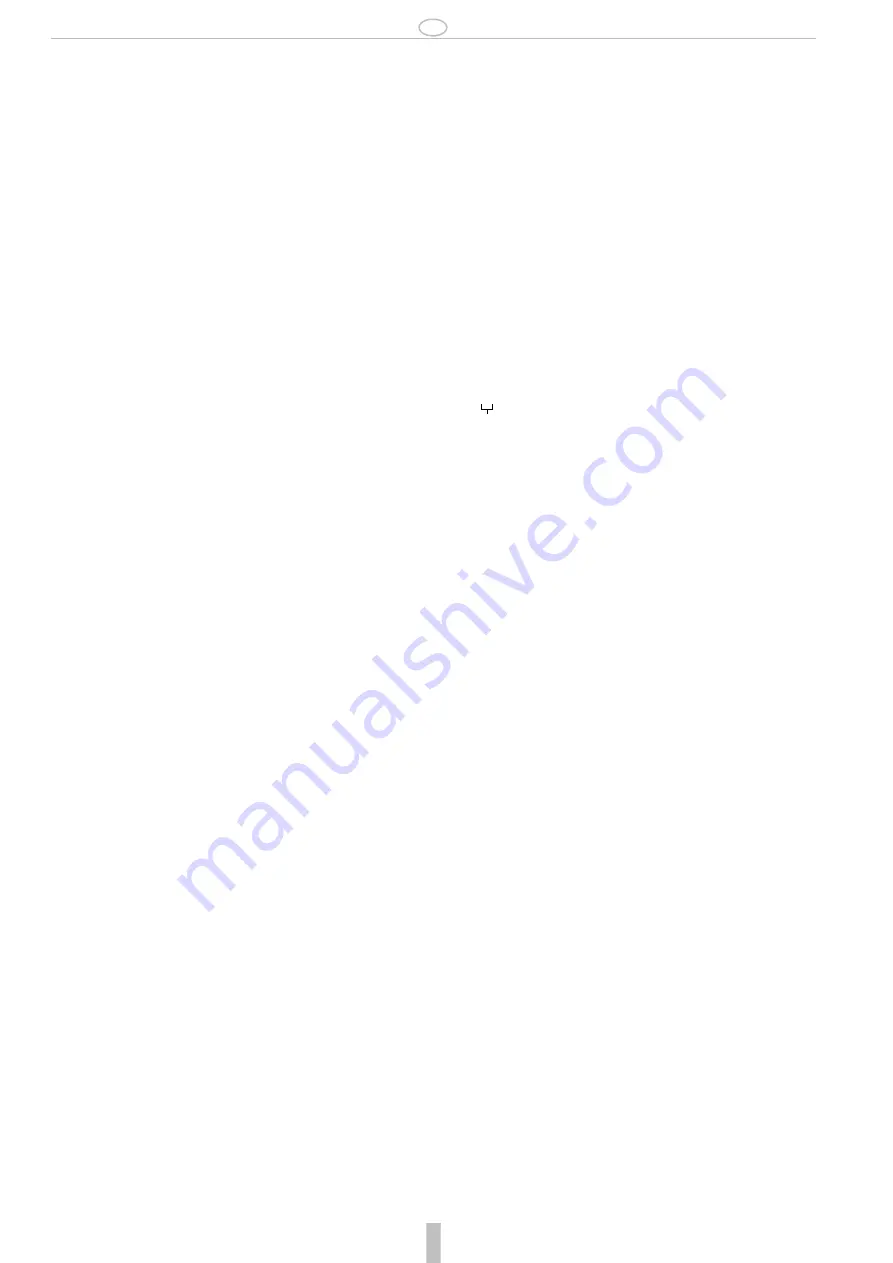
Honeywell GmbH
7
MU1H-1155GE23 R0912
GB
1. Safety Guidelines
1. Follow the installation instructions.
2. Use the appliance
•
according to its intended use
•
in good condition
•
with due regard to safety and risk of danger.
3. Note that the appliance is exclusively for use in the applications detailed
in these installation instructions. Any other use will not be considered to
comply with requirements and would invalidate the warranty.
4. Please take note that any assembly, commissioning, servicing and adju-
stment work may only be carried out by authorized persons.
