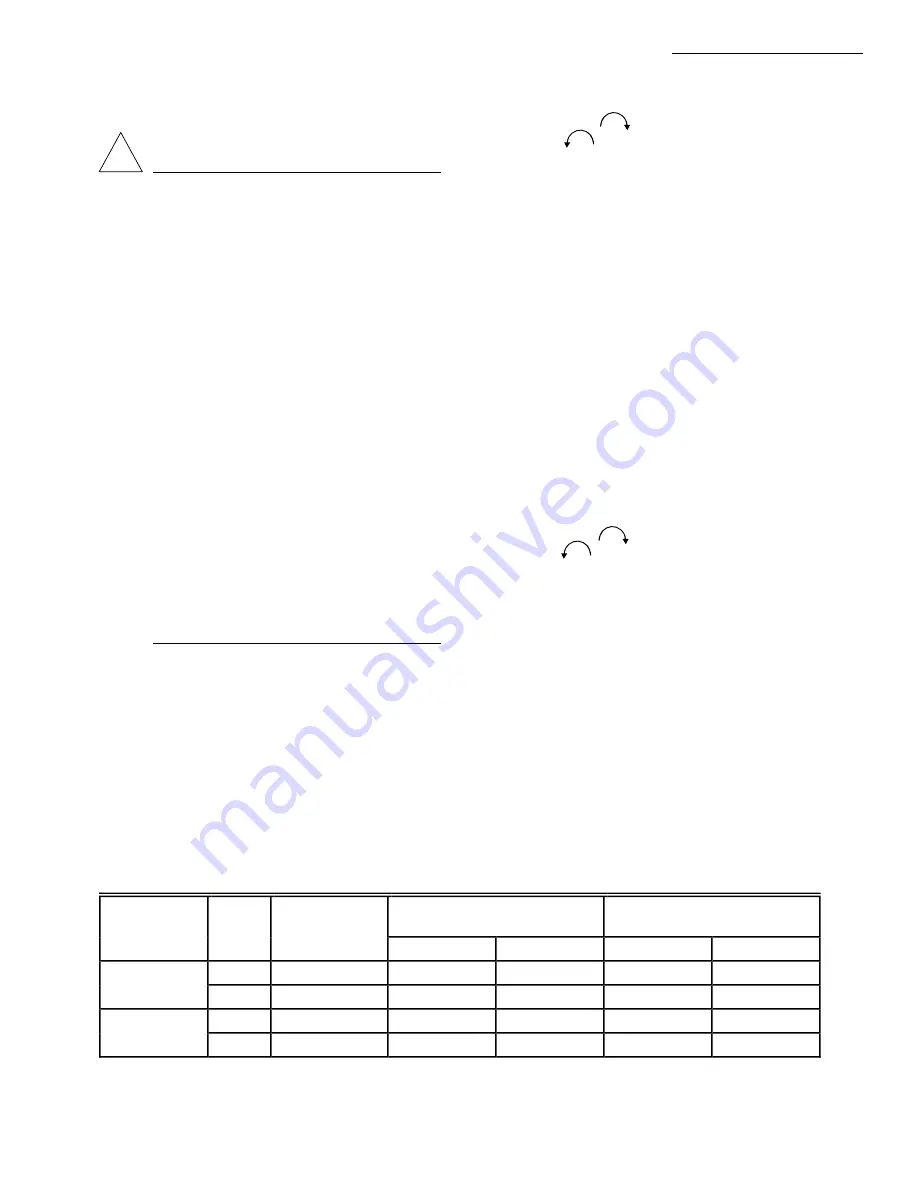
9
68-0047—2
VR8204; VR4204
STARTUP AND CHECKOUT
CHECK AND ADJUST GAS INPUT AND BURNER
IGNITION
CAUTION
1. Do not exceed input rating stamped on appli-
ance nameplate, or manufacturer recommended
burner orifice pressure for size orifice(s) used.
Make certain primary air supply to main burner
is properly adjusted for complete combustion.
Follow appliance manufacturer instructions.
