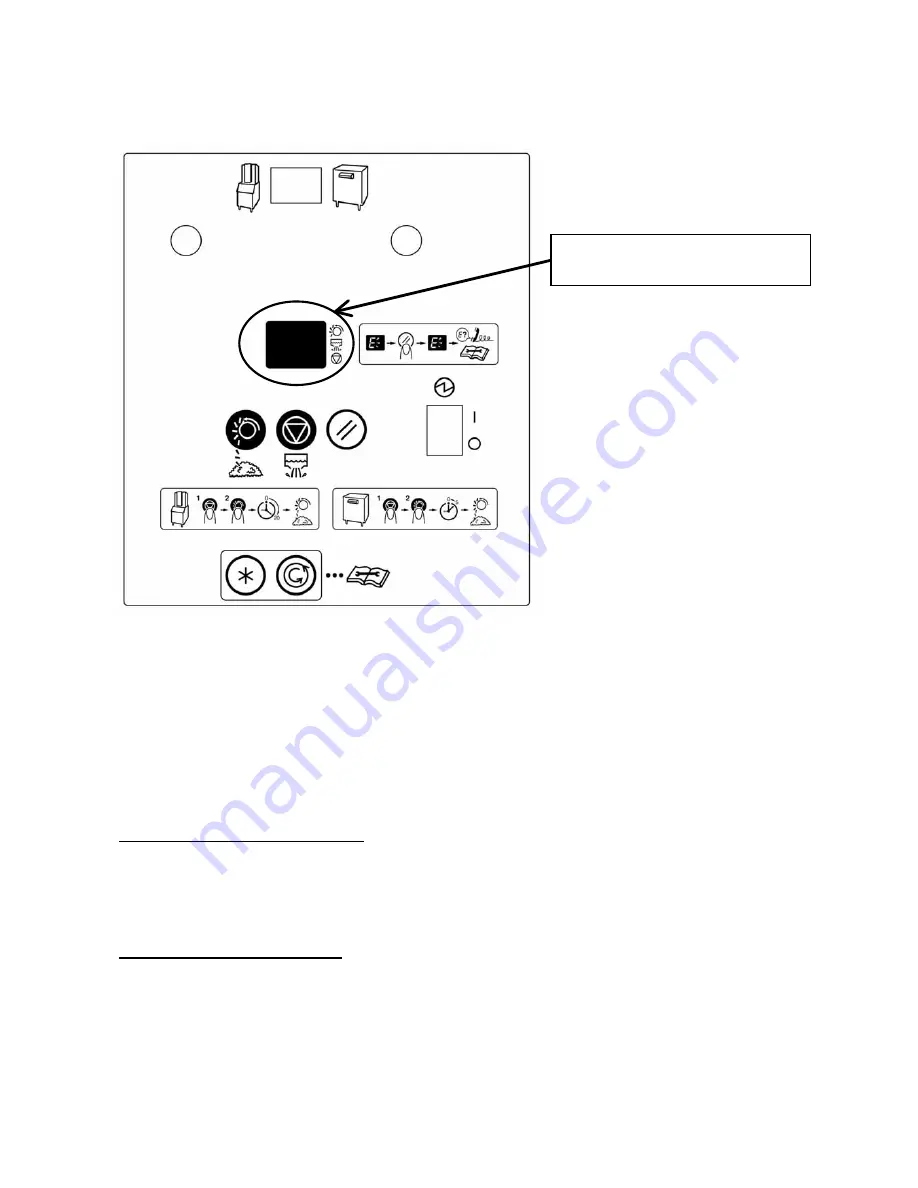
37
When an error occurs, “E_” or ”c_”
will appear in the Display Window.
8. PROTECTORS
[a] INDICATION
When an operational error occurs, “E_” or “C_” will appear and blink in the Display Window
on the Operation Board, and the icemaker will stop. When a service call is received, ask
the user to check which error code is in the Display Window. Then, see the error code
table in “9. ERROR CODES” to locate the cause.
[b] PROTECTORS
1) Compressor
Internal Inherent Motor Protector
Senses a temperature rise of the Compressor, and internally shuts off the circuit.
Automatically resets when the temperature goes down. If the Compressor takes a long
time to restart, the Ice Production Timer may shut down the unit with “E1” in the Display
Window. In this case, press the Reset Button.
Internal Pressure Relief Valve
Allows discharge gas into the low side to prevent damage to the Compressor when the
discharge pressure rises excessively. The bypassed gas will trip the above-mentioned
Internal Inherent Motor Protector which will not reset until the temperature goes down.
Summary of Contents for TM-500AAE
Page 4: ...iii 8 FLUSH WATER VALVE 59 9 CONTROLLER BOARD 60 10 LINE VALVE 60...
Page 7: ...3 2 DIMENSIONS CONNECTIONS...
Page 13: ...9 2 WIRING DIAGRAM a WIRING DIAGRAM...
Page 14: ...10 b CONTROL BOX LAYOUT...
Page 24: ...20 d SEQUENCE 1 Startup Water Supply Floor Mounting...
Page 25: ...21 1 Startup Water Supply Fixed Mounting...
Page 28: ...24 3 Startup After Fan Motor and Line Valve start Compressor starts in 15 sec Floor Mounting...
Page 29: ...25 3 Startup After Fan Motor and Line Valve start Compressor starts in 15 sec Fixed Mounting...
Page 30: ...26 4 Startup Ice production starts Floor Mounting...
Page 31: ...27 4 Startup Ice production starts Fixed Mounting...
Page 32: ...28 5 Normal Operation Bin control and drain cycle 480 sec start Fixed Mounting...
Page 35: ...31 7 Shutdown Drain Floor Mounting...
Page 36: ...32 7 Shutdown Drain Fixed Mounting...
Page 57: ...53 Fig 1 Fig 2 Fig 3...