5. Immediately rectify any malfunctions which may influence safety.
2. Description of function
Spring loaded check valves have a moving seal disc which is lifted off the seat
by a greater or lesser amount depending on the flow rate through the valve.
If the flow falls towards zero, then the spring pushes the disc back onto the
seat and seals the waterway.
To ensure continuing correct function it is recommended that check valves be
regularly checked and maintained (as specified in EN 1717).
The filter insert is divided into two parts. In the „filtering“ position, only the
lower, larger section is rinsed through by water jets from outside to inside.
The small upper section does not come in contact with unfiltered water. When
the ball valve is opened for reverse rinsing, then the whole filter insert is
pushed downwards until the water supply to the outer side of the main filter is
stopped. Simultaneously, the water flow is opened to the upper part of the
filter. The water needed for cleaning the filter passes through the upper filter
section, then the rotating impeller and the main filter from inside to outside,
i.e. the filter is reverse rinsed with filtered water. In that way the upper filter is
also cleaned by jets from the impeller. The filter automatically switches back
to the operating position when the ball valve is closed again.
Spring loaded pressure reducing valves operate by means of a force equali-
sing system. The force of a diaphragm operates against the force of an adjus-
tment spring. If the outlet pressure and therefore diaphragm force fall
because water is drawn, the then greater force of the spring causes the valve
to open. The outlet pressure then increases until the forces between the
diaphragm and the spring are equal again.
The inlet pressure has no influence in either opening or closing of the valve.
Because of this, inlet pressure fluctuation does not influence the outlet pres-
sure, thus providing inlet pressure balancing.
3. Application
4. Technical data
5. Scope of delivery
The water station comprises:
•
Check valve with
- Housing and housing end casing with flanges
- Check valve insert
- Test and drain plugs
- Disc, guide, spring, disc lip seal ring
•
Fine filter with
- Housing with flanges
- Pressure gauge
- Fine filter in brass filter bowl
- Ball valve with lever and drain connection
•
Pressure reducing valve with
- Housing with PN16 flanges per ISO7005-2, EN1092-2
- Spring bonnet with adjustment screw
- Adjustment spring
- Cartridge insert
- Pressure gauge
6. Options
7. Assembly
7.1. Installations Guidelines
•
Install in horizontal pipework with test and drain plugs and filter bowl down-
wards and spring bonnet upwards
- This position ensures optimum draining and filter efficiency
•
Install shutoff valves
- Shutoff valves provide optimal serviceability
•
Ensure good access
- Pressure gauge can be read off easily
- Simplifies maintenance and inspection
•
The installation location should be protected against frost
•
Fit immediately after water meter
- Corresponds to DIN 1988, Part 2
•
Provide a straight section of pipework of at least five times the nominal
valve size after the pressure reducing valve (in accordance with DIN
EN806 part 2)
7.2. Assembly instructions
1. Thoroughly flush pipework
2. Install pressure reducing valve
•
Note flow direction
•
Install without tension or bending stresses
3. Seal in pressure gauge
7.3. Discharge of reverse rinsing water
The reverse rinsing water must be routed to the drain channel in such a way
that no backwater can occur.
To do this there are 3 options:
1. Direct connection:
•
Connector DN 50/70 as well as the necessary pipes and siphon (3
elbows 90°) in DN 70.
2. Discharge into floor drain
3. Drain into open container.
*at 4 bar inlet pressure and 25 s reverse rinsing duration
Medium
Drinking water
Inlet pressure
Max. 16 bar
Outlet pressure
1.5 - 6.5 bar
Installation position
Horizontal with filter bowl downwards
Connection size
DN 65 - DN 100
Flanges on inlet and outlet
Flanges PN16 acc. to DIN86021 /
ISO 7005-2, EN 1092-2
The filter is constructed for drinking water installations. In case of a process water application the filter
has to be proven individually.
Operating temperature
Max. 65 °C
Nominal pressure
PN16
Minimum pressure drop
1.0 bar
Opening pressure check valve
ca. 0.05 bar
Operating pressure
Min. 2.0 bar
Max. 16.0 bar
Diaphragm pressure loading
Max. 9.0 bar
Connection size
DN 65 - DN 100
HS10S-...FA = Standard version with flanges PN16, Filter mesh size 100
μ
m
Connection size
Filter size
Reverse rinsing volume*
DN65 - 100
15 litre