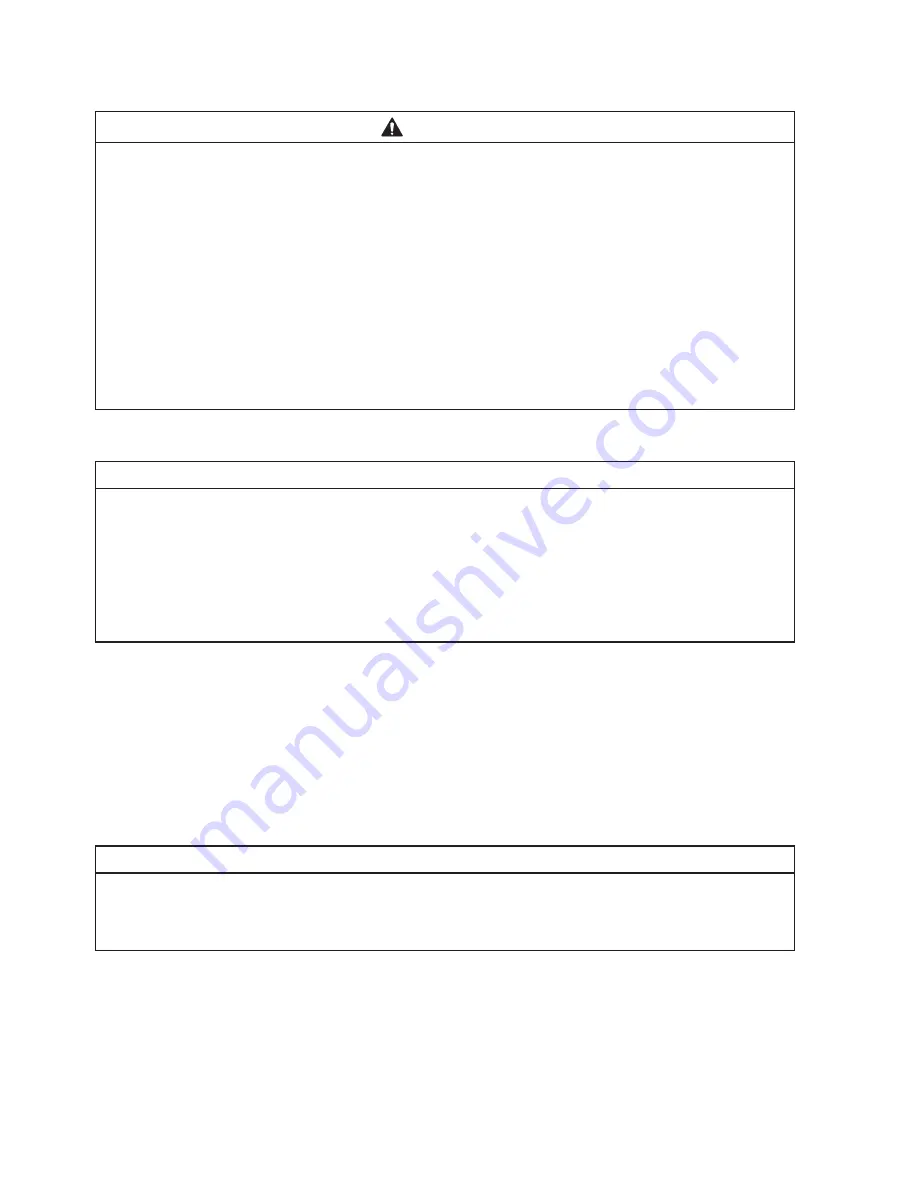
40
2. Brazing
WARNING
• R-134a and R-404A themselves are not flammable at atmospheric pressure and
temperatures up to 176°F (80°C).
• R-134a and R-404A themselves are not explosive or poisonous. However,
when exposed to high temperatures (open flames), R-134a and R-404A can be
decomposed to form hydrofluoric acid and carbonyl fluoride both of which are
hazardous.
• Do not use silver alloy or copper alloy containing arsenic.
• Use an electronic leak detector or soap bubbles to check for leaks. Add a trace
of refrigerant to the system (if using an electronic leak detector), and then raise
the pressure using nitrogen gas (140PSIG). DO NOT use R-134a or R-404A as a
mixture with pressurized air for leak testing.
1) Braze all fittings while purging with nitrogen gas flowing at a pressure of 3 to 4 PSIG.
NOTICE
• Always install a new drier every time the sealed refrigeration system is opened.
• Do not replace the drier until after all other repair or replacement has been made.
Install the new drier with the arrow on the drier in the direction of the refrigerant
flow.
• When brazing, protect the drier by using a wet cloth to prevent the drier from
overheating. Do not allow the drier to exceed 250°F (121°C).
2) Use an electronic leak detector or soap bubbles to check for leaks. Add a trace of
refrigerant to the system (if using an electronic leak detector), and then raise the
pressure using nitrogen gas (140 PSIG). DO NOT use R-134a or R-404A as a mixture
with pressurized air for leak testing.
3. Evacuation and Recharge
1) Attach a vacuum pump to the system. Be sure the charging hoses are connected to both
high and low-side access valves.
IMPORTANT
The vacuum level and vacuum pump may be the same as those for current
refrigerants. However, the rubber hose and gauge manifold to be used for
evacuation and refrigerant charge should be exclusively for POE oils.
2) Turn on the vacuum pump. Open the gauge manifold valves. Never allow the oil in the
vacuum pump to flow backwards.
3) Allow the vacuum pump to pull down to a 29.9" Hg vacuum. Evacuating period depends
on pump capacity.
4) Close the low-side valve and high-side valve on the gauge manifold.
Summary of Contents for AMERICA 73183
Page 22: ...22 B Wiring Diagrams 1 CR1B FG High Pressure Switch Cut out 270 10 PSIG Cut in 190 20 PSIG...
Page 23: ...23 High Pressure Switch Cut out 270 10 PSIG Cut in 190 20 PSIG 2 CR1B FS HS CR3B FS HS...
Page 24: ...24 3 CR2B FG High Pressure Switch Cut out 270 10 PSIG Cut in 190 20 PSIG...
Page 25: ...25 4 CR2B FS HS CR3B FS HS High Pressure Switch Cut out 270 10 PSIG Cut in 190 20 PSIG...