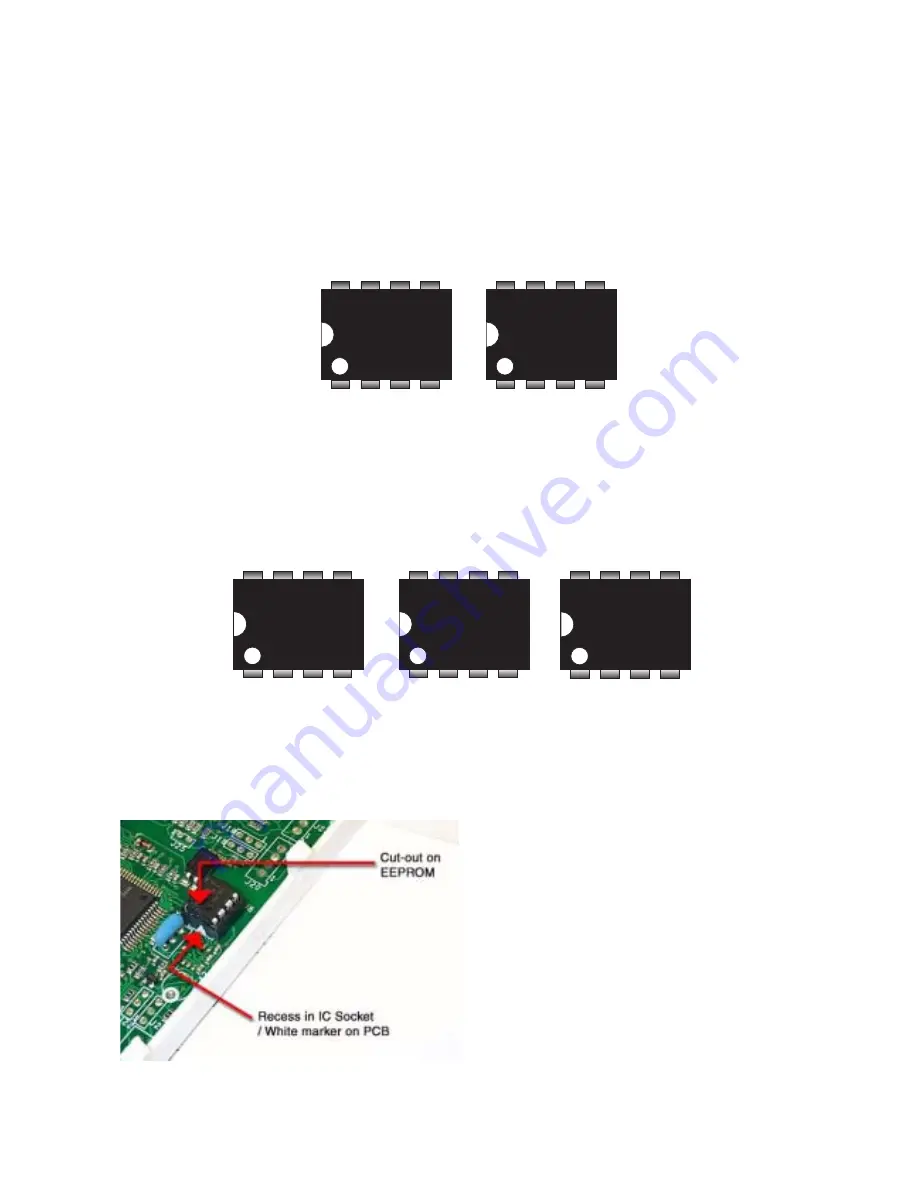
31
EEPROMS
There are two versions of Eeprom EVO1 and EVO2 and they are not interchangeable.
They match the version of software fitted on production to an appliance.
Before programming a blank Eeprom via E-mit identify the correct Eeprom before fitting to the
Power Board.
(Note: All Display Eeproms are EVO 1 and cannot be programmed via Emit.)
There are two types of EVO1 Eeprom. The original one manufactured by Fairchild, is no longer in
production. Eeproms manufactured by ST are used on current production and for spare part
requirements.
Both types have the above numbers stamped on them to identify and must not be fitted to EVO2
machines.
EVO2 Eeproms are manufactured by ST. These also have a unique identification number as shown.
These Eeproms must not be fitted to EVO1 machines.
Fitting
The correct orientation when fitting any version Eeprom is shown below:
EVO 1 (+ Display)
F B34AG
93C86AN
Fairchild
(F xxxx)
ST 93C86W6
ST
(ST xxxxx)
(Equivalent Types)
ST 24C64 6
ST 24C64W6
ST 26C64W6P
EVO 2
(Equivalent Types)