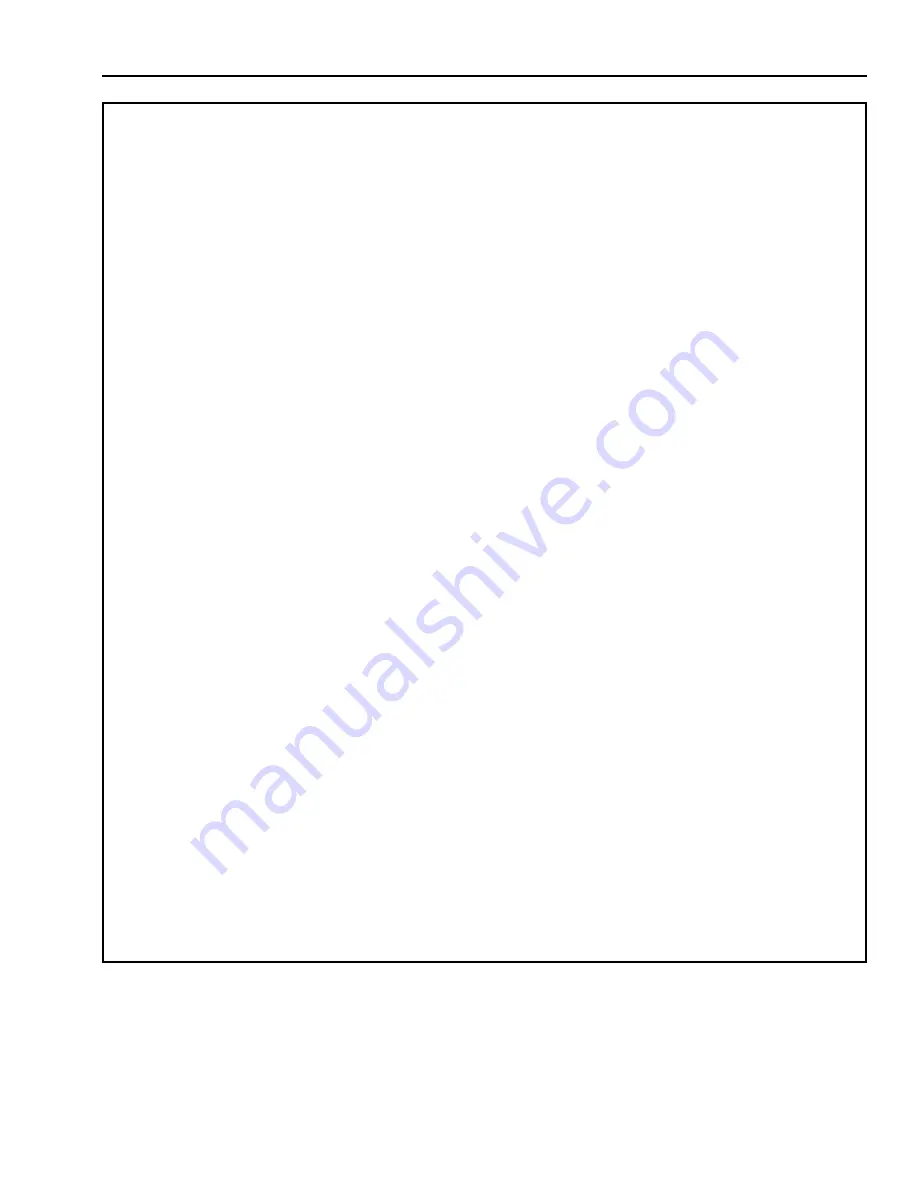
Y8610U INTERMITTENT PILOT RETROFIT KIT
68-0133—2
19
ANSI STANDARDS
Exhibit A
Recommended Procedure for Safety Inspection of an Existing Appliance Installation as a Preliminary Step
to Applying an Automatic Intermittent Pilot System
The following procedure is intended as a guide to aid in determining that an appliance is properly installed and is in a safe
condition for continuing use.
This procedure is predicated on central furnace and boiler installations equipped with an atmospheric gas burner(s) and not
of the direct vent type. It should be recognized that generalized test procedures cannot anticipate all situations. Accordingly,
in some cases, deviation from this procedure may be necessary to determine safe operation of the equipment.
a.
This procedure should be performed prior to any attempt at modification of the appliance or the installation.
b.
If it is determined there is a condition which could result in unsafe operation, the appliance should be shut off and the
owner advised of the unsafe condition.
The following steps should be followed in making the safety inspection:
1. Conduct a Gas Leakage Test of the appliance piping and control system downstream of the shut-off valve in the supply
line to the appliance.
2. Visually inspect the venting system for proper size and horizontal pitch and determine there is no blockage or
restrictions, leakage or corrosion or other deficiencies which could cause an unsafe condition.
3. Shut off all gas to the appliance and shut off any other fuel-burning appliance within the same room. Use the shutoff
valve in the supply line to each appliance. If a manual gas valve is not in the gas supply line within 6 feet of the
appliance in an accessible location, one shall be installed.
4. Inspect burners and crossovers for blockage and corrosion.
5. Applicable only to warm air heating appliances. Inspect heat exchangers for cracks, openings or excessive corrosion.
6. Applicable only to boilers. Inspect for evidence of water or combustion product leaks.
7. Insofar as is practical, close all building doors and windows and all doors between the space in which the appliance is
located and other spaces of the building. Turn on clothes dryers. Turn on any exhaust fans, such as range hoods and
bathroom exhausts, so they will operate at maximum speed. Do not operate a summer exhaust fan. Close fireplace
dampers. If, after completing steps 7 through 12, it is believed sufficient combustion air is not available, refer to 1.3.4 of
the National Fuel Gas Code (Z223.1) for guidance.
8. Place in operation the appliance being inspected. Follow the lighting instructions. Adjust thermostat so appliance will
operate continuously.
9.
a.
Determine that the pilot is burning properly and that main burner ignition is satisfactory by interrupting and re-
establishing the electrical supply to the appliance in any convenient manner.
b.
Determine manifold pressure in order to match input after the new control is installed.
10.
a.
Visually determine that main burner gas is burning properly; i.e., no floating, lifting or flashback. Adjust the
primary air shutter(s) as required.
b. If appliance is equipped with high and low flame control or flame modulation, check for proper main burner operation at
low flame.
11. Test for spillage at the draft hood relief opening after 5 minutes of main burner operation. Use a draft gauge, the flame
of a match or candle, or smoke from a cigarette, cigar or pipe.
12. Return doors, windows, exhaust fans, fireplace dampers and all other fuel-burning appliances to their previous
conditions of use.
13. Applicable only to warm air heating appliances. Check both limit controller and fan controller for proper operation. Limit
controller operation can be checked by temporarily disconnecting the electrical supply to the blower motor and
determining that the limit control acts to shut off the main burner gas.
14. Applicable only to boilers:
a.
Determine that the circulating water pumps are in operating condition.
b.
Test low water cutoffs, automatic feed controls, pressure and temperature limit controls and relief valves in
accordance with the manufacturer’s recommendations and instructions to determine they are in operating
condition.
Exhibit A of ANSI Standard Z21.71 for Automatic Intermittent Pilot Ignition Systems for Field Installation.