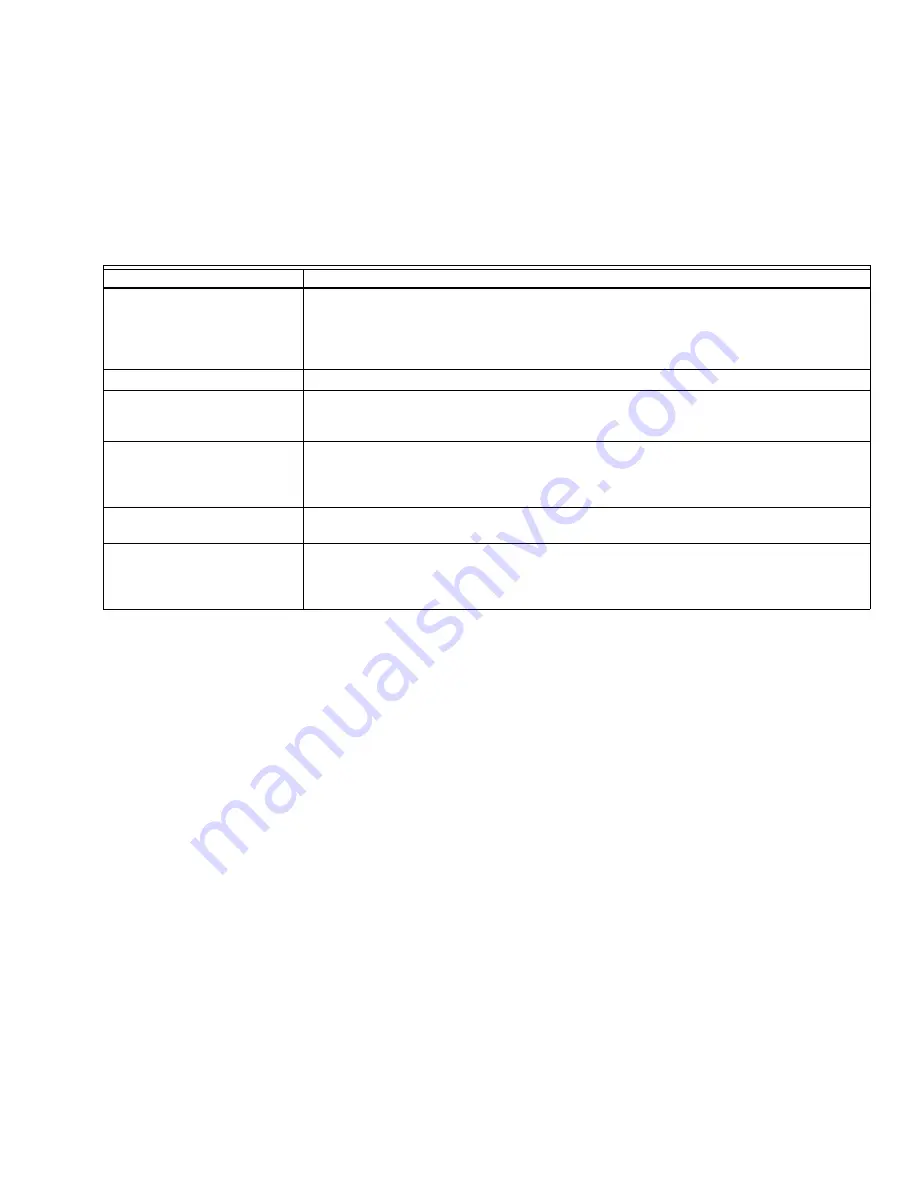
VGF FLANGED GLOBE VALVES
19
63-2618—01
CHECKOUT AND TROUBLESHOOTING
Actuators
NOTE:
For valve actuator operation instructions, see the
Product Data sheet for the specific actuator.
1.
Operate the control system and check valve opera-
tion to ensure the valve stem can position the valve
smoothly through full stroke without binding.
2.
Verify that the actuator fully closes the A port.
3.
Perform the checkout tests included with the actua-
tor instructions.
Table 10. VGF Valve Checkout and Troubleshooting.
TYPICAL SPECIFICATIONS
Valve housing shall consist of cast iron and shall be ANSI-
rated to withstand the pressures and temperatures
encountered. Automatic control valves shall have flanged
fittings, 2-1/2 in. through 6 in. size.
Valves shall have stainless steel plugs, seats, and stems,
and be constructed with replaceable spring-loaded
reinforced carbon-filled Teflon packing.
Straight through and diverting valves shall have a
maximum seat leakage rate of 0.05% Cv at the control
port and shall have 50:1 rangeability or better. Pressure-
balanced valves shall have a maximum seat leakage rate
of 0.01% at 175 psi differential pressure.
All valves shall be provided with either linear or equal
percentage contoured throttling plugs for water, glycol-
water, or steam service. Three-way valves shall be
available in either mixing or diverting configurations.
Valves shall be manufactured by the same company that
manufactures the direct coupled linear valve actuators or
linkages and rotary actuators.
Topic
Information
Valve does not move freely
•
Possible cause: Contamination. Over time, scale, rust, magnetite, sand, and silt can cause wear of valve components.
•
The presence of suspended rust in a hydronic system voids most industry warranties.
•
Appropriate system flushing, filtration, and chemical treatment are required to maintain proper operating
conditions.
•
Boiler and chiller manufacturers publish water quality guidelines. Specific conditioning regimens depend on system.
Valve Leak-by
•
Damage to the plug or seat caused by particulate, wire draw, or steam corrosion requires valve replacement.
Valve stem leaks
•
Replace the stem packing using the matching repacking kit. (See the Specifications section for the proper
accessory.)
•
If the valve stem is bent, the valve must be replaced.
Improper Control
•
Pressure drop across the valve must be at least as great as the pressure drop across the controlled load. If not, valve
authority and control span are reduced.
•
If necessary, use pipe transitions in order to use a valve body with the proper Cv rating. Transition should be installed
approximately 6 pipe diameters from valve.
Noisy Valve
•
Limit differential pressure across valve seats to 20 psi.
•
This recommendation is independent of published close-off ratings.
Actuator Failure in Steam Applications
•
Take care not to exceed valve temperature ratings. This can result in damage not covered by the Honeywell limited
warranty.
•
To protect actuators from excess heat, orient the valve so the actuator is not directly over the piping, and/or use a
43196000 High Temperature Kit.