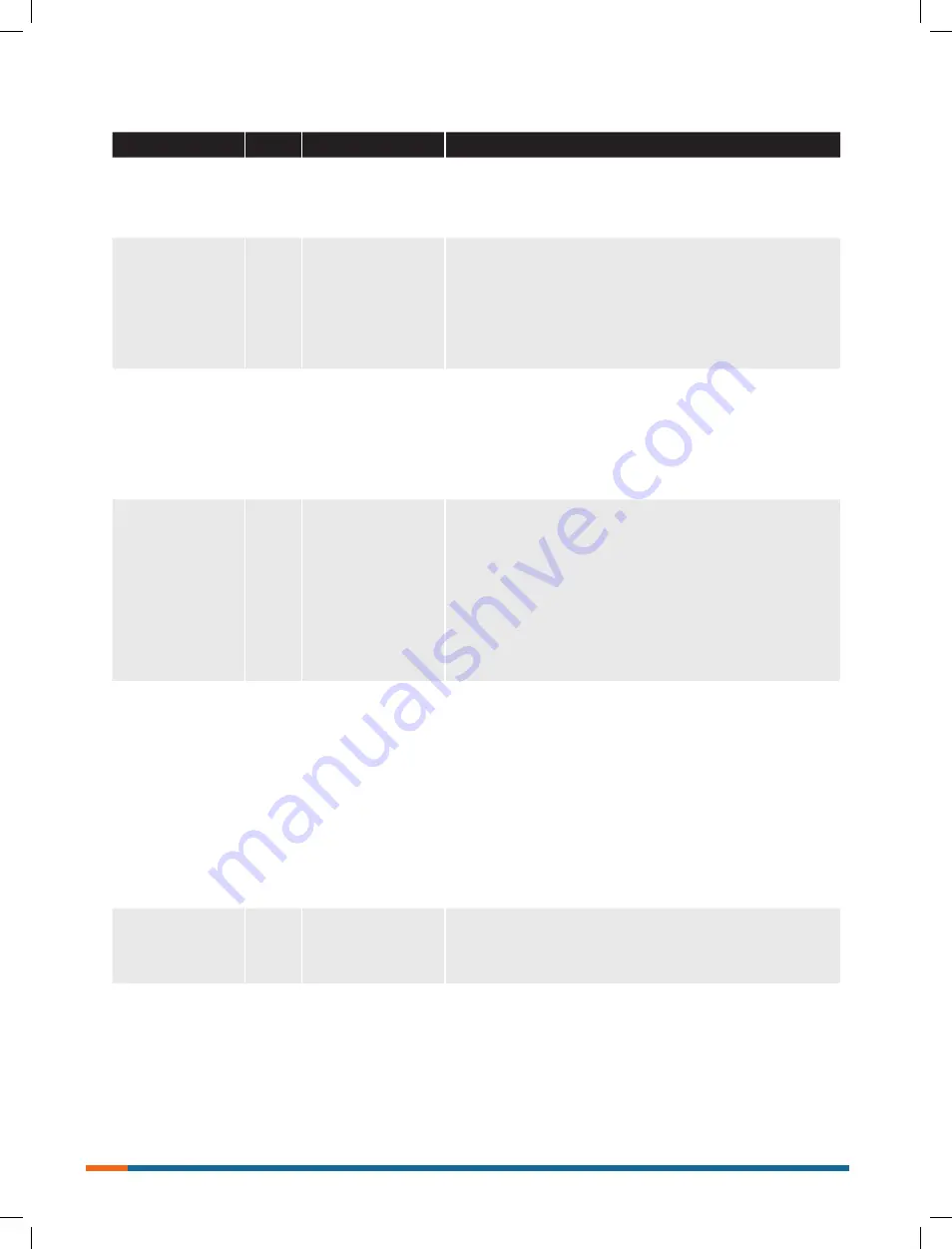
ISRB-2009, Rev. 02_17.
8
Troubleshooting Checklist
Trouble
Item
Possible Cause
Remedy
No flow
1
2
3
Speed too low
Wrong rotation
Obstruction in piping
Check by tachometer and compare with published
performance.
Compare actual rotation with Figure 1, change driver if wrong.
Check piping, valves, silencer to assure open flow path.
Low capacity
4
5
6
7
Speed too low
Excessive pressure
rise
Obstruction in piping
Excessive slip
See item 1, if belt drive, check for slippage and re-adjust
tension.
Check inlet vacuum and discharge pressure and compare with
published performance.
See item 3.
Check inside of casing for worn or eroded surfaces causing
excessive clearances
Excessive power
8
9
10
11
Speed too high
Excessive pressure
rise
Impeller rubbing
Scale, sludge, rust or
product build up
Check speed and compare with published performance.
See item 5
Inspect outside of cylinder for high temperature areas, then check
for impeller contact at these points. Correct blower mounting, drive
alignment.
Clean blower appropriately
Damage to bearings
or gears
12
13
14
15
16
Inadequate
lubrication
Excessive
lubrication
Excessive
pressure rise
Coupling
misalignment
Excessive belt
tension
Check oil sump levels in gear and drive end headplates
Check oil levels. If correct, drain and refill with clean oil of
recommended grade.
See item 5.
Check carefully. Re-align if questionable.
Re-adjust for correct tension.
Vibration
17
18
19
20
21
22
23
24
Misalignment
Impellers rubbing
Worn bearings/gears
Unbalanced or
rubbing impeller
Driver or blower
loose
Piping resonances
Scale/sludge
build-ups
Casing strain
See item 15
See item 10
Check gear backlash and conditions of bearings and replace as
indicated.
Scale or process material may build up on casing and impellers, or
inside impellers. Remove build-up to restore original clearances and
impeller balance.
Tighten mounting bolts securely.
Determine whether standing wave pressure pulsations are present
in the piping.
Clean out interior of impeller lobes to restore dynamic balance.
Re-work piping alignment to remove excess strain.
Driver stops, or will
not start
25
26
Impeller stuck
Scale, sludge, rust or
product build-up
Check for excessive hot spot on headplate or cylinder.
See item 10. Look for defective shaft bearing and/or gear
teeth.
Clean blower appropriately
Summary of Contents for Roots 412 HPT
Page 1: ...www howden com Roots 412 HPT Blower Installation Operation Maintenance Manual...
Page 11: ...11 ISRB 2009 Rev 02_17...
Page 12: ...ISRB 2009 Rev 02_17 12...
Page 13: ...13 ISRB 2009 Rev 02_17...
Page 14: ...ISRB 2009 Rev 02_17 14...
Page 15: ...15 ISRB 2009 Rev 02_17...