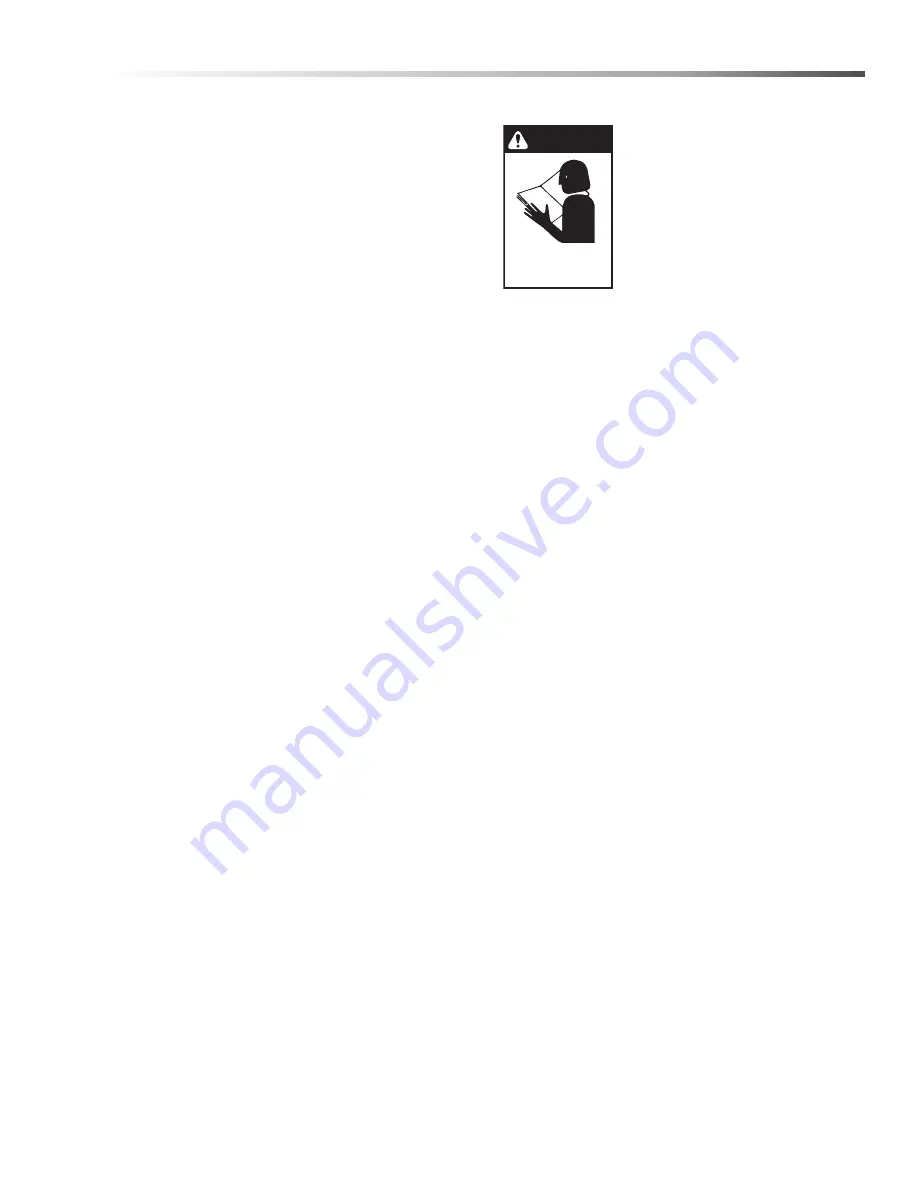
13
Operations
Defective pipes or fittings should be replaced and not
repaired. Never use a flame or fire in any form to locate
gas leaks; use a soap solution.
After the piping and meter have been checked
completely, purge the system of air.
DO NOT
bleed the
air inside an enclosed room.
The appliance and its individual shut-off valve must be
disconnected from the gas supply piping system during
the pressure testing of that system at test pressure in
excess of 1/2 psig or damage to the gas valve will
occur.
