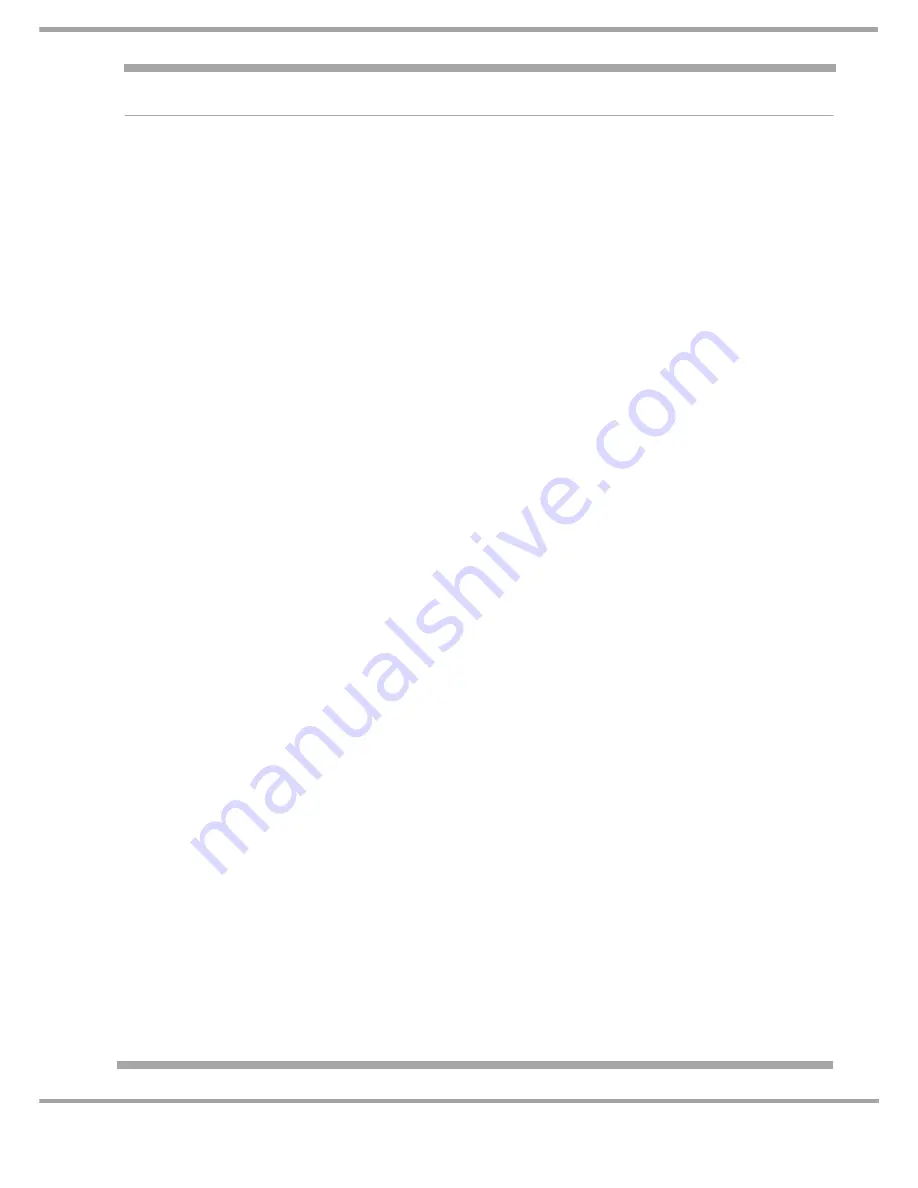
15 of 35
Indesit
Company
Service Manual UK
English
Possible Reasons for Fault Code Displayed
Note: -
Always carry out an earth insulation test before using the fault guide, as an earth fault on a
component or damaged wiring may display fault codes not related to the component signalled.
If any earth faults are found on initial testing they must be rectified before using the fault code chart,
to avoid erroneous codes being displayed.
Modern components, especially modules are very reliable, therefore edge connectors, contacts and
wiring should be thoroughly tested before trying components.
LED 1
The micro-switch in the base tray has been closed for 9 seconds to signal the alarm.
Water is leaking from components or hoses in the base of the machine.
Programme will abort and the drain pump will be energised.
LED 2
The module has detected movement of the turbine for 9 seconds when the inlet valve was not
energised.
The inlet valve is letting water by when the valve is closed.
The programme will be aborted and the drain pump is energised.
LED 1 & 2
The drain pump has been energised for 8 minutes, but the pressure switch has not
switched to the empty position (contacts 11-12).
•
Check continuity of the pump coil.
•
Check for a jammed drain pump or blockage in the outlet hose or plumbing.
•
A blocked pressure chamber or pressure switch air tube.
•
Check the pressure switch operation.
•
Check wiring to pump and module connections.
LED 1, 2 & 3
The module has detected no turbine rotation
•
Check wiring between turbine and module.
•
Check Turbine rotation
LED 1 & 3 Pressure Switch
The machine has filled with 2.5 litres of water but the pressure switch is still in the
empty position.
•
Check the filter or sump is not blocked.
•
Check the pressure switch is not stuck in the empty position (contacts 11-12) or the
pressure chamber or air tube are either blocked, unattached or split.
•
Check the wash pump is circulating the water.
•
Check the wiring to the pressure switch.
•
Check the edge connector blocks on the pressure switch and module card.
•
Check the outlet hose is not too low causing the machine to siphon.
•
Aborts the cycle and energises the drain pump.
LED 1 & 4
Module recognition error.
•
Check edge connections and wiring.
•
Reprogramme the EEPROM file.
•
Replace module or display as required.
LED 2 & 3
Time out for filling.
(The WASH LED will flash as a warning before the fault code is displayed.)
The module has not detected turbine rotation with the inlet valve energised.
•
Check the taps are turned on and that the fill hoses are not kinked.