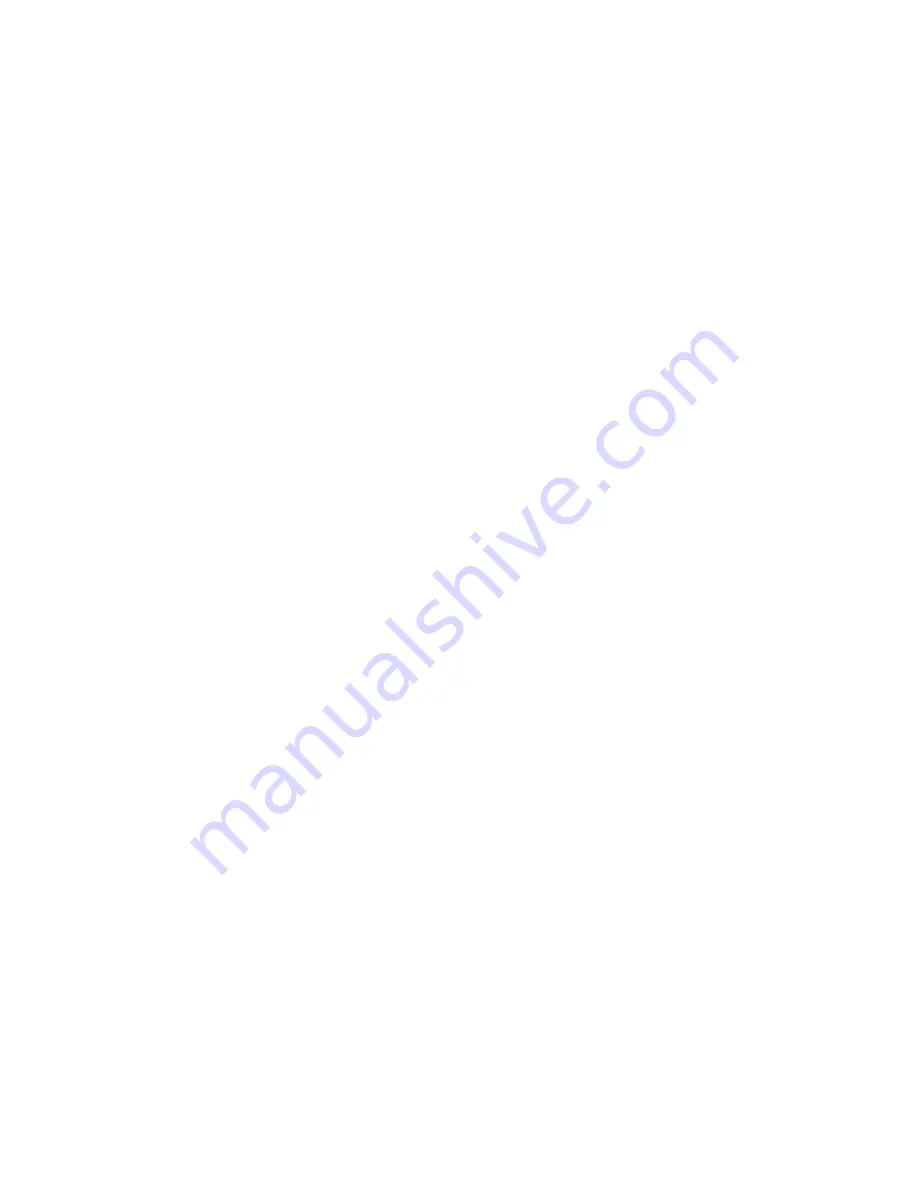
RM7890, RM7895 100 Vac
c .
KDM: The KDM is powered from a low voltage, ener-
gy-limited source, so it can be mounted outside of the
control panel if it is protected from mechanical damage.
NOTE: Use a separate 13 Vdc power supply any time more
than two Data ControlBus™ Modules or KDM are
used or when placed more than 100 feet (30 meters)
from the relay module .
d .
Remote Reset Module:
(1) Do not run high voltage ignition transformer wires
in the same conduit with the Remote Reset Module
wiring.