2. IF CHECKING GAS INPUT BY CLOCK-
ING GAS METER. Make certain there is no
gas flow through the meter other than to the
appliance being checked. Other appliances must
remain off with their pilots extinguished (or
their consumption must be deducted from the
meter reading). Convert flow rate to Btuh as
described in form 70-2602, Gas Controls Hand-
book, and compare to Btuh input rating on
appliance nameplate.
3. IF CHECKING GAS INPUT WITH MANO-
METER: Be sure gas control is in OFF posi-
tion before removing outlet pressure tap plug
to connect manometer (pressure gauge). Also
turn gas control knob back to OFF when re-
moving gauge and replacing plug. Before re-
moving inlet pressure tap plug, shut off gas
supply at the manual valve in the gas piping to
the appliance or, for LP, at the tank. Also shut
off gas supply before disconnecting manom-
eter and replacing plug. Repeat Gas Leak Test
at plug with main burner operating.
Standard Pressure Regulator
1. Check the manifold pressure listed on the appliance
nameplate. Gas control outlet pressure should match the
nameplate.
2. With main burner operating, check gas control flow
rate using the meter clocking method or pressure using a
manometer connected to the outlet pressure tap on the gas
control. See Fig. 5.
3. If necessary, adjust pressure regulator to match ap-
pliance rating. See Table 4A or 4B for factory set nominal
outlet pressure and adjustment range.
a. Remove pressure regulator adjustment cap screw.
b. Using screwdriver, turn inner adjustment screw
clockwise
to increase or counterclock-
wise
to decrease gas pressure to burner.
c. Always replace cap screw and tighten firmly to
prevent gas leakage.
4. If desired outlet pressure or flow rate cannot be
achieved to adjusting the gas control, check gas control
inlet pressure using a manometer at the gas control inlet
pressure tap. If inlet pressure is in the nominal range (see
Table 4A or 4B), replace gas control. Otherwise, take the
necessary steps to provide proper gas pressure on the
control.
Slow-opening and Step-opening Pressure Regulators
1. Check the full rate manifold pressure listed on the
appliance nameplate. Gas control full rate outlet pressure
should match this rating.
2. With main burner operating, check gas control flow
rate using the meter clocking method or pressure using a
manometer connected to the outlet pressure tap on the gas
control. See Fig. 5.
3. If necessary, adjust pressure regulator to match ap-
pliance rating. See Table 4A or 4B for factory set nominal
outlet pressure and adjustment range.
a. Remove pressure regulator adjustment screw.
b. Using screwdriver, turn inner adjustment screw
clockwise
to increase or counterclock-
wise
to decrease gas pressure to burner.
c. Always replace cap screw and tighten firmly to
prevent gas leakage.
4. If desired outlet pressure or flow rate cannot be
achieved by adjusting the gas control, check gas control
inlet pressure using a manometer at the gas control inlet
pressure tap. If inlet pressure is in the nominal range (see
Table 4A or 4B), replace gas control. Otherwise, take the
necessary steps to provide proper gas pressure to the con-
trol.
5. STEP-OPENING PRESSURE REGULATORS
ONLY. Carefully check burner lightoff at step pressure.
Make sure burner lights smoothly and without flashback to
orifice. Make sure all ports remain lit. Cycle burner several
times, allowing at least 30 seconds between cycles for
regulator to resume step function. Repeat after allowing
burner to cool. Readjust full rate outlet pressure, if neces-
sary, to improve lightoff characteristics.
!
TABLE 4A—PRESSURE REGULATOR SPECIFICATION PRESSURES (in. wc)
Model
Type
Nominal Inlet
Factory Set
Nominal Outlet Pressure
Setting Range
Type
of Gas
Pressure Range
Step
Full Rate
Step
Full Rate
Standard,
Natural
5.0 - 7.0
—
3.5
—
3.0 - 5.0
slow-opening
LP
12.0 - 14.0
—
10.0
—
8.0 - 12.0
Step-opening
Natural
5.0 - 7.0
0.9
3.5
—
3.0 - 12.0
LP
12.0 - 14.0
2.2
10.0
—
8.0 - 12.0
Summary of Contents for TRADELINE VR8204A
Page 15: ...15 68 0047 2 ...