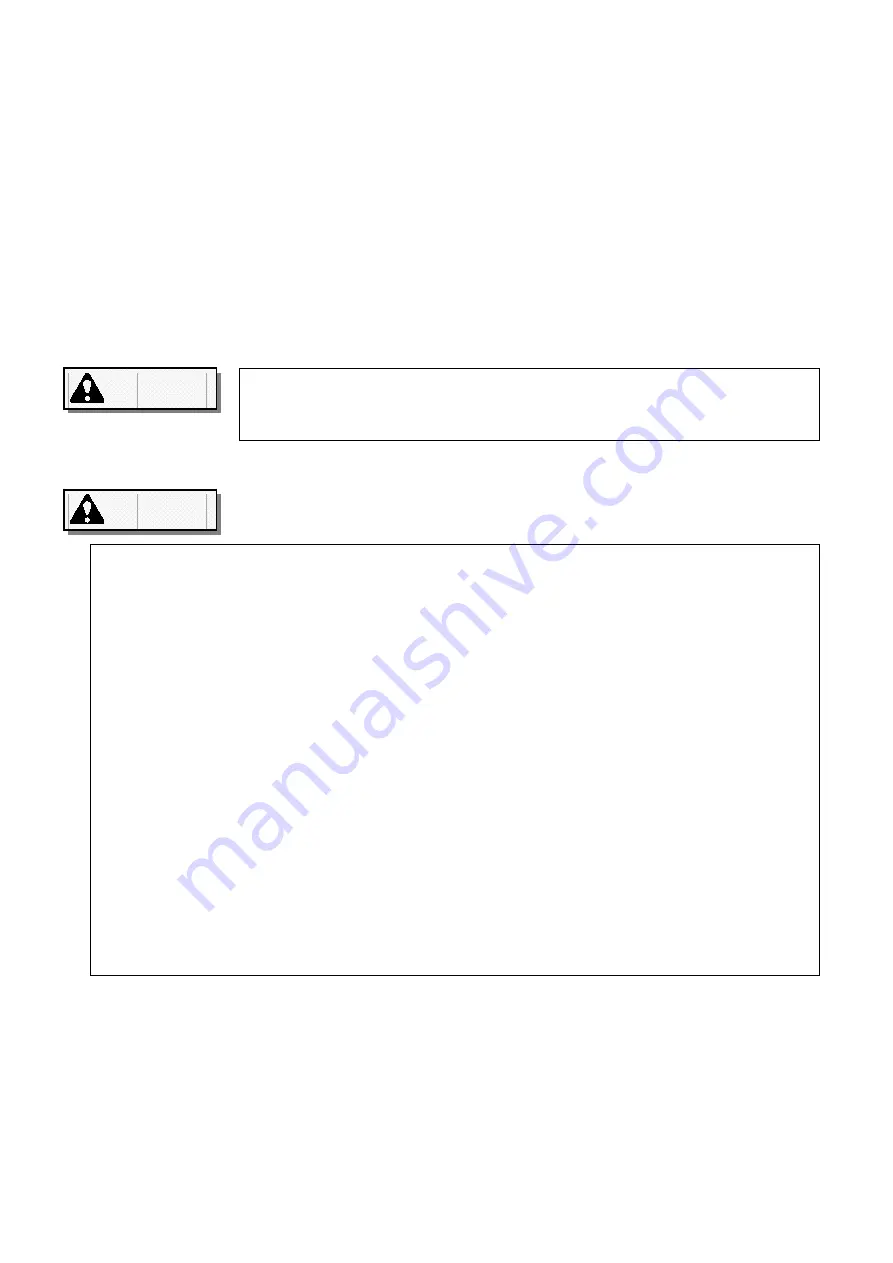
- -
18
4.4 Setting Safe Rotational Speed
ANSI B 11.6-1984 section 7.1.9 suggests guidelines for setting a safe rotational speed.
A safe rotational speed will be a function of the consideration of among other things, the degree
of wear and tear then existing on the jaws of the chuck, which may effect their ability to grip the
work piece. The jaws or chuck body should be replaced and/or properly refurbished if the
surface of the master jaw or the chuck body deteriorates so that gripping force is lost. In
addition, depending upon the usage received by the chuck, the gripping force should be
measured periodically with a gage. There should be a regular inspection for cleanliness as a
function of the ability of the chuck to grip a work piece even though its gripping pressure may
remain constant. The chuck speed should be reviewed with each change in job. Including
reference to the feeding speed of a work piece, a change in the size and weight of a work piece,
the composition of a work piece, the type of cuts or machining performed and the speed or rate
of cut.
Do not leave the chuck in the state where its top jaws is not
tightened. If the spindle is rotated in such a state, the jaws will fly
out, causing serious or fatal injury to the operator or bystanders.
Aside from damage to the chuck, the chuck will be able to maintain a constant
gripping force upon a work piece assuming that the hydraulic or pneumatic
operating pressures do not change. However, the ability of the chuck to hold a work
piece will deteriorate with wear and tear on the surfaces of the jaws of the chuck,
which will tend to reduce the coefficient of friction between the jaws and the work
piece. The ability of the jaws to hold the work piece will depend upon the work piece
itself. A larger diameter, heavier work piece, for example, will exert greater force
against the jaws of the chuck, and therefore, will more easily overcome the gripping
capability of the jaws of the chuck. Increase in the rpm will also add to the force,
which tends to pull the work piece out of the chuck, and improper maintenance in
the form of dirt, rust, improper or inadequate lubrication will also diminish the ability
of the chuck to hold a work piece. Finally, the manner in which the work piece is
machined in the lathe or machining center will determine the precise forces exerted
on the work piece, and therefore, on the jaws of the chuck, and may overcome the
ability of the jaws to hold the work piece. It is therefore absolutely required that the
ability of the jaws of the chuck to hold the work piece be reviewed with each new
set-up or job and periodically during the course of a long job. Machine operations of
the lathe which produce forces sufficient to overcome the gripping force of the jaws
of this chuck will cause the work piece to fly out which, in turn, may cause severe
injury or death to the operator or bystanders.
WARNING
WARNING
Summary of Contents for H3EF
Page 4: ...2 M6 M8 M10 M12 M16 N m 12 1 29 4 57 9 101 161...
Page 5: ...3 8 1 4 1 EP...
Page 6: ...4 1 1 1 1 1 1 1 1 3 H3EF H3EF H3EF H3EF JIS 8 1 2 1 2 1 2 1 2 3 T 2 1 2 1 2 1 2 1 kg 1...
Page 11: ...9 3 3 3 3 5 5 5 6 8 M10 M12 L1 mm 20 24 mm 15 19 mm 10 11 N m 57 9 101 5 8 9 10...
Page 12: ...10 3 3 3 3 3 3 3 3 1 4 1 4 12 11...
Page 18: ...16 4 1 4 1 4 1 4 1 EP 8 1 4 1 EP 100 0004 1 5 1 23F TEL 0120 77 6278 FAX 03 3287 1203 17...
Page 19: ...17 4 2 4 2 4 2 4 2 1000 4 2 1 4 2 1 4 2 1 4 2 1 M4 90 M4 90 4 2 2 4 2 2 4 2 2 4 2 2 18...
Page 20: ...18 4 4 4 4 4 4 4 4 ANSI B11 6 1984 section 7 1 9...
Page 22: ...20...
Page 26: ...24 6 5 6 5 6 5 6 5 6 8 M12 L 95 16 L 105 3 B 3 B 8 B 10 B 4 B 10 B 14 1 M10 1...
Page 27: ......