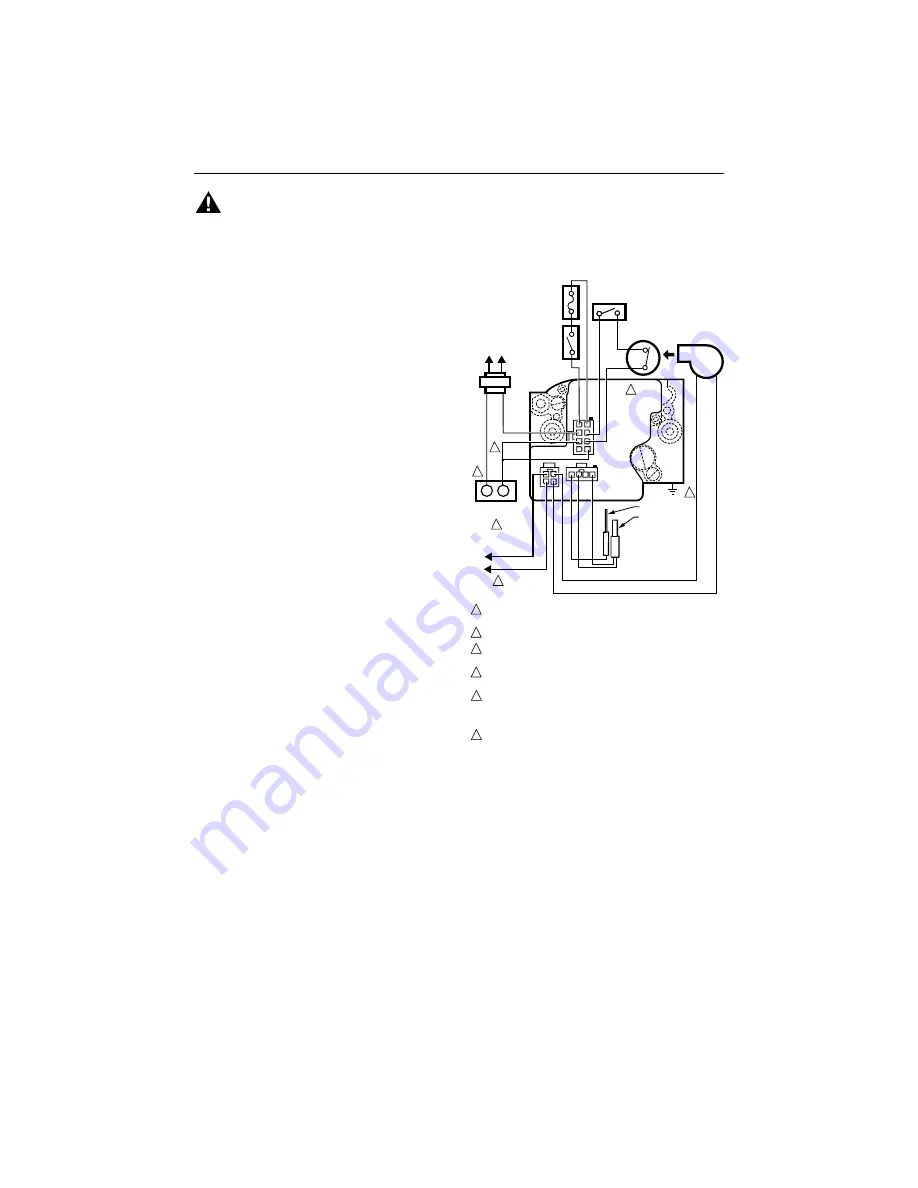
SV9520H SMARTVALVE™ SYSTEM CONTROL LINE VOLTAGE POLARITY SENSE MODELS
69-1383
10
WARNING
Electrical Shock Hazard.
Can cause property damage, severe
injury or death.
Only a trained, experienced service technical should
perform this troubleshooting.
1. Make sure the appliance power is on and any
manually operated gas cock on the appliance
is open.
2. Remove the appliance burner compartment
door. Confirm that SV9520 LED indicator is
flashing in a "bright - dim" sequence.
3. Make sure the ignition system control switch is
in the ON position.
4. Disconnect the system thermostat leadwires at
the ST9160 EFT or the 208907 Terminal
Board.
5. Using alligator clips on a short jumper wire,
jumper the R and W terminals on the EFT or
Terminal Board.
6. Observe the appliance operation, comparing it
to the Sequence of Operation shown in Fig. 11.
Allow the ignition sequence to proceed until the
appliance lights or an abnormal or unexpected
event is observed.
1.
Check the appliance as shown in Table 10.
Troubleshooting Without LED Indicator
Assistance.
1.
Turn off power to appliance.
2.
Remove appliance burner compartment door and
disconnect thermostat from the ST9160 EFT or the
208907 Terminal Board.
3.
Make sure the ignition system switch on the
SmartValve is in the ON position.
4.
Turn appliance power on
5.
Using alligator clips on a short jumper wire, jumper
the R and W terminals on the EFT or Terminal
Board.
6.
Observe appliance operation, comparing it to the
Sequence of Operation shown in Fig. 11. Allow the
ignition sequence to proceed until the appliance
lights or an abnormal or unexpected event is
observed. Be sure to wait long enough for one of
the LED diagnostic codes to flash.
7.
Observe the LED indicator on the SmartValve;
check and repair the system as noted in Table 10.
8.
After analysis and repair are complete, turn off
appliance power and reconnect thermostat.
9.
Turn on appliance power and generate a call for
heat.
10.
Observe appliance operation, comparing it to the
Sequence of Operation shown in Fig.11.
11.
If appliance operation is not consistent with
Sequence of Operation, repeat troubleshooting
procedures.
Fig. 9. SV9520 typical wiring connections
direct to the system thermostat.
C1
C2
C3
LOAD
COMMON
THERMOSTAT
POWER SUPPLY. PROVIDE DISCONNECT MEANS AND OVERLOAD
PROTECTION AS REQUIRED.
CONNECT 120V (HOT) LEAD AS SHOWN.
APPLIANCE CHASSIS MUST HAVE RELIABLE CONNECTION TO
EARTH GROUND.
DATA AND R LINES MUST BE CONNECTED TO W ON THERMOSTAT
FOR PROPER SYSTEM OPERATION.
THERMOSTAT MUST HAVE ZERO OFF-STATE CURRENT DRAW.
MECHANICAL SWITCH THERMOSTATS RECOMMENDED. TRIAC
SWITCH THERMOSTATS OR POWER-STEALING THERMOSTATS
ARE NOT RECOMMENDED.
IN THIS APPLICATION, POSTPURGE FUNCTION IS NOT AVAILABLE
AND THE LED FUNCTIONS ONLY DURING A CALL FOR HEAT.
1
4
5
6
6
3
2
2
5
4
1
M17608
AIR
PROVING
SWITCH
NEUTRAL
HOT
L2
L1
(HOT)
TO
120 VAC, 60 HZ
POWER SUPPLY
ROLL-OUT
SWITCH
LIMIT
SWITCH
COMBUSTION
AIR BLOWER
R
W
R
C
AIR
DATA
40 VA
TRANSFORMER
L1
L2
SV9520
HOT
SURFACE
IGNITER
FLAME ROD
3
AUXILIARY
LIMIT SWITCH
(OPTIONAL)
1
1
2
5
6
7
8
3
2
2
3
3
1
4
4
4