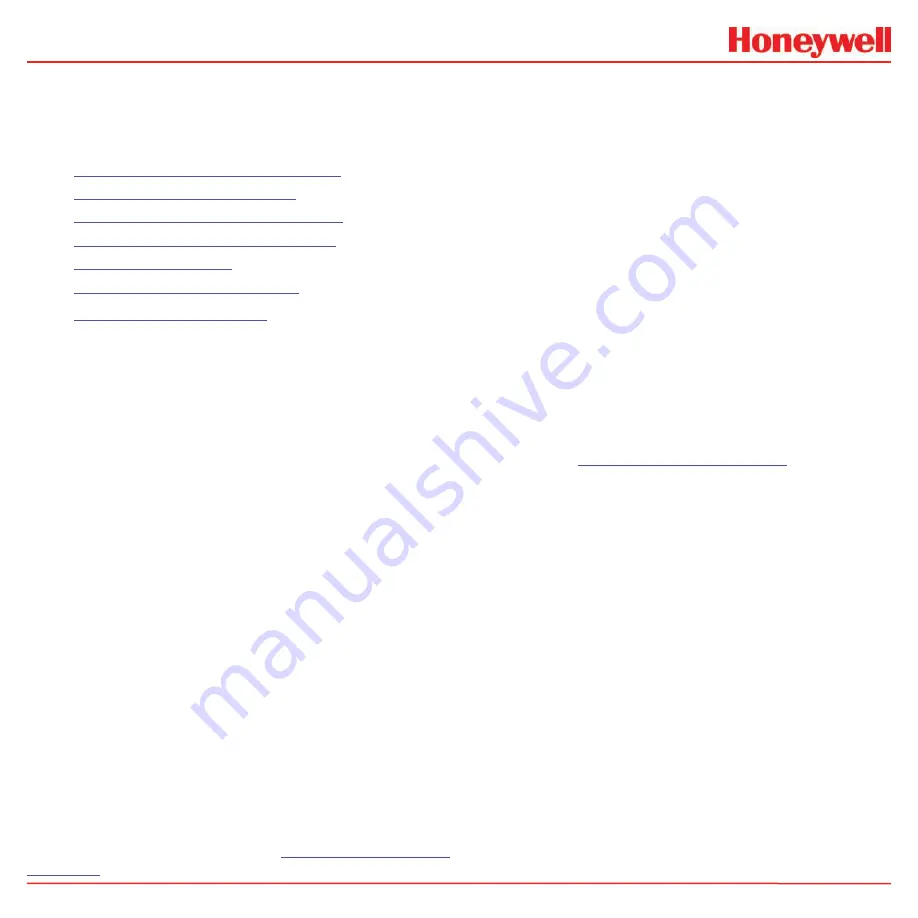
Vertex M
TM
24-Point Continuous Monitor
Section 2 - Installation
2-2
2.1 Introduction
The installation and initial start-up procedure for the
Vertex M System consists of seven steps, described
in this and the following sections:
•
2.2 Surveying the Installation Site
•
2.3 Optional Floor Mounting
•
2.4 Installing Sample Lines/Filters
•
2.5 Installing Pump Exhaust Line
•
2.6 Electrical Power
•
2.7 Data Acquisition System
•
2.8 Wiring Alarm Relays
2.2 Surveying the Installation Site
A survey of the site helps you make important decisions
before installing your Vertex M System. Topics in this
section assist you with appropriate placement of the
Vertex M System and in determining if you have special
filtering needs at the sampling location.
The site should:
• Be remote from the monitored location, not
sharing the atmosphere
• Have sufficient ventilation for cabinet cooling
• Have power available
• Be indoors in an area that is not subject to wide
variations in temperature and humidity.
Note:
The specified humidity is 20–65% RH and a temper-
ature between 59°F to 95°F (15°C to 35°C).
2.2.1 Placement of the Vertex M System
Install the Vertex M System in an environmentally-
protected setting remote from the manufacturing or
storage locations that it monitors.
Note:
Refer to the installation drawing in
Appendix A Installation
Drawings
for lifting/mounting information.
You can place the Vertex M System up to 400 ft. (122 m)
from sample locations.
