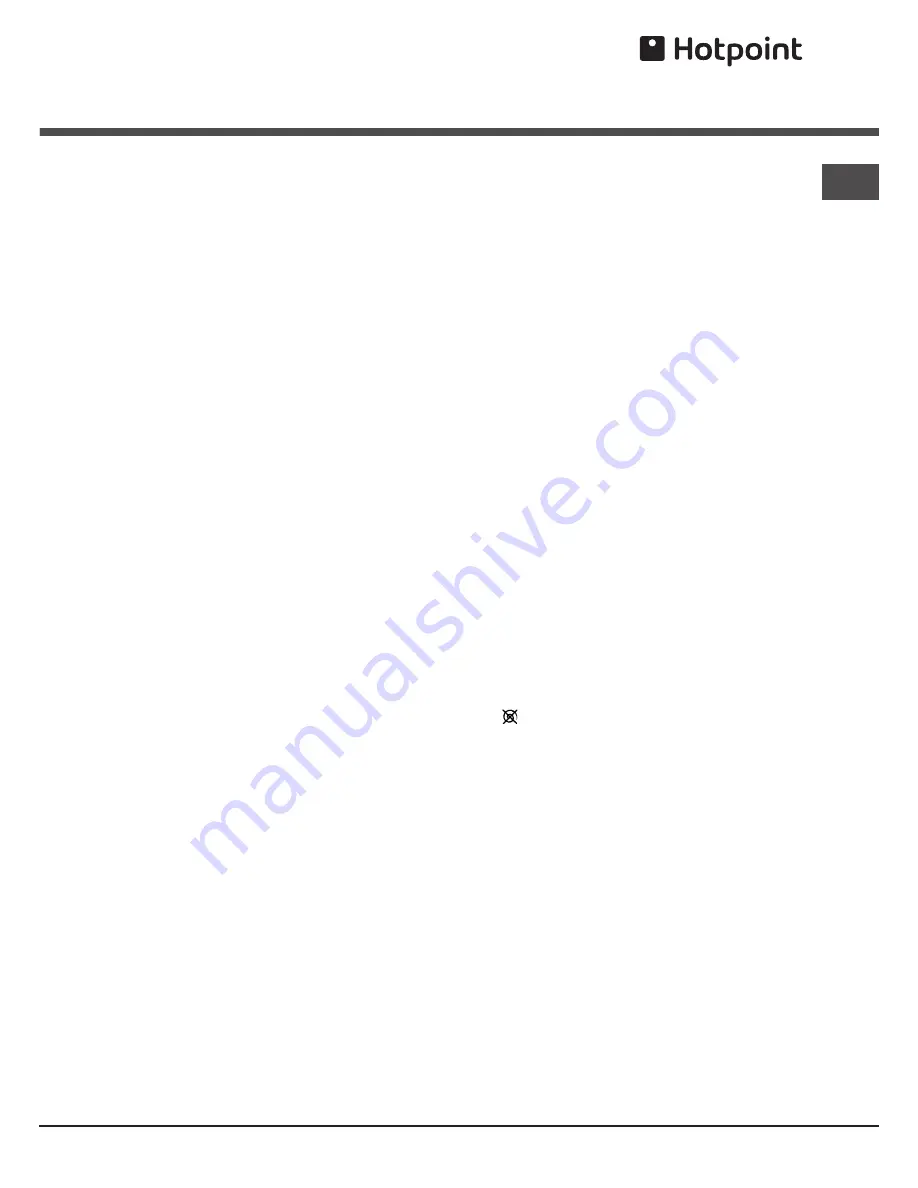
EN
13
Trouble shooting
Your washing machine could occasionally fail to work. Before contacting the Technical Assistance Centre (
see “Assistance”
),
make sure that the problem cannot be solved easily using the following list.
Problem:
The machine does not switch on.
The wash cycle does not start.
The machine does not fill with
water
or
Indicator light for the first
wash cycle flashing rapidly.
The machine continuously fills with
water and continually drains away
or Water left in the drum
or Stuck on wash.
The machine does not drain or spin
- (error lights flashing).
The machine does not spin.
The machine does not drain or spin
- ‘EASY IRON’ light flashes.
The programme takes too long.
The machine vibrates a lot during
the spin cycle.
The machine is noisy.
Possible causes / Solutions:
• The appliance is not plugged into the socket fully, or not enough to make contact.
• There is no power to the socket, or the fuse has blown in the mains plug.
• The door is not closed properly.
• The ON/OFF button has not been pressed.
• The START/PAUSE button has not been pressed.
• The water tap has not been turned on to allow water to flow into the machine.
• The ‘DELAY TIMER’ has been selected.
• The ‘CHILD LOCK’ is activated
(see ‘The machine just ‘beeps’ when a
programme or option is selected’ below).
• The water inlet hose is kinked.
• The water inlet hose is not connected to the water supply.
• The water pressure is too low.
• The water tap has not been turned on to allow water to flow into the machine.
• There is no water supply to the house.
• The inlet valve filter is blocked.
• The START/PAUSE button has not been pressed.
• The top of the drain hose is too low - It must be fitted at a height between 65
and 100 cm from the floor
(see “Installation”)
.
• The drain hose is connected incorrectly to the sink trap allowing water to run
into the machine, the drain hose must be positioned higher than the bottom of
the sink to prevent water flowing down the drain hose
.
• The end of the drain hose has been pushed too far down the standpipe, the
‘U’ bracket should be fitted 100 mm from the end of the drain hose.
• The Pump filter is blocked
.
• The drain hose is kinked
(see “Installation”).
•
New Installation -
The blanking cap or spigot has not been removed if
connected under a sink.
• The drain hose or sink trap is blocked
.
• The Spin Speed is set to “ ” position
.
• The ‘EASY IRON’ option is enabled, at the end of the program the machine drum will
rotate slowly. To complete the wash cycle press the ‘START/PAUSE’ or the ‘EASY
IRON’ buttons (
see Wash Cycles & Options).
• The ‘SILK’ program is selected, at the end of the program it requires the drain
phase to be started. To complete the program press either the ‘START/PAUSE’
or ‘EASY IRON’ buttons
(see Wash Cycles & Options).
• Programme times will vary due to water pressure, the incoming water
temperature and if the wash load goes out of balance. This will increase the
programme time accordingly (
see ‘The machine wont spin properly’ below)
- (Most Common Cause!)
• The feet have not been adjusted, enabling the machine to rock.
•
New Installation -
Either the Transit Bolts including the plastic spacers, or the
Polystyrene Packaging have not been removed when installing the machine.
• The machine is trapped between cabinets and/or walls.
• The load is in a slight out of balance condition and machine is spinning, but at
a lower speed.
• There will always be some motor, pump and drum noise during spin
.