(2) Do not route Remote Reset Module wires in conduit
with line voltage circuits.
8 .
Maximum wire lengths:
a .
For the relay module, the maximum length of leadwire
to the control terminal input is 300 feet (91 meters).
b .
For the flame detector leadwires, the maximum flame
sensor leadwire length is limited by the flame signal
strength.
c .
Remote Reset Module leadwires: The maximum length
of wire is 1000 feet (305 meters) to a Remote Reset
Module pushbutton.
d .
Data ControlBus™ or Modbus™ Module: The maximum
cable length depends on the number of system modules
connected, the noise conditions, and the cable used.
The maximum length of all interconnecting wires is
1000 feet (305 meters).
9 .
Make sure loads do not exceed the terminal ratings. Refer
to the label on the relay module or to the ratings in the
Specifications section. See Table 1.
10 .
Check the power supply circuit to be sure the voltage and
frequency tolerance match those of the relay module. A
separate power supply circuit can be required for the relay
module with the required disconnect means and overload
protection added.
11 .
Check all wiring circuits and complete the Static Checkout,
see Table 8, before installing the relay module on the wir-
ing subbase.
12 .
Install all electrical connectors.
13 .
Restore power to the panel.
ASSEMBLY
Mounting RM7890; RM7895
NOTE: For installation dimensions, see Fig . 1 or 2 .
Relay Module Mounting
1 .
Mount the relay module vertically, see Fig. 8 or 9, or mount
horizontally with the knife blade terminals pointing down-
ward. When mounting on the Q7800A Wiring Subbase, the
relay module must be in an electrical enclosure.
2 .
Select the location in the electrical enclosure. Be sure to
allow adequate clearance for servicing, installation and
removal of the relay module, dust cover, flame amplifier,
flame amplifier signal voltage probes, electrical signal volt-
age probes and electrical connections.
a .
Allow an additional two inches (51 mm) below the relay
module for the flame amplifier mounting.
b .
Allow an optional three-inch (76 mm) minimum to both
sides of the relay module for electrical signal voltage
probes.
3 .
Make sure subbase wiring does not project beyond the
terminal blocks. Tuck in wiring against the back of the sub-
base so it does not interfere with the knife blade terminals
or bifurcated contacts.
IMPORTANT
The relay module must be installed with a plug-in motion
rather than a hinge action.
4 .
Mount the relay module by aligning the four L-shaped cor-
ner guides and knife blade terminals with the bifurcated
contacts on the wiring subbase and securely tightening
the two screws without deforming the plastic.
Dust Cover Mounting
1 .
Align the interlocking ears of the dust cover with the two
mating slots in the relay module, see Fig. 10.
2 .
Insert the two interlocking ears into the two mating slots,
and with a hinge action, push on the upper corners of the
dust cover to secure it to the relay module.
3 .
Be sure the dust cover is firmly in place.
Installing ST7800 Purge Card (RM7895 Only)
1 .
Remove the dust cover, KDM, Data ControlBus™ Module, or
extension cable assembly.
2 .
Remove the current ST7800 Purge Card from the relay
module by pulling upward on the plastic support cover.
See Fig. 11.
3 .
Make sure that the ST7800 Purge Card selected has the
desired purge timing.
4 .
Insert the ST7800 Purge Card into the opening of the relay
module purge card compartment. See Fig. 11.
Installing Plug-In Flame Signal Amplifier
1 .
Disconnect the power supply before beginning installation
to prevent electrical shock and equipment damage. More
than one disconnect can be involved.
2 .
Align the amplifier circuit board edge connector with the
keyed receptacle on the relay module. Verify that the am-
plifier nameplate faces away from the relay module. See
Fig. 12.
3 .
Push in the amplifier until the circuit board is fully inserted
into the receptacle and then push the amplifier toward the
relay module retaining clasp.
4 .
Verify the amplifier is firmly in place.
5 .
Perform all required checkout tests.
Installing Flame Detector
NOTE: See Table 5 for the flame detection system available
for use with the relay module . Make sure the correct
combination of amplifier and flame detector is used .
13
32-00216-01