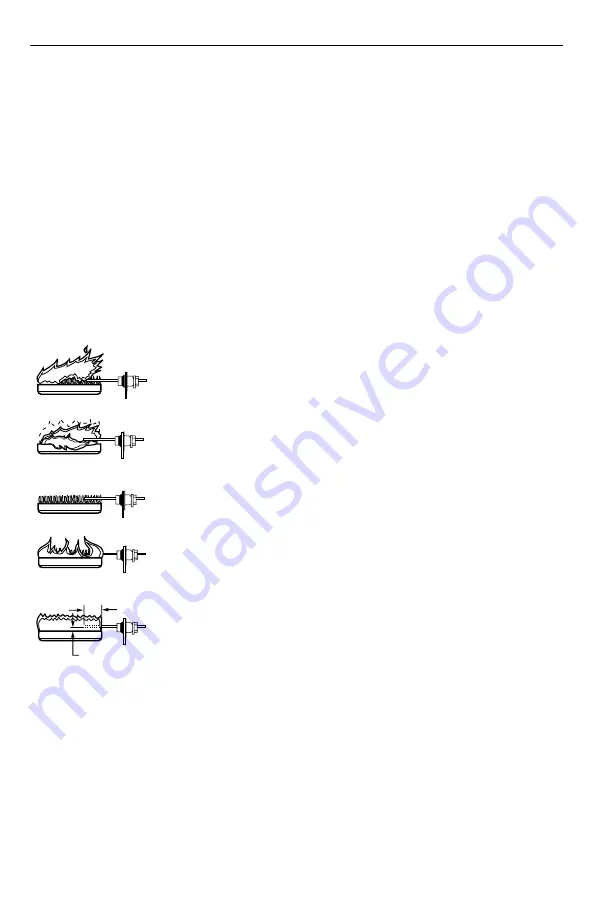
69-1174
9
S8701/S8702 DIRECT SPARK IGNITION CONTROLS
CHECK BURNER FLAME CONDITION
NOISY LIFTING FLAME
BURNER
WAVING FLAME
SMALL BLUE FLAME
LAZY YELLOW FLAME
GOOD RECTIFYING FLAME
1 IN. (25.4 MM)
1/4 TO 1/2 IN. (6.4 TO 12.7 MM)
M18055
CHECK FOR:
• HIGH GAS PRESSURE
• EXCESS PRIMARY AIR
OR DRAFT
CHECK FOR:
• POOR DRAFT
• EXCESS DRAFT
• HIGH VELOCITY OR
SECONDARY AIR
INSTALL SHIELD IF NECESSARY.
CHECK FOR:
• CLOGGED PORTS OR
ORIFICE FILTER
• WRONG SIZE ORIFICE
CHECK FOR
LACK OF AIR FROM:
• DIRTY PRIMARY
AIR OPENING
• LARGE PORTS
OR ORIFICES
Low or Unsteady Flame Current
If the current to the S8701/S8702 is less than 1.0
µ
A or is
unsteady, check the burner flame, flame sensor location
and electrical connections as follows:
Burner Flame
The flame sensor must be constantly immersed in flame.
Check burner flame conditions as shown in Fig. 8.
Flame Sensor
The flame signal is best when about 1 inch. (25 mm) of
flame rod is immersed in the burner flame. A bent flame
rod, bent mounting bracket or cracked ceramic insulator
can affect flame signal. Replace flame sensor if necessary.
Electrical Connections and Shorts
Connections at the flame sensor must be clean and tight. If
wiring needs replacement, use moisture resistant no. 18
AWG wire rated for continuous duty up to 105
°
C (221
°
F).
Fig. 8. Check Burner Flame Conditions.
Checkout After Service
Perform the following steps before leaving the job (de-
scribed in the CHECKOUT section).
•
START SYSTEM
•
TRIAL FOR IGNITION PERIOD CHECK
•
SAFETY LOCKOUT RESET
Also perform any other checks recommended by the
heating appliance manufacturer if system components
other than the S8701 or S8702 were serviced.
TROUBLESHOOTING GUIDE
Start the system by setting the thermostat or temperature
control to call for heat. Observe the system response and
establish the type of malfunction or deviation from normal
operation by using the troubleshooting guide. After any
maintenance or repair, the troubleshooting sequence
should be repeated until normal system operation is
obtained.