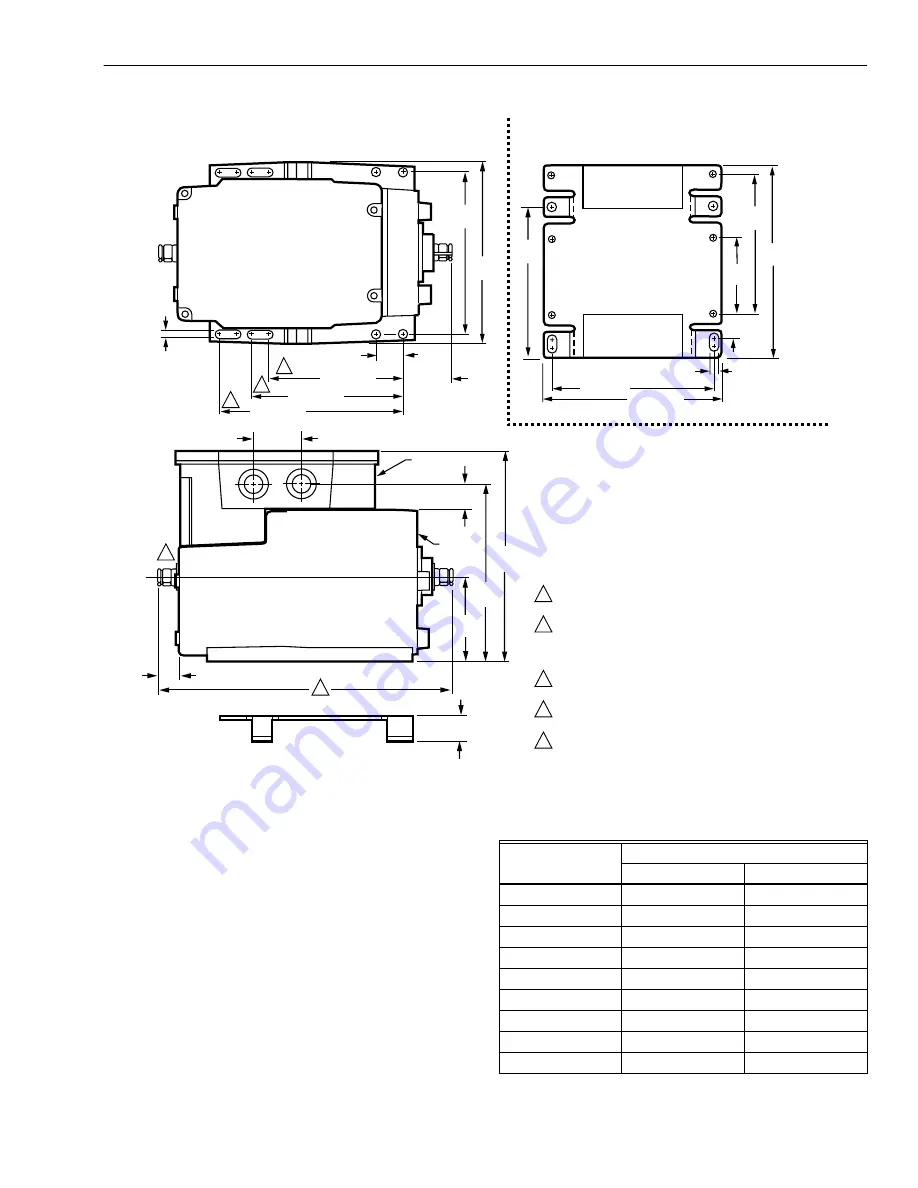
SERIES 72 MODUTROL IV™ MOTORS
3
63-2202—4
Fig. 1. Series 72 Modutrol IV Motor dimensions in in. (mm).
Controller: These motors can be used with any electronic
controller that provides a stable noise-free proportional
current output as specified in Electrical Ratings, Input
Range below.
Electrical Ratings:
Power Consumption: See Table 2.
Input Range:
Current, Nonadjustable: 4 to 20 mA nominal, 25 mA
maximum.
Current, Adjustable: 4 to 20 mA adjustable, 50 mA
maximum.
Zero/Null (Motor Closed): 0.08 to 18 mA.
Span: 1.8 to 18 mA.
Voltage, Nonadjustable: 2 to 10 Vdc.
Input Impedance:
4 to 20 mA Input: 100 ohms.
2 to 10 Vdc Input: 400K ohms.
Table 2. Series 72 Modutrol IV Motor Power
Consumption Ratings (at 120 Vac, 50/60 Hz).
M17089BB
4-7/8
(124)
5-1/2
(140)
13/16
(20)
4-1/16 (103)
1/4
(7)
1-1/2 (37)
4-1/16 (103)
4-1/16 (103)
WIRING
BOX
MOTOR
AUXILARY
END
POWER
END
ADAPTER
BRACKET
2-9/16
(66)
5-3/8
(137)
6-7/16
(164)
9/16 (15)
3/4
(19)
TOP VIEW OF BRACKET
TOP VIEW
4-5/8
(116)
4-1/4
(107)
2-5/16
(58)
11/16
(17)
4-7/8 (124)
5-9/16 (141)
1/4 (7)
5-13/16
(148)
2
POWER END
1
3
4
5
1-1/2 (37)
3/4
(19)
SPRING RETURN MODEL SHOWN
SOME MODELS DO NOT HAVE AN AUXILIARY
SHAFT. ALL OTHER DIMENSIONS ARE THE SAME.
FOR HIGH TORQUE (60 LB-IN.) SPRING RETURN
MODELS 8-3/4 (222); FOR LOW TORQUE (25 LB-IN.)
SPRING RETURN MODELS 8-1/4 (210);
NON-SPRING RETURN MODELS 7-5/16 (185).
FOR HIGH TORQUE (60 LB-IN.) SPRING
RETURN MODELS (SHOWN).
FOR LOW TORQUE (25 LB-IN.) SPRING
RETURN MODELS.
FOR NON-SPRING RETURN MODELS.
1
2
3
4
5
Model
Power Consumption
Watts
Amps
M7261
19
0.20
M7272
26
0.26
M7274
15
0.71
M7281
23
0.24
M7282
28
0.28
M7284
23
0.24
M7285
28
0.28
M7286
23
1.00
M7294
23
0.24