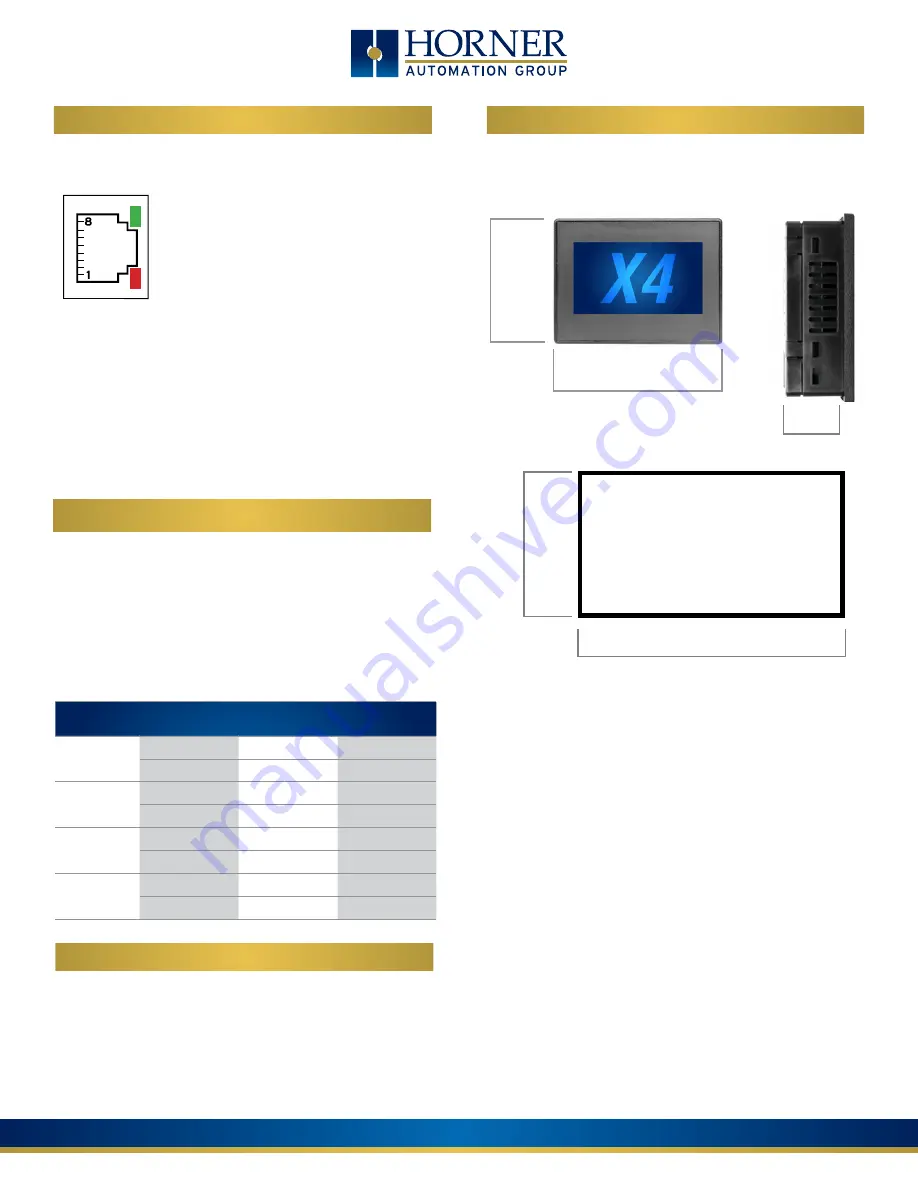
MAN1138-03-EN
-EU
Unit 1 Centrepoint, Centre Park Road, Cork, T12 H24E, Ireland. | (p) +353 21 4321 266 (f) +353 021 4321 826 | www.horner-apg.com
g.com
g.com
g.com
g.com
g.com
g.com
Please visit our website for a complete listing and to learn more about certified Horner Automation products.
This document is the property of Horner Automation Group, and is subject to change.
page 6 of 7
5.1 - Built-in I/O (Model R & Model A)
Both X4 models feature built-in I/O. The I/O is mapped into OCS
Register space, in three separate areas – Digital/Analog I/O, High-Speed
Counter I/O, and High-speed Output I/O. Digital and analog I/O location
is fixed starting at 1, but the high-speed counter and high-speed output
references may be mapped to any open register location. For more
details on using the high-speed counter and high-speed outputs, see
the X4 OCS User’s Manual (MAN1137).
5 BUILT-IN I/O
FIXED
ADDRESS
DIGITAL/ANALOG
I/O FUNCTION
MODEL R
MODEL A
%I
Digital Inputs
1-12
1-12
Reserved
13-32
13-32
%Q
Digital Outputs
1-6
1-12
Reserved
7-16
13-16
%AI
Analog Inputs
1-4
1-4
Reserved
5-12
5-12
%AQ
Analog Outputs
1-2
1-2
Reserved
3-6
3-6
6 BATTERY
The X4 uses a replaceable non-rechargeable 3V lithium coin-cell
battery (CR2450) to run the Real-Time Clock and to maintain the
retained register values. This battery is designed to maintain the clock
and memory for 7-10 years. Please reference MAN1137 for instructions
on how to replace the battery.
7 DIMENSIONS & INSTALLATION
4.92” (125mm)
3.79”
(96mm)
1.22” (31mm)
Panel Cutout
3.58”
(91mm)
4.675” (118.75mm)
7.2 - Installation Procedure
The X4 utilizes a clip installation method to ensure a robust and
watertight seal to the enclosure. Please follow the steps below for the
proper installation and operation of the unit.
1.
Carefully locate an appropriate place to mount the X4. Be sure to
leave enough room at the top of the unit for insertion and removal
of the microSD™ card.
2.
Carefully cut the host panel per the diagram on Page 1, creating a
91mm x 118.75mm +/-0.1mm opening into which the X4 is to be
installed. If the opening is too large, water may leak into the
enclosure, potentially damaging the unit. If the opening is too small,
the OCS may not fit through the hole without damage.
3.
Remove any burrs/sharp edges and ensure the panel is not warped in
the cutting process.
4.
Install and tighten the four mounting clips (provided in the box)
until the gasket forms a tight seal. For standard composite mounting clips
(included with product), use a torque rating of 2-3 in-lbs (0.23-0.34
Nm). For optional metal mounting clips, use a torque rating of 4-8
in-lbs (0.45-0.90 Nm).
5.
Connect communications cables to the serial port, USB ports, and
CAN port as required.
4.3 - Ethernet Communications
Link
Indicator
Activity
Indicator
10/100 Ethernet port with automatic MDI-X (crossover detection)
is provided via the single 8-position modular jack lableled “LAN”.
Several features are available for use over Ethernet, such as WebMI,
Modbus TCP/IP, Ethernet/IP, SMTP (E-mail), and more.
Ethernet configuration is done via the Cscape Hardware
Configuration, though temporary Ethernet configuration may be done
through the System Menu directly on the X4.
For more information on the Ethernet, available features and
protocols, refer to the Ethernet Supplement document (SUP0740).
communications continued...
6.1 - Battery Maintenance
7.1 - X4 Dimensions