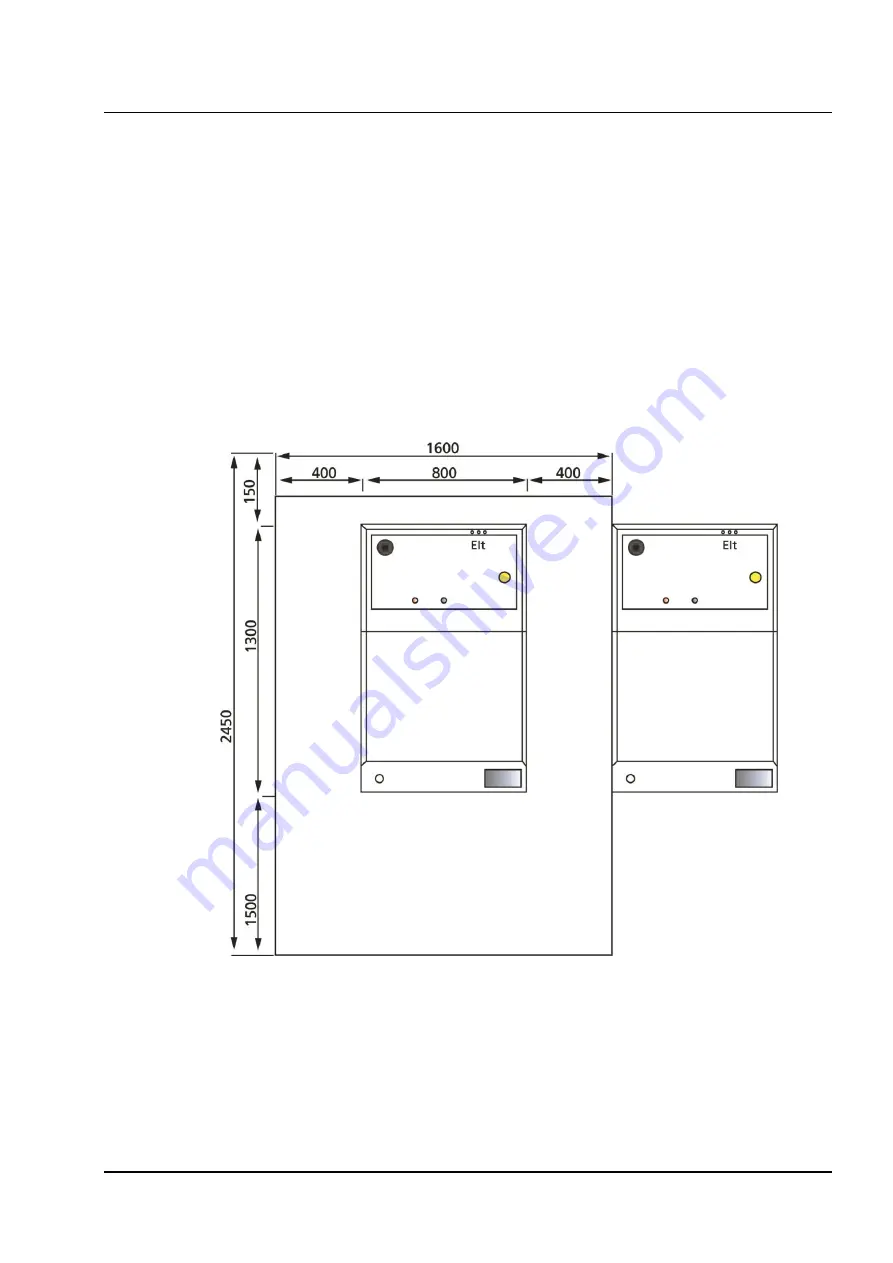
Technical documentation
Subject to modifications
47 of 131
4.4.12. Installation diagram
The installation of the plant is carried out in accordance with Hoval's specifications.
All plant and electrical supply lines must be placed and installed in accordance with the
installation plan or Hoval's specifications.
An open area (working area) is required for all work on the CHP plant, in particular
installation, maintenance and service. For work in front of the CHP plant (front), a larger
clearance is required in order to be able to remove and insert the equipment set (engine
and generator). The room height should be at least 2,000 mm. Deviations from the
specified minimum dimensions may involve additional work and are only possible after
consultation.
Please also refer to the
Figure 6: Installation diagram
for the defined dimensions for
determining the total space requirement. The dimensions and weights of the individual
plant components can be found in the manufacturer's specifications in the technical
documentation.
Figure 6: Installation diagram
The dimensions are given in "mm" and depend on the external dimensions of the CHP
plant.