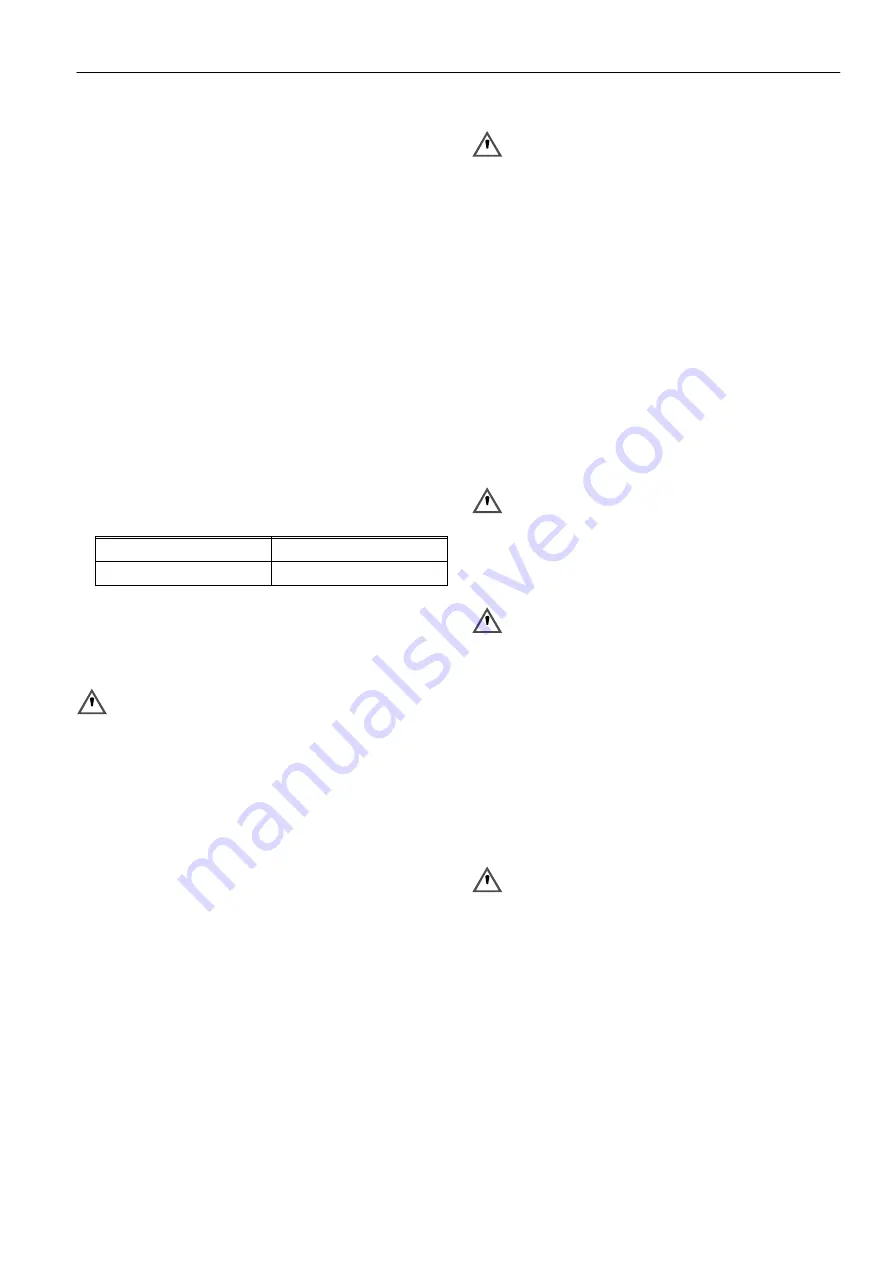
EN1R--9170 0109R1--NE
3
INSTALLATION
IMPORTANT
Take care that installer is a trained experienced ser-
vice person.
Turn off gas supply before starting installation.
Disconnect power supply to prevent electrical shock
and/or equipment damage.
Do not remove seals over inlet and outlet until the
device is ready to be installed.
If M5 air pressure connection is not to be used, it is
recommanded to push a dust cap into the hole
(order nr. 45.900.426--001).
Mounting position
The gas control can be mounted 0 to 90
_
in any direction from
the upright position, i.e. from the position when electric
operators are on top.
Main gas connection
·
Take care that dirt cannot enter the gas control during
handling.
·
Use a clean taper fitting with thread according to ISO 7--1
or a piece of new, properly reamed pipe, free from swarf.
·
Do not tighten the pipe or pipe fitting too far (see table
below). Otherwise valve distortion and malfunction could
result.
Pipe size
Max. length of pipe thread
1
/
2
”
18.6 mm
·
Apply a moderate amount of good quality thread
compound to the pipe or fitting only, leaving the two end
threads bare. PTFE tape may be used as an alternative.
·
Ensure that gas flows in the same direction as the arrow
on the bottom of the gas control.
Electrical connection
CAUTION
Switch off power supply before making electrical con-
nections.
Take care that wiring is in accordance with applicable
codes and local regulations.
Ensure that cut--off function of limit control de--en-
ergizes both valves.
Use lead wire which can withstand 105
_
C ambient.
Use lead wire which is proven against moisture.
The electric on/off operator is provided with:
6.3 mm quick connect terminals suitable for 6.3 mm
receptacles (e.g. ”Series 250” AMP fasteners) and special
plugs.
The electric servo on/off operator/regulator is provided with:
quick connect terminals suitable for a female connector
according to DIN 43650 and special plugs.
Wiring gas control in intermittent ignition (IP) system
The appliance manufacturer’s instructions should always be
followed.
Perform gas leak test
WARNING
FIRE OR EXPLOSION HAZARD CAN CAUSE
PROPERTY DAMAGE, SEVERE INJURY OR
DEADTH
Check for gas leaks with a rich soap and water solu-
tion any time work is done on a gas control.
Gas leak test
·
Paint all pipe connections upstream of the gas control with
with a rich soap and water solution. Bubbles indicate a gas
leak.
·
If a gas leak is detected, tighten the pipe connection.
·
Stand clear while lighting the main burner to prevent injury
caused from hidden gas leaks, which could cause flasback
in the appliance vestibule. Light the main burner.
·
With the main burner in operation, paint all pipe joints
(including adapters) and gas control inlet and outlet with
with a rich soap and water solution or an approved leak
detection fluid.
·
If another gas leak is detected, tighten adapter screws,
joints and pipe connections.
·
Replace the part if gas leak can not be stopped.
CAUTION
Keep soap and water solution away from electrical
connections.
ADJUSTMENTS
WARNING
Adjustments must be made by qualified persons only.
If the appliance manufacturer supplies checkout and/
or service and maintenance instructions carefully fol-
low them.
If such instructions are not provided then use the pro-
cedure outlined below.
Adjustment can only be made with a special tool.
Pressure tap
The gas control is provided with a pressure tap of 9 mm O.D.
at inlet and outlet side.
When checking the pressure undo the screw a half turn and
slip tube over nipple.
Ensure that screw is retightened after making test.
CAUTION
To ensure a safe closing of the valves, it is essential
that voltage over the terminals of electric operators is
reduced to 0 Volt.
Offset adjustment throttle valve versions on modulating applications
(see fig. 1.)
·
Remove cap screw with a screw driver to expose offset
adjustment screw.
·
Check gas supply pressure to the appliance using a
pressure gauge connected to the inlet pressure tap.
·
Start fan and check air flow.
·
Energize both electric operators in order to have gas input
to burner and ignite boiler.