2.2.2 Exposure to Dust and Humidity
Exposure to corrosive gases or materials, excess
moisture, dust and other unusual environmental
conditions could seriously hamper the Vertex M’s
monitoring ability and could damage the monitor.
Allow room around the Vertex M System for ventilation
and servicing.
2.2.3 Sample Transport Time
Install the Vertex M System central to all 24 sample
locations to achieve equal sample transport times
during monitoring. The shorter the sample line, the
shorter the response time. If monitoring a critical
location, it may be desirable to place the monitor near
that critical area to reduce sample transport time for that
location. See
Appendix B Specifications
for transport
times.
2.2.4 Monitor Dimensions
Monitor dimensions are important factors in monitor
placement. The Vertex M System is 24. in. (61 cm)
wide, 36 in. (91.4 cm) deep and 57 in. (144.8 cm) in
height. The system with 3 analyzers weighs about 550
pounds (249 kg). Allow for 24 in. (61 cm) door swing; 5
in. (12.3 cm) at rear and 5 in. (12.3 cm) on sides. Allow
clearance above monitor for installing sample lines.
2.2.5 Sample Locations
Before installing the Vertex M System, evaluate the
sampling locations to determine if excessive dust
or moisture are present. An external filter must be
used in all locations. Make sure you use the correct
filter. Dust may be a result of construction as well as
manufacturing activities. Moisture may occur from rain
entering a line at an outdoor sampling location or from
Summary of Contents for Vertex M
Page 8: ...1 1 Vertex MTM 24 Point Continuous Monitor Vertex M TM Technical Handbook 1 Introduction ...
Page 25: ...Vertex MTM 24 Point Continuous Monitor Section 1 Introduction 1 18 ...
Page 26: ...2 1 Vertex MTM 24 Point Continuous Monitor Vertex M TM Technical Handbook 2 Installation ...
Page 35: ...Vertex MTM 24 Point Continuous Monitor Section 2 Installation 2 10 ...
Page 36: ...3 1 Vertex MTM 24 Point Continuous Monitor Vertex M TM Technical Handbook 3 Startup ...
Page 40: ...Vertex MTM 24 Point Continuous Monitor Section 3 Startup 3 5 Figure 3 1 Vertex M Main Screen ...
Page 77: ...4 1 Vertex MTM 24 Point Continuous Monitor Vertex M TM Technical Handbook 4 Operation ...
Page 93: ...Vertex MTM 24 Point Continuous Monitor Section 4 Operation 4 17 Figure 4 9 Filter Options ...
Page 109: ...Vertex MTM 24 Point Continuous Monitor Section 4 Operation 4 33 ...
Page 125: ...5 1 Vertex MTM 24 Point Continuous Monitor Vertex M TM Technical Handbook 5 Maintenance ...
Page 134: ...Vertex MTM 24 Point Continuous Monitor Section 5 Maintenance 5 10 ...
Page 140: ...Vertex MTM 24 Point Continuous Monitor Section 5 Maintenance 5 16 ...
Page 141: ...6 1 Vertex M TM Technical Handbook 6 Troubleshooting ...
Page 164: ...Section 6 Troubleshooting 6 24 ...
Page 166: ...Vertex MTM 24 Point Continuous Monitor Appendix A Installation Drawings A 2 A 1 Introduction ...
Page 170: ...Vertex MTM 24 Point Continuous Monitor Appendix A Installation Drawings A 6 ...
Page 173: ...Vertex MTM 24 Point Continuous Monitor Appendix A Installation Drawings A 9 ...
Page 174: ...B 1 Vertex MTM 24 Point Continuous Monitor Vertex M TM Technical Handbook A Specifications ...
Page 178: ...C 1 Vertex MTM 24 Point Continuous Monitor Vertex M TM Technical Handbook A Detectable Gases ...
Page 193: ...Vertex MTM 24 Point Continuous Monitor Appendix A Replacement and Consumable Items D 4 ...
Page 240: ...Vertex MTM 24 Point Continuous Monitor Appendix A 4 20mA Analog Output Option G 4 ...
Page 250: ...Vertex MTM 24 Point Continuous Monitor Appendix A Warranty Statement I 4 ...