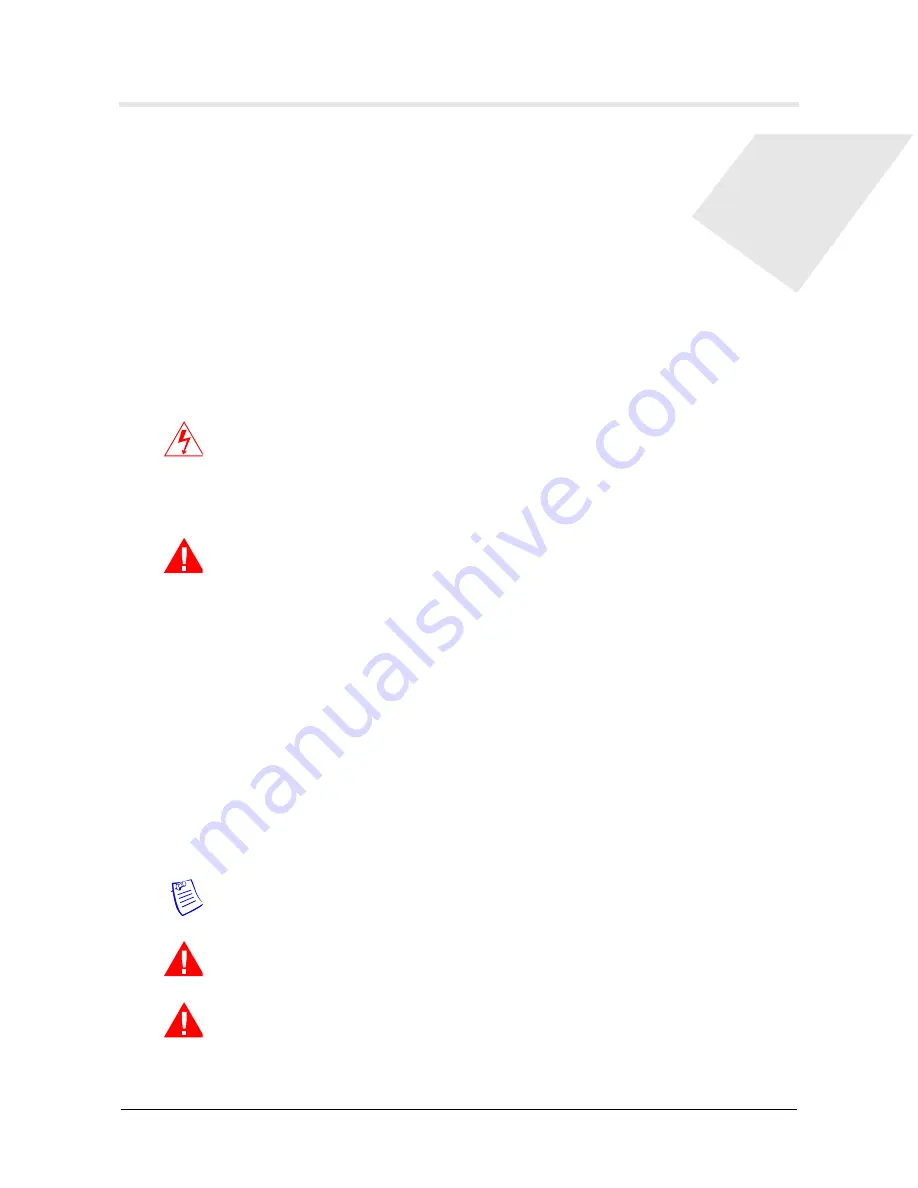
PW-6000 Two-Reader Module Installation Guide
,
Document 800-01951, Revision C
v
Notices
Warnings and Cautions
Warning:
Be
Before connecting the device to the power supply, verify that the output voltage is
within specifications of the power supply.
Do not apply power to the system until
after
the installation has been completed.
Personal injury or death could occur, and the equipment could be damaged beyond
repair, if this precaution is not observed!
Warning: Fire Safety and Liability Notice
Never connect card readers to any critical entry, exit door, barrier, elevator, or gate
without providing
an alternative exit
in accordance with all fire and life safety codes
pertinent to the installation. These fire and safety codes vary from city to city and you
must get approval from local fire officials whenever using an electronic product to
control a door or other barrier. Use of egress buttons, for example, may be illegal in
some cities. In most applications, single action exit without prior knowledge of what
to do is a life safety requirement. Always make certain that any required approvals are
obtained in writing. DO NOT ACCEPT VERBAL APPROVALS, BECAUSE THEY
ARE NOT VALID.
Honeywell never recommends using the PW-6000 or related products for use as a
primary warning or monitoring system. Primary warning or monitoring systems
should always meet local fire and safety code requirements. The installer must also
test the system on a regular basis by instructing the end user in appropriate daily
testing procedures. Failure to test a system regularly could make the installer liable for
damages to the end user if a problem occurs.
Note:
See the Remote Enclosure Installation manuals for
PW5K2ENC1/PW5K2ENC2 or PW5K1ENC3 for installation instructions.
Warning:
EARTH GROUND all enclosures for proper installation.
Warning:
Use suppressors on all door strikes. Use S-4 suppressors for installation. Honeywell
recommends only DC strikes.