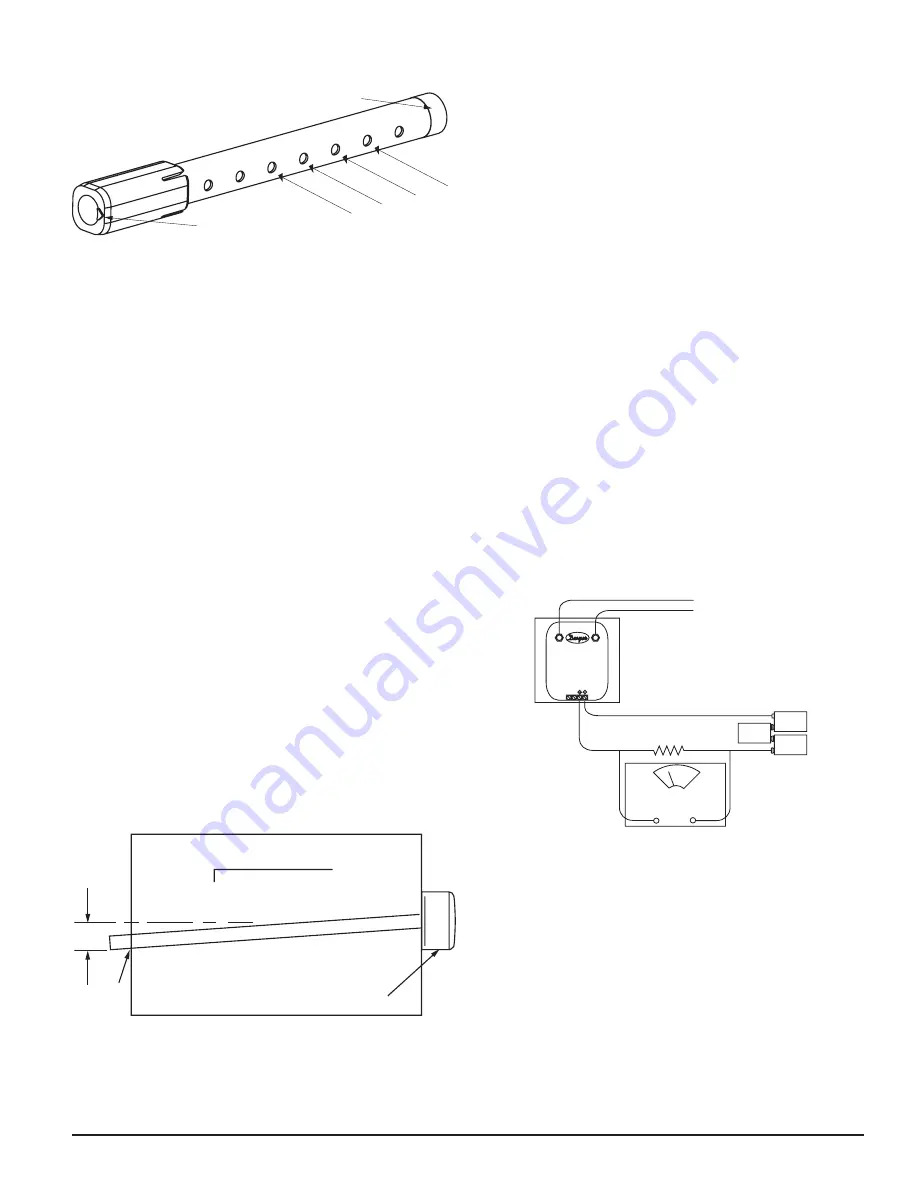
[5.3] MODIFICATIONS OF SAMPLING TUBES
There may be applications where duct widths are not what is specified for the
installation . In such cases, it is permissible to modify a sampling tube that is
longer than necessary to span the duct width .
Use a 0 .193-inch diameter (#10) drill and add the appropriate number of holes
so that the total number of holes exposed to the air flow in the duct is 10 to 12 .
Space the additional holes as evenly as possible over the length of the tube .
CAUTION:
This procedure should only be used as a temporary fix . It is not
intended as a permanent substitute for ordering the correct length tubes .
[5.4] REMOTE SAMPLING TUBE INSTALLATION
The detector arrangement can also incorporate the remote mounting of the
sampling tube and/or exhaust tube . In this case both the detector, sampling
tube and exhaust tube (if included) should be rigidly mounted to withstand
the pressure and vibrations caused by the air velocity . The location of the
detector’s sampling tube should be such that there is uniform airflow in the
cross section area .
Pressure differential across the sampling and exhaust ports in the detector hous-
ing shall be verified to be between 0 .01 and 1 .11 inches of water . Do so by
measuring the pressure difference between the inlet and outlet ports on the
detector housing using a manometer as described in the Measurement Tests
section of this manual .
