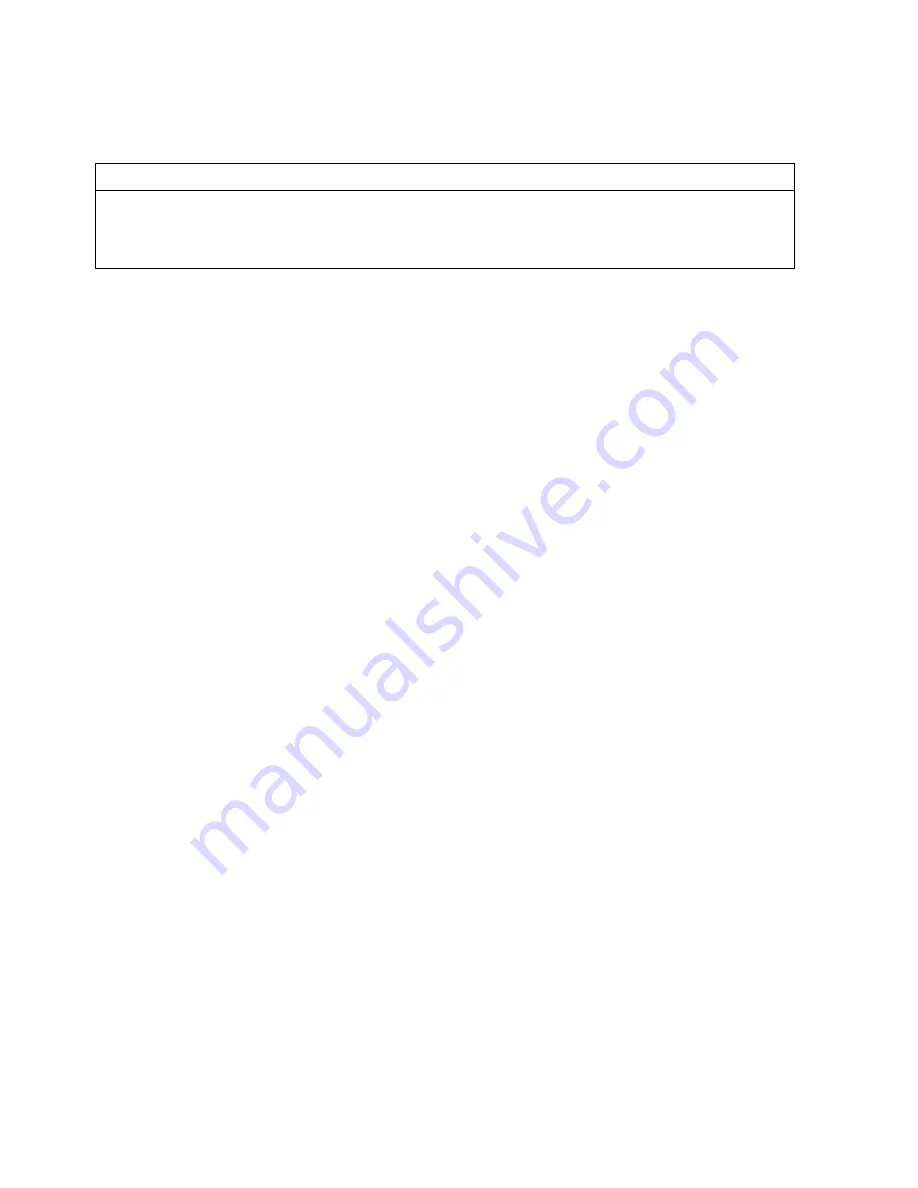
23
3. Evacuation
1) Attach a vacuum pump to the system. Be sure to connect the charging hoses to both
high and low-side refrigerant piercing valves.
IMPORTANT
The vacuum level and vacuum pump may be the same as those for current
refrigerants. However, the rubber hose and gauge manifold to be used for
evacuation and refrigerant charge should be exclusively for POE oils.
2) Turn on the vacuum pump, then open the gauge manifold valves. Never allow the oil in
the vacuum pump to flow backwards.
3) Allow the vacuum pump to pull down to a 29.9" Hg vacuum (500 microns). Evacuating
period depends on pump capacity.
4) Close the low-side valve and high-side valve on the gauge manifold.
5) Disconnect the gauge manifold hose from the vacuum pump and attach it to a
refrigerant service cylinder. Remember to loosen the connection and purge the air from
the hose. For the required refrigerant charge, see the nameplate. We recommend only
virgin or reclaimed refrigerant which meets ARI Standard 700 (latest edition) be used.
4. Recharge
6) R-290 can be charged in either the liquid or vapor state. A liquid charge is preferred.
Connect the refrigerant hose to the service cylinder and bleed air out of refrigerant
hose. Next, invert the service cylinder and place it on the scales. Zero out the scales.
Open the high-side valve on the gauge manifold.
7) Allow the system to charge with liquid until the proper charge weight is met.
8) Close the high-side valve on the gauge manifold. If charging is complete, skip to step 10.
9) If necessary, add any remaining charge to the system through the low-side.
NOTICE!
To prevent compressor damage, use a throttling valve or liquid
dispensing device to add the remaining liquid charge through the low-side
refrigerant access valve with the compressor running.
Close the refrigerant
cylinder valve and let the low-side refrigerant equalize to the system, then close the
low-side manifold gauge. Unplug the appliance from the electrical outlet.
10) Remove the refrigerant hose from the service cylinder. Pinch off (crimp down) the
process tubes just below the piercing valves.
11) Remove the piercing valves. Cut the process tubes to remove the piercing valve holes
then braze the process tubes closed. Note: Be sure there is no refrigerant leak or
refrigerant in the area before brazing.
12) Use a combustible gas leak detector or soap bubbles to check for leaks again.
13) Place red sleeves over the process tubes.
14) Plug the appliance back into the electrical outlet. Allow the appliance to cool to setpoint
before reloading.
Summary of Contents for EF1A-FS
Page 1: ...FREEZER Service Manual ER1A FS ER2A FS EF1A FS EF2A FS Issued 07 26 2019 Revised 07 14 2020...
Page 28: ...28 Model Run Capacitor Starting Capacitor ER1A FS 15 F 250 V 250 F 160 V B Wiring Diagram...
Page 29: ...29 Model Run Capacitor Starting Capacitor EF1A FS 10 F 250 V 150 F 160 V...
Page 30: ...30 Model Run Capacitor Starting Capacitor ER2A FS 15 F 250 V 250 F 160 V...
Page 31: ...31 Model Run Capacitor Starting Capacitor EF2A FS 30 F 250 V 200 F 160 V...