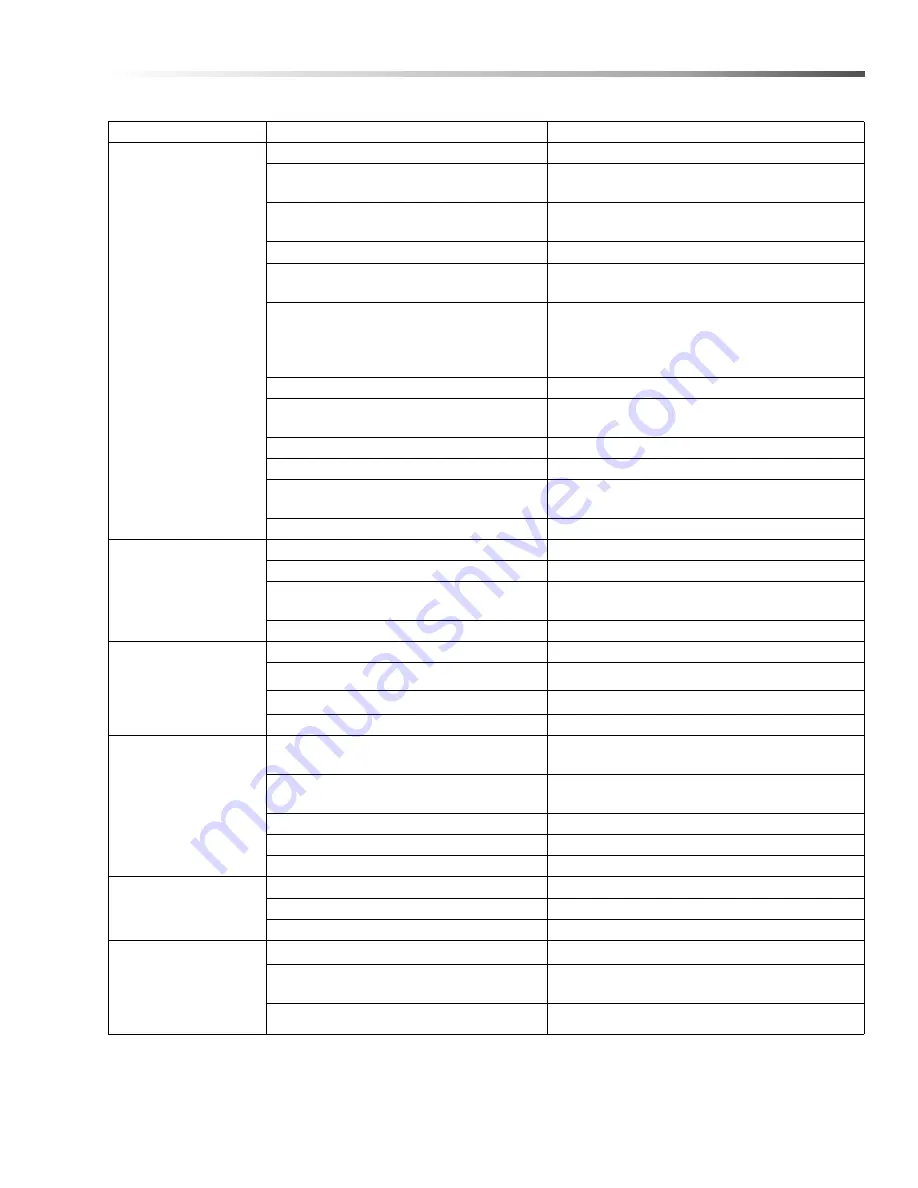
13
Maintenance
Troubleshooting Guide
PROBLEM
POSSIBLE CAUSE
SOLUTION
LOW OPERATING
PRESSURE
Faulty pressure gauge
Install new gauge.
Insufficient water supply
Use larger supply hose; clean filter at water
inlet.
Old, worn or incorrect spray nozzle
Match nozzle number to machine and/or
replace with new nozzle.
Belt slippage
Tighten or replace; use correct belt.
Plumbing or hose leak
Check plumbing system for leaks. Re-tape
leaks with teflon tape.
Faulty or mis-adjusted unloader valve
(Where applicable)
Call local dealer. Tampering with the factory
setting may cause personal injury and/ or
property damage, and will void the manufac-
turer's warranty.
Worn packing in pump
Install new packing kit.
Fouled or dirty inlet or discharge valves in
pump
Clean inlet and discharge valves.
Worn inlet or discharge valves
Replace with valve kit.
Obstruction in spray nozzle
Remove obstruction.
Leaking pressure control valve (where
applicable)
Rebuild or replace as needed.
Insufficient power supply
Check voltage.
FLUCTUATING
PRESSURE
Valves worn
Check and replace if necessary.
Blockage in valve
Check and clean out if necessary.
Pump sucking air
Check water supply and
suction line for air seepage at joints.
Worn piston packing
Check and replace if necessary.
PRESSURE LOW
AFTER PERIOD OF
NORMAL USE
Nozzle worn
Check and replace if necessary.
Inlet or discharge valves worn
Check and replace if necessary.
Inlet or discharge valves blocked
Check and clean if necessary.
Unloader valve seat worn
Check and replace if necessary.
PUMP NOISY
Air in suction line
Check water supply and connections on
suction line.
Broken or weak inlet or discharge valve
springs
Check and replace if necessary.
Foreign matter in valves
Check and clean if necessary.
Worn bearings
Check and replace if necessary.
Excessive temperature of liquid
Reduce to below 75° C (160°F).
PRESENCE OF
WATER IN PUMP OIL
Oil seal worn
Check and replace if necessary.
High humidity in air
Check and change oil twice as often.
Piston packing worn
Check and replace if necessary.
MOTOR STRAINS
UNDER LOAD
(CONTINUED
ON NEXT PAGE)
Faulty motor
Send to nearest Baldor repair center.
Incorrect spray nozzle
Install proper nozzle size (see serial plate for
proper size).
Obstruction in spray nozzle
Remove obstruction.
Hotsy 1700 Operator’s Manual 8.914-380.0 - W
Summary of Contents for 1700 Series
Page 2: ...2 Hotsy 1700 Operator s Manual 8 914 380 0 W Machine Data Label ...
Page 16: ...16 Notes Hotsy 1700 Operator s Manual 8 914 380 0 W ...
Page 17: ...17 PARTS HOTSY 1700 Parts Hotsy 1700 Operator s Manual 8 914 380 0 W ...
Page 36: ...36 Wiring Diagram 1 Models 1720 and 1722 Hotsy 1700 Operator s Manual 8 914 380 0 W ...
Page 42: ...42 Wiring Diagram 7 Models 1710 Hotsy 1700 Operator s Manual 8 914 380 0 W ...