[6] MEASUREMENT TESTS
[6.1] AIR FLOW
The SK-Duct is designed to operate over an extended air speed range of 100
to 4000 FPM . To verify sufficient sampling of ducted air, turn the air handler
on and use a manometer to measure the differential pressure between the two
sampling tubes . The differential pressure should measure at least 0 .01 inches
of water and no more than 1 .11 inches of water . Because most commercially
available manometers cannot accurately measure very low pressure differen-
tials, applications with less than 500 FPM of duct air speed may require one
of the following: 1) the use of a current-sourcing pressure transmitter (Dwyer
Series 607) or 2) the use of aerosol smoke, see below for test descriptions .
[6.2] LOW FLOW AIR FLOW TEST USING DWYER SERIES 607
DIFFERENTIAL PRESSURE TRANSMITTER
Verify the air speed of the duct using an anemometer . Air speed must be at
least 100 FPM . Wire the Dwyer transmitter as shown in
Figure 5
. Connect the
leads of the meter to either side of the 1000
Ω
resistor . Allow unit to warm up
for 15 seconds . With both HIGH and LOW pressure ports open to ambient air,
measure and record the voltage drop across the 1000
Ω
resistor (measurement
1), 4 .00 volts is typical . Using flexible tubing and rubber stoppers, connect the
HIGH side of the transmitter to the sampling tube of the duct smoke detec-
tor housing, and the LOW side of the transmitter to the exhaust tube of the
duct smoke detector housing . Measure and record the voltage drop across the
1000
Ω
resistor (measurement 2) . Subtract the voltage recorded in measure-
ment 1 from the voltage recorded in measurement 2 . If the difference is greater
than 0 .15 volts, there is enough air flow through the duct smoke detector for
proper operation .
FIGURE 3. AIR DUCT DETECTOR SAMPLING TUBE:
SAMPLING TUBE ENDCAP
ARROW MUST FACE
INTO AIR FLOW
AIR FLOW
DIRECTION
CAUTION:
The sampling tube end cap, included with the detector, is criti-
cal to proper operation of the duct smoke detector . The end cap is needed to
create the proper air flow to the sensor of the duct smoke detector . Once any
sampling tube length adjustments are made, plug the end of the sampling tube
with the provided end cap .
A plastic exhaust tube is included with the unit to be installed if needed . In-
stall into the housing connection that is downstream from the sampling tube
connection . The exhaust tube can be installed from the front of the detector
or the back . A longer 1 foot exhaust tube, model ETX, is available as an acces-
sory in cases where the molded exhaust tube does not extend at least 2 inches
into the duct .
[5.2] SAMPLING TUBE INSTALLATION
1 . For tubes shorter than the width of the duct, slide the sampling tube,
with installed end cap, into the housing connection that meets the air-
flow first . Position the tube so that the arrow points into the airflow as
shown in Figure 3 . Per NFPA sampling tubes over 3 feet long should be
supported at the end opposite of the duct detector . In ducts wider than 8
feet, work must be performed inside the duct to couple the other section
of the sampling tube to the section already installed using the ½-inch
conduit fitting supplied . Make sure that the holes on both sections of the
air inlet sampling tube are lined up and facing into the airflow .
2 . For tubes longer than the width of the air duct, the tube should extend
out of the opposite side of the duct . Drill a ¾-inch hole in the duct op-
posite the hole already cut for the sampling tube . Ensure that the sam-
pling tube is angled downward from the duct smoke detector to allow for
moisture drainage away from the detector . The sampling tube should be
angled at least
1
⁄
4
˝ downward for every 12˝ of duct width per Figure 4 .
There should be 10 to 12 holes spaced as evenly as possible across the
width of the duct . If there are more than 2 holes in the section of the tube
extending out of the duct, select a shorter tube using Table 1 . Otherwise,
trim the tube to leave approximately 1 to 2 inches extending outside the
duct . Plug the end with the end cap and tape closed any holes in the
protruding section of the tube . Be sure to seal the duct where the tube
protrudes .
FIGURE 4.
DETECTOR
3
/
4
˝
HOLE
12˝
1
/
4
˝
2˝
NOTE:
Air currents inside the duct may cause excessive vibration, especially
when the longer sampling tubes are used . In these cases, a 3-inch floor flange
(available at most plumbing supply stores) may be used to fasten the sam-
pling tube to the other side of the duct . When using the flange/connector
mounting technique, drill a 1 to 1¼-inch hole where the flange will be used .
HIGH
LOW
9 VOLT
BATTERY
9 VOLT
BATTERY
9 VOLT
BATTERY
TO SAMPLING TUBE
TO EXHAUST TUBE
DIFFERENTIAL
PRESSURE
TRANSMITTER
MODEL #607-01
15 TO 36
VDC SUPPLY
1000 OHM 5%
1 WATT RESISTOR
VOLT METER FLUKE
MODEL 87 OR
EQUIVALENT
+
–
H0163-01
FIGURE 5. PROCEDURE FOR VERIFYING AIR FLOW:
H0215-00
H0551-00
3
I56-3432-006
04-12