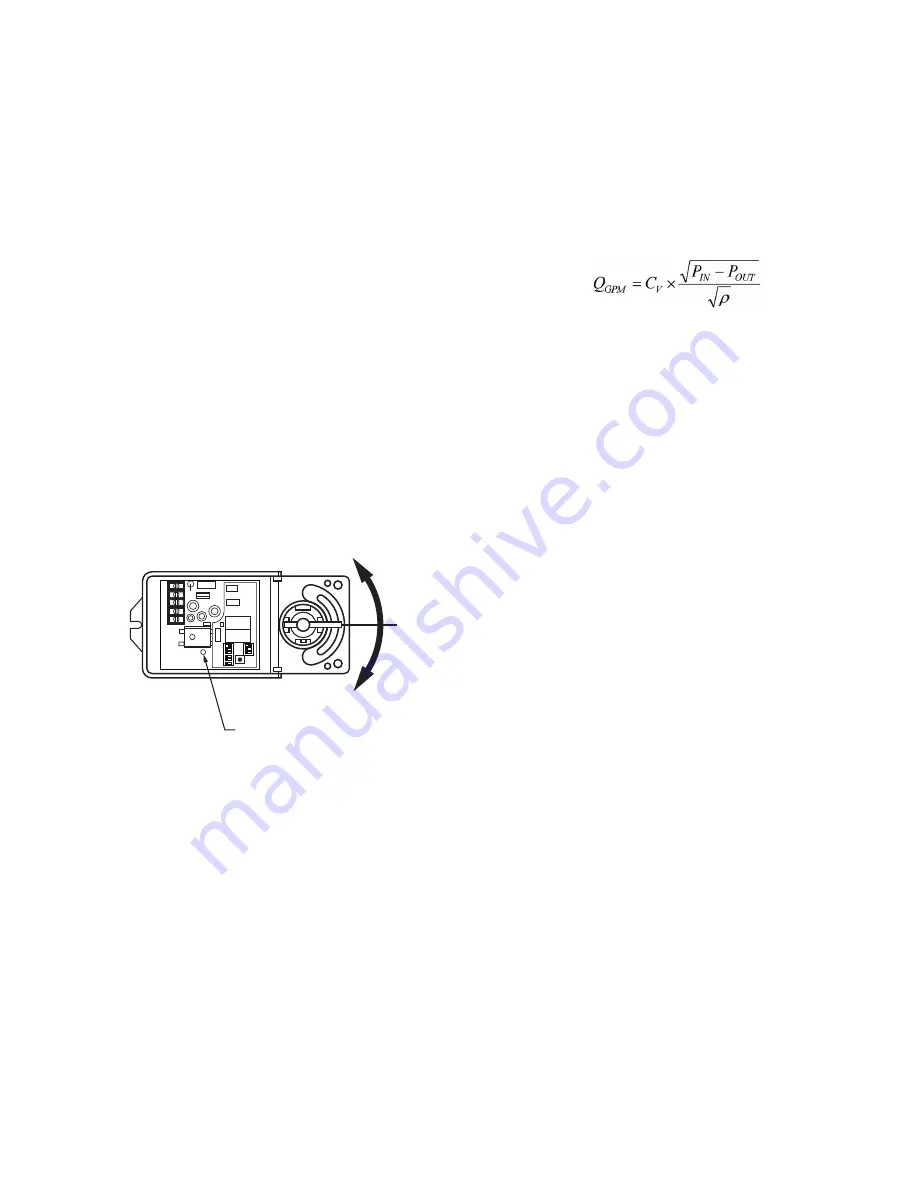
VRW2 DYNAMIC PRESSURE- REGULATING FLANGED CONTROL VALVES
9
62-3116—01
OPERATION AND CHECKOUT
Once both the mechanical and electrical installations are
complete:
1.
Cycle the actuator to verify that the direction of rotation
suits the control sequence.
2.
If the rotation direction is incorrect:
a. For floating control actuators: Reverse two control
signal wires (CW/CCW), or change position of selec-
tor switches.
b. For analog control actuators, change position of
selector switches.
3.
If the control scheme requires fail-safe operation, ensure
that, upon removal of power, the fail position coincides
with the control sequence.
Manual Override
1.
Remove Actuator cover and DISCONNECT POWER
before operating actuator manually.
NOTE: Failure to disconnect power may cause dam-
age to the actuator gears.
2.
Press the clutch.
3.
Rotate valve stem to manually operate valve. Clockwise
to close, Counter-Clockwise to open. See Fig. 11.
Fig. 11. Manual Operation.
MAINTENANCE
1.
Continual blinking indicates that the Actuator torque out-
put limit has been exceeded. This may have been
caused by debris in the valve internals. Disconnect
power and manually operate the valve to clear the
debris. Reconnect power. The Actuator will automatically
recalibrate and reset. If the problem reoccurs, inspect
the valve body internally for debris.
2.
If the system experiences large amounts of pipe scale
due to poor water conditions, as sometimes found in
older or retrofit pipe systems, provisions should be made
to keep the system clean. Proper water treatment is also
recommended by the use of a Separator.
3.
If a separator is not used for system cleaning and filtra-
tion, the valves should be checked annually.
Operation
The differential pressure regulator maintains constant pressure
drop (P
IN
- P
OUT
) across the valve seat through a wide range
of head pressures. At a given shaft position, flow through the
valve will constant as defined by the formula:
where
ρ
is the density of the glycol mix.
P
IN
changes constantly in a multi-zone system as other valves
open and close, changing system flow and head pressure
according to the characteristics of the supply pump curve.
Reaction of the mechanical pressure regulator is
instantaneous, eliminating changes in room temperature due
to changes in fluid flow, and reducing the need for the control
system to constantly operate the control portion of the valve to
correct for the non-load related temperature changes that
occur in a system with standard control valves.
At full flow in a 2-position control application, a VRW2 behaves
as a flow limiter.
The pressure regulator takes a minimum pressure to operate,
and has a maximum differential regulation capability. The
pressure drop across a VRW Valve is comparable to the
pressure drop across a control valve plus a balancing valve in
a conventional system design.
SETTINGS AND ADJUSTMENTS
At the full open position, VRW valves will maintain flow at the
gallons per minute rate determined by the DIP Switch settings
shown in Table 4. Under steady state operation, the control
system will only require the valve to open enough to satisfy
load conditions. During morning recovery from night setback,
the controller will usually command the valve to 100%.
Coil flow can be confirmed by reading pressures at the supply
inlet and return outlet, and using the system design data to
calculate flow.
Note that the pressure regulator in this valve guarantees that
the flow through the valve will not be affected by upstream
changes in pressure. Unlike conventional balancing valves, it
is not necessary to reconfirm flow after adjusting other valves.
Any overflow during morning recovery due to oversized
pressure regulated valves will not affect other valves in the
system, provided pumps are capable of required flow.
M31293
CLOSE
OPEN
CLUTCH PUSH BUTTON
1
ON
23
4
5
6
1
ON
23
1 2 3 4 5
88