Gas Pressure
The ideal incoming gas pressure is 11 w.c" (minimum
6 w.c", maximum 14 w.c" or 1/2 psig). The correct
operating manifold pressure for natural gas is 3.5 w.c"
The operating manifold pressure for propane gas is 11
w.c" By adjusting the gas valve pressure regulator
between 3 and 4 w.c.i. for the NG and 6 and 11 w.c" for
the LPG, a side range can be achieved.
If the desired input rating cannot be obtained within the
above manifold pressure adjusting range, the next size
larger or smaller burner orifice should be used.
The gas pressure coming out of the regulator and going
to the burner ring has been factory set for elevations of
0 to 2000 ft. Altitudes greater than 2000 ft will require
adjustments to the gas manifold pressures. Consult
your local service dealer/dealer for high altitude adjust-
ments. In Canada, certification for installation at
altitudes over 4500 feet above sea level is the jurisdic-
tion of local authorities. You should not readjust the
burner ring gas pressure. If you replace your gas valve,
you will need to adjust the new valve. Refer to your
machine’s
specification plate
for the correct pressure
setting. Follow the installation and adjustment instruc-
tions provided with your replacement valve.
NOTE: Air for combustion and ventilation along with
exhaust flue sizing must conform to methods outlined
in current American Standard (ANSI-Z223.1) National
Fuel Gas Code or National Standard of Canada CSA-
149.1 and CSA-149.2 “Installation Code for Gas
Burning Appliances”.
Warning & Check List
1. Installation or servicing of gas
appliances and controls must
only be performed by qualified
personnel. After installation or
servicing, test manual valve,
operating valves, pressure regu-
lation, and automatic shut-off
valve for proper operation.
2. Install in a suitable dry location.
The machine must be located in an area properly
protected from the weather.
3. Shut off gas and electricity before starting installa-
tion or service. Turn back on to test or operate.
4.
DO NOT
connect appliances before pressure
testing the gas piping. Damage to gas valve may
result. (6 - 14 w.c.i. or 1/2 psig)
5.
DO NOT
insert any object other than suitable pipe
or tubing in the inlet or outlet of the gas valve.
Internal damage may occur and result in a
hazardous condition.
6.
DO NOT
grip gas valve body with a pipe wrench or
vise. Damage may result causing gas leakage.
Use inlet or outlet bosses or a special body
wrench.
7.
DO NOT
short the gas valve terminals.
8.
DO NOT
allow any flame to impinge on the
regulator vent tubing if supplied. It may clog and
cause gas valve malfunction.
9.
DO NOT
use the gas cock to adjust gas flow.
10. If main burner fails to shut off, turn off gas supply.
11. Keep all combustible materials away from gas
appliances.
DO NOT
allow lint or dust to collect in
burner area.
12. Dials must only be operated by hand. Never use
pliers, wrenches or other tools to turn dials.
13. After installation or servicing, test for leaks with a
soap solution. With the main burner on, coat pipe
and tubing joints, gaskets, etc. Bubbles indicate
leaks.
14. If the machine is installed in an enclosed room,
care should be taken to ensure that an adequate
supply of air is available for combustion and venti-
lation. (1 sq. inch per 1000 BTU)
GF 9452/9462 Operator’s Manual 8.914-365.0 - M
WARNING
READ OPERATOR’S
MANUAL THOROUGHLY
PRIOR TO USE.
OPERATIONS
SAFET
Y
MAINTENANCE
Summary of Contents for 9452
Page 2: ...2 GF 9452 9462 Operator s Manual 8 914 365 0 M Machine Data Label ...
Page 26: ...26 Notes GF 9452 9462 Operator s Manual 8 914 365 0 M ...
Page 27: ...27 Parts Parts 1 103 906 0 1 103 908 0 9452 9462 GF 9452 9462 Operator s Manual 8 914 365 0 M ...
Page 41: ...41 GF 9452 9462 Operator s Manual 8 914 365 0 M Electrical Wiring Diagram B B OR B ...
Page 42: ...8 914 365 0 Printed in